Learning and building together
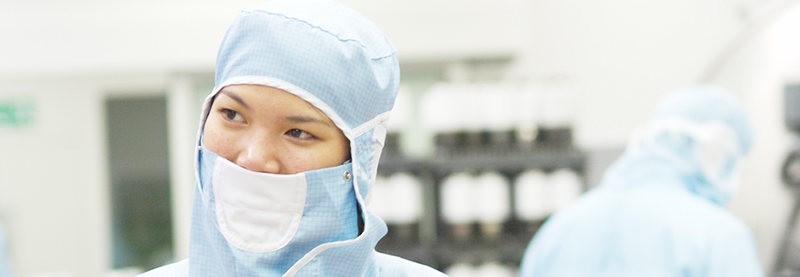
ABB is committed to achieving excellence in Occupational Health and Safety (OHS) and works to achieve this objective through both strategic, Group-led programs and business-specific initiatives.
To support these initiatives, we continue to invest in the competence and development of our people through widespread training and the International Diploma program, and through the provision of additional, specific resources in areas of growth and known high risk activities.
Nonetheless, following an extended fatality free period, sadly we recorded four fatal incidents during 2012; three at the workplace and one during road travel. The fatalities involved two ABB employees and two contractors and occurred in Saudi Arabia, Sweden, Brazil and Congo-Brazzaville.
The number of serious injuries to ABB employees and contractors also increased from 38 in 2011 to 42 in 2012. Serious injuries occurred in all divisions and all regions, with the most common risks identified as falls from height, electrical contact and being struck by objects. All incidents are investigated to identify root causes and lessons learned are communicated throughout the company.
The loss of colleagues and contractors and the increase in serious injuries are of grave concern for us and provide additional impetus for our continued strong focus on OHS improvement programs.
During 2012, we continued to embed OHS in business practices, developing a framework to align goals, standards and processes across our global markets and operational divisions. Business-led OHS programs continued to focus on the particular needs and activities of the different business units (BU) and a new program was initiated in the Motors and Generators BU of the Discrete Automation and Motion Division.
This BU has grown significantly following the acquisition of Baldor Electric Company in 2011 and the OHS improvement program was initiated by the BU to build awareness, knowledge and consistent practices across its operations. The program focused on BU-specific risks, such as lifting, electrical testing, and mechanical handling. It consisted of intensive training in theory and practice and sessions were held in factories in Finland, India, Italy and China, each resulting in improvement action plans.
To support ABB’s strategy to grow our service business, we appointed a Group Service OHS Advisor in 2012. The Advisor is responsible for developing the OHS strategy for ABB Service in line with its growth ambitions and the risk profile of the business, and to coordinate activities throughout regional, country and BU service organizations.
In the service business, collaboration with our customers and other partners is critically important for mutual success. Such a collaboration with ABB Full Service customer Vale at its Voisey’s Bay nickel mine in northern Canada has achieved a major safety milestone – three years with no lost-time incidents. Vale Concentrator Department, ABB and Iskueteu, a local operations support company, worked together to implement best practices for workforce safety, production efficiency and maintenance excellence. Together, we have instilled a strong safety culture into the workforce.
In recognition of the value our service customers place on strong OHS performance, ABB also launched an internal Global Service Award for Safety. The award is intended to recognize service activities resulting in more effective injury or illness prevention and to promote leadership in this area. The 2012 award acknowledged the creation of a guide that provides safety instructions for different machines found in the workplace, with easily-understood material for both new and experienced employees.
In 2012, ABB also expanded the scope of our Group-led programs, rolling out our Group occupational health strategy with a series of awareness training sessions around the world. More than 120 people in seven regions were trained to address occupational health risks, such as exposure to hazardous substances, physical agents, noise and vibration.
The sessions involved a combination of theory and practice to assist effective management and monitoring of risks at country and site level. Participants prepared their own occupational hygiene management programs and during 2013 we will conduct reviews to assess implementation of these programs.
The strategy is led by a global Occupational Health Team consisting of occupational health physicians and OHS professionals who also provide support and guidance for local programs. In 2012, we appointed a Group Occupational Health Physician to spearhead this program.
