(includes GRI indicators EC2, EN5, EN6, EN7, EN18)
ABB has been in the energy business for 120 years. Our technologies are used along the entire energy value chain, from the extraction of resources and their transformation into electricity, liquified natural gas or refined petroleum products, to their efficient use in industry, transportation and buildings. We help our customers to use electrical power effectively and to increase industrial productivity in a sustainable way.
The link between energy efficiency and mitigating climate change is clear. According to the 2010 World Energy Outlook, published by the International Energy Agency, more than 70 percent of projected CO2 emission reductions by 2020 can be delivered by energy efficiency. A combination of energy efficiency measures and renewable power generation could deliver almost 70 percent of the required emissions reduction over the next two decades.
ABB has identified mitigation of climate change and energy efficiency as key drivers for all parts of our business and we are positioning our business to take advantage of these opportunities and to mitigate any related risks. Our large portfolio of products and services help our customers in the utility and industry sectors save energy and reduce greenhouse gas emissions.
For example, our advanced industrial information technology for the control and optimization of integrated systems, electrical power grids, buildings and industrial processes saves energy and reduces emissions. The interconnection of power systems with high-voltage direct current technology makes large savings through a more even distribution of loads and a more efficient use of primary energy resources, thereby reducing CO2 emissions. It also enables large-scale integration of renewable energy into the power grids.
While motor-driven applications consume two-thirds of electricity in industry and one-quarter of all the electricity used in the world, drives control less than 10 percent of the motors. ABB’s high-efficiency motors and variable-speed drives for motors contribute to large emission reductions. The worldwide installed base of ABB drives saves electricity equivalent to the annual consumption of more than 54 million European Union households. Optimizing motor-drive systems worldwide could save power equivalent to the annual output of 250 nuclear reactors.
Reducing emissions through a novel, stable supply of power
Using ABB technology, Statoil’s Gjøa platform has become the first floating platform in the North Sea to be supplied with power from shore. When electrical power was connected in July 2010, the platform started to use the world’s longest alternating current cable from land to a floating installation.
The nearly 100-kilometer long cable makes it possible to supply the platform off the coast of Sogn and Fjordane County with renewable energy from the Norwegian electricity grid, and means the platform will cut its carbon dioxide emissions by 210,000 tons per year at full production. A traditional solution with power generated by gas turbines on board would have generated emissions equivalent to 100,000 cars every year.
The technology used for power supply to platforms from land has been developed in close partnership between Statoil and ABB. In addition to the power cable, ABB also supplied the high-voltage equipment for the platform, developing compact electrical solutions for transformers and engine drives in order to save space on board.
Working with partners to build capacity
In practice, however, it can be challenging to capture the benefits of new and existing technologies. Governments, businesses and individuals all play a role, but there’s no easy way to coordinate their actions. Barriers to investing in energy efficiency can include lack of knowledge, unwillingness to change behaviors and practices, and a reluctance to absorb the upfront cost of retrofitting equipment or installing new technology before older technology has reached the end of its productive life cycle.
ABB in China works with a range of partners to overcome these barriers through energy efficiency training. ABB entered into a strategic partnership with Guangdong Province as early as 2006, and has so far delivered energy efficiency training in six Guangdong cities to more than 1,000 enterprises. At the end of 2009, ABB signed a three-year strategic framework agreement with the Ministry of Industry and Information Technology addressing energy efficiency. The two parties work closely together to organize energy efficiency seminars, technology training and consultancies to help enterprises achieve systematic energy conservation and emissions reductions.
In 2010, ABB partnered with the Beijing Energy Conservation and Environmental Protection Center and the global conservation organization WWF to launch a high-level training program on energy efficiency management. The course, “Low Carbon Management Skills and Technology Applications for Enterprises,” is offered to enterprises nationwide and is recognized as part of the Continuing Professional Education program by the Ministry of Human Resources and Social Security.
ABB executives also take part in global initiatives on energy efficiency and climate change. For example, we are a co-chair of the World Business Council for Sustainable Development’s electricity utilities working group, and participate in the energy and climate focus area.
Energy efficiency begins at home
At ABB, we aim to steadily increase the efficiency of our own operations, including through the use of our own products. We have set ourselves the target of reducing the energy we use as a company by 2.5 percent per employee per year for 2010 and 2011. To implement the objective, our 23 most energy-intensive production sites are required to conduct energy audits and all sites are required to develop an energy saving program.
As approximately 50 percent of energy is consumed in our buildings, we have set a supporting objective to improve energy efficiency in buildings by 2.5 percent. During 2010, energy savings in buildings programs were developed in our top 20 countries, representing more than 80 percent of ABB real estate. Underpinning this effort, our Green Building Policy was formalized as a mandatory Group Directive and a cross-functional work program, involving Real Estate, Operational Excellence and Sustainability Affairs, was established to develop a common, practical approach to energy efficiency in production processes and in buildings.
As our 2010 results show, there are still improvements to be made. Electricity consumption remained steady, but primary energy consumption increased, driven in part by the need for diesel-fueled back-up power generation in India. With no significant change in global employee numbers, our energy consumption per employee therefore increased slightly from 2009.
We have made good progress in developing key performance indicators to monitor the environmental impact of transport of goods. Pilot projects are under way in Italy, Saudi Arabia and the U.S. to help us understand how these indicators can be applied practically for both domestic and international transport. Draft guidelines have been developed and are due to be tested in 2011. Carbon dioxide emissions from cross-border transportation have been collected and are being reviewed.
For business air travel, we have established the means for data collection and the methodology for emissions calculation, based on the U.K. Department for Environment, Food and Rural Affairs and Department of Energy and Climate Change methodology. Our first data collection, covering 2010, is presented in the greenhouse gas emissions table below.
Concrete action to reduce our emissions
ABB in Italy is pursuing energy efficiency in buildings both at design stage and during refurbishments. The new building hosting ABB’s business in Genoa was designed with both passive and active energy saving in mind. Walls and surfaces are insulated to minimize heat dispersion, while a range of technologies recover heat, manage lighting, harvest solar energy, and control ventilation to ensure energy conservation. Similar strategies applied to ABB’s existing Santa Palomba site near Rome will avoid 147 tons of CO2 emissions per year, with a payback time of approximately one and a half years.
The Real Estate organization in ABB Germany was given an award by the Deutsche Energie-Agentur – the German Energy Agency – for its sustainable implementation of ecological real estate management. The main office in Mannheim, the Wabenbau, is one of the projects where ABB has achieved energy savings of 44 percent and a CO2 emission reduction of 550 tons by restructuring the building. Other ABB sites in Hamburg, Heidelberg, Ladenburg, Lüdenscheid, Mannheim and Ratingen have also been recognized for their achievement of energy savings of 24 percent, CO2 reduction of 1,956 tons and a cost reduction of almost $800,000 annually.
Energy and climate performance: Other GRI indicators
Download XLS |
EN3 Direct energy use by ABB (Gigawatt-hours – GWh) | |||
Primary fuel |
2010 |
2009 |
2008 |
Oil (11.63 MWh/ton) |
114 |
87 |
104 |
Coal (7.56 MWh/ton) |
0 |
0 |
0 |
Gas |
427 |
415 |
416 |
Total direct energy |
542 |
502 |
520 |
Download XLS |
EN4 Indirect energy use: Consumption and losses at utilities | |||||||
Energy source |
2010 |
2009 |
2008 | ||||
| |||||||
District heat consumption |
223 |
259* |
250* | ||||
District heat: Losses at utilities |
33 |
39 |
37 | ||||
Electricity consumption |
1,335** |
1,321* |
1,323* | ||||
Electricity: Losses at utilities |
1,844 |
1,824 |
1,627 | ||||
Total indirect energy |
3,436 |
3,442 |
3,237 |

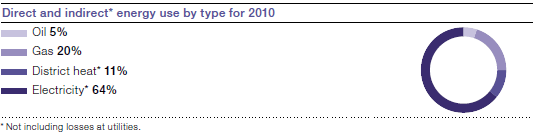
Direct energy use increased by about eight percent during 2010, driven in part by the need for supplementary on-site power generation in India. Electricity consumption remained steady. For 2010, we did not assume additional district heating consumption for the 13 percent of employees not covered by the reported data, as most are located in regions not using district heating, contributing to an apparent decline in district heat consumption.
The pattern of energy consumption was relatively unchanged during 2010, but energy consumption per employee increased slightly. We expect to see further improvements in energy efficiency as production volumes rebound and energy savings programs gain traction.
Download XLS |
EN16, EN17 Greenhouse gas emissions (kilotons CO2 equivalents) | |||||||
|
2010 |
2009 |
2008 | ||||
| |||||||
Scope 1 |
|
|
| ||||
CO2 from use of energy |
117 |
107 |
112 | ||||
SF6 |
247 |
263 |
406 | ||||
CO2 from transport by own fleet |
350* |
350* |
350* | ||||
Scope 2 |
|
|
| ||||
District heat consumption |
49 |
57 |
55 | ||||
District heat: Losses at utilities |
8 |
9 |
8 | ||||
Electricity consumption |
293 |
290 |
287 | ||||
Electricity: Losses at utilities |
405 |
400 |
397 | ||||
Scope 3 |
|
|
| ||||
Air travel** |
645 |
N/A |
N/A |
Emissions of SF6 continued to decline as we pursued emission reduction programs at different sites. However, challenges remain to ensure appropriate handling procedures at both ABB and customer sites.
We are working to improve our data collection around transport emissions, from our own fleet, from transport of our goods by external suppliers and from business air travel. In 2010, we made the first calculation of greenhouse gas emissions from business air travel and we are now reviewing the first data on international transport of goods.