At country level, OHS improvement programs are organized according to formal country OHS strategic plans that are tailored according to local conditions and business needs. Progress towards performance targets and implementation of training and development programs is monitored quarterly at Group level.
Increasingly, local ABB OHS programs are being recognized by external stakeholders. For example, in the US in 2012, ABB Inc. was named one of America’s safest companies by EHS Today, a leading publication and resource for safety, health and industrial hygiene professionals. Newly-integrated Baldor plants also received the Award of Excellence in Safety from the state of Georgia, the North Carolina Department of Labor Safety Award, the South Carolina Chamber of Commerce Commendation for Excellence for Safety and the Arkansas Department of Labor Safety Award.
For 2013, we will continue to develop our model for OHS excellence, building awareness and understanding at every level of the company. We will build our OHS behavior standard as an integral part of the Group processes that define the values of the company and work to ensure business-specific needs are recognized and met.
Occupational health and safety performance: GRI indicators
LA6 Percentage of total workforce represented in health and safety committees
Health and safety consultation is an integral part of ABB’s commitment to introduce into all businesses occupational health and safety management systems based on OHSAS 18001 and the International Labour Organization (ILO) guidelines. The form of health and safety consultation with employees varies according to local requirements and cultures. It includes health and safety committees and employee forums.
At Group level, ABB has a standing Occupational Health and Safety (OHS) committee chaired by an Executive Committee member whose mandate covers all employees.
LA7 Injuries, lost days, diseases and fatalities
Download XLS (18 kB) |
|
2012 |
* |
2011 |
2010 | ||
---|---|---|---|---|---|---|
| ||||||
Employee work-related fatalities |
1 |
|
0 |
1 | ||
Incident rate |
0.01 |
|
0 |
0.01 | ||
Employee work-related serious injuries |
22 |
|
22 |
15 | ||
Incident rate |
0.16 |
|
0.18 |
0.13 | ||
Employee business travel fatalities |
1 |
|
0 |
2 | ||
Incident rate |
0.01 |
|
0 |
0.02 | ||
Employee business travel serious injuries |
0 |
|
3 |
5 | ||
Incident rate |
0 |
|
0.02 |
0.04 | ||
Contractor work-related fatalities |
2 |
|
0 |
2 | ||
Contractor work-related serious injuries |
20 |
|
16 |
16 | ||
Contractor business travel fatalities |
0 |
|
0 |
0 | ||
Members of the public fatalities |
0 |
|
0 |
0 | ||
Employee lost days due to industrial incidents |
10,345 |
|
9,478 |
8,362 | ||
Employee occupational health diseases |
10 |
|
7 |
13 | ||
Employee total recordable incident rate |
13.04 |
|
13.17 |
13.48 |
In these statistics, figures for fatalities also include deaths occurring within one year as a result of injuries sustained. Incident rates are according to the ILO rate per 1,000 employees. The total recordable incident rate includes the following incidents: serious injuries, lost time incidents, medical treatment injuries, occupational health diseases and restricted work day cases. “Lost days” are calendar days, and are counted from the day after the incident. Business travel incidents include injuries related to road travel. Incidents during air travel, on business trips, are excluded.
LA8 Programs in place regarding serious diseases
More than 30 ABB country organizations report programs in place to address serious diseases. The majority of programs include stress management, health screening for conditions such as diabetes and hypertension, and counseling schemes to assist employees to maintain healthy lifestyles and a suitable work-life balance. Other initiatives include vaccination programs and cancer screening.
In four countries (Brazil, Mexico, Philippines and South Africa) ABB has specific programs in place to address HIV/AIDS and ABB in Italy worked with “Save the children” and the Association of Volunteers in International Service (AVSI) Foundation to collect funds for a program to fight HIV/AIDS in developing countries.
Additionally, all ABB travelers receive destination-specific security and health advice prior to travel. The health advice includes medical preparedness, medical screening where needed and advice on particular health risks at their destination.
LA9 Health and safety topics covered in formal agreements with trade unions
This information is not recorded by the Group, but local legislation requires formal agreements in some countries such as Germany and South Africa. Group health and safety performance is reported annually by the head of Group Function Sustainability Affairs at a meeting with the European Works Council.