Pursuing efficiency through the life cycle
(includes GRI indicators EN2, EN9–15, EN21, EN24–27)
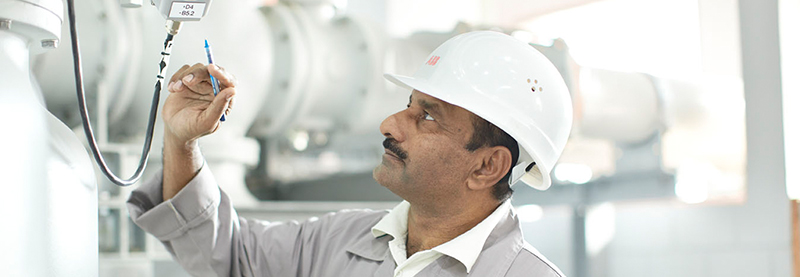
As a business, ABB focuses on developing world-class products, systems and services to lower our customers’ energy use, reduce their emissions and improve resource efficiency on a long-term basis. We take a life cycle approach to assess the impacts throughout the phases of a product’s life.
Environmental impact can occur in all phases of a product’s life cycle, from raw material supply to manufacture, transportation, customer use and final recycling and disposal. ABB has been working for many years to manage our impacts, both those caused by our products and projects and within our own facilities.
To ensure continual improvement in our own operations, we require all manufacturing and service facilities to implement environmental management systems according to the ISO 14001 standard. Our newly-acquired Baldor sites pursued a robust ISO 14001 implementation program during 2012, and is due to complete it in 2013.
For non-manufacturing sites, we have implemented an adapted environmental management system to ensure management of environmental aspects and continual improvement of performance. Of the more than 390 ABB facilities and offices in 64 countries covered by our environmental management program, approximately 95 percent currently comply with the ISO 14001 standard.
ABB life cycle assessment experts have worked with our sales teams to develop customized tools and environmental reporting approaches tailored to specific customer needs. One tool uses Environmental Product Declarations and other data sources to track specified environmental impacts for a specified project, while another tool helps customers to visualize both the environmental and financial costs and benefits of different ABB solutions.
Life cycle assessment (LCA) is required as part of a product’s research and development phase and is also used in the concept development phase for next generation products. ABB designers follow sustainability guidelines in each phase of the product and technology development process. These include standardized LCA procedure and a handbook to guide consideration of environmental, and health and safety aspects during design, such as how to reduce the use of hazardous substances, avoid other environmental and health risks, minimize consumption of resources and design for recycling and easy end-of-life treatment.
ABB develops Environmental Product Declarations to communicate the environmental performance of our core products over their life cycle. Declarations are based on LCA studies, created according to the international standard ISO/TR 14025. More than 80 declarations for major product lines are published on our website (www.abb.com).
Water
Even though ABB’s manufacturing process does not consume significant amounts of water, we have undertaken a program to better understand the patterns and impacts of ABB’s water withdrawal, use and discharge. To start the program, we developed an in-house tool for mapping and analysis of water flows at our facilities. The tool, based on the World Business Council for Sustainable Development Global Water Tool, was piloted at a number of facilities in early 2012 and then rolled out to 42 manufacturing facilities in water-scarce and extremely water-scarce watersheds.1
1 Food and Agriculture Organization of the United Nations (FAO) (2003). Review of world water resources by country. Water Reports 23. Rome. According to this methodology, a watershed is considered water-stressed if the total actual renewable water resources (TARWR) are below 1,700 m3 per person and year, water-scarce if below 1,000 and extremely water-scarce if below 500.
In this extended pilot phase, we targeted manufacturing plants to gain a broader view of both industrial and domestic water use patterns. The facilities were required to gather a team to systematically review water flows, analyze water-related opportunities and threats to their operations and develop a water action plan to minimize risks and to leverage opportunities.
Action plans were received from 34 facilities. A number of small sites that do not use process water were exempted from developing formal action plans, but did work through the process and submitted completed water maps for their facilities.
Action plans identified both technical solutions, such as waste water treatment plants to enable water reuse and behavioral aspects to improve water efficiency. The most frequently described actions were awareness-raising and training programs, the installation of flow meters to detect leakages and measure usage, the installation of aerators for taps, and the introduction of waterless urinals. How the plans progress will be monitored at Group level through 2013.
When looking at ABB’s global operations, more than three quarters of our water withdrawals are used for cooling processes and returned to source at similar or higher quality (44 percent) or are used for domestic purposes such as sanitation, cooking or garden maintenance (32 percent). None of our water extractions caused significant changes to water sources in 2012.
Of those ABB sites that use water for process purposes, approximately 30 percent use closed-loop systems, mainly for cooling, surface treatment processes and the production of electrical insulation paper. Excluding cooling water returned to the source of extraction, the use of closed-loop processes and reuse of waste water in other ways saved approximately 3,700 kilotons of water in 2012. Without these recycling and reuse processes, ABB’s water withdrawals would have been almost 40 percent higher.
Our facilities are increasingly installing waste water treatment plants to allow the reuse of domestic and process water in other applications. Most notably in Australia, India and South Africa, rain water tanks have been installed to replace water supplied by utilities for sanitary and gardening uses, and in Italy, a new air conditioning system capable of reusing process cooling water has been introduced.
Not including cooling water, about 52 percent of water was discharged to public sewers, with almost 30 percent of that volume first processed at our own treatment plants. Another 38 percent was discharged to surface or ground water, with 45 percent of that volume pre-treated, and the remainder was handled by hazardous waste water treatment companies.
Thanks to a wide portfolio of products and solutions, we provide our customers with enhanced performance, efficiency and reliability in water management. During 2012, different elements of ABB’s water portfolio received industry awards for water efficiency and for innovation in “smart water networks.”
At the 2012 H2O awards, celebrating achievements of the Middle East and North Africa water industry, ABB’s AquaMaster3™ flow meter device won the “Most Water Efficient product category.” The award recognized the device’s effectiveness in addressing water leaks, boosting water efficiency and lowering utilities’ environmental impact. The technology heralds a new era in water leakage management and was designed in response to the industry’s demands for enhanced metering capability – enabling a more efficient and cost-effective operation and compliance with increasing legislative requirements.
ABB was also recognized through a global leadership award by Frost & Sullivan for our innovation in the sector of “smart water networks/grids.” ABB’s commitment to the water sector with technology solutions was commended in the areas of automation and control, metering and utility hardware, design and engineering, and information communication technologies.
Waste and recycling
The main waste streams at ABB organizations are metal, wood, paper, oil and plastic. With the ongoing integration of the newly acquired operations of Baldor and Thomas & Betts, the characteristics of our waste streams and the opportunities for waste minimization and recycling are changing. We are working to understand these differences and learn from established good practices, but we continue to aim to reduce the amount of waste sent to landfill and to increase our use of materials that are recycled or made available for reuse.
ABB products contain mostly steel, copper, aluminum, oil and plastics. Approximately 90 percent of the material is reclaimable after the end of a product’s useful life. ABB enhances the ability to recycle by designing products that can be dismantled more easily, and by providing users with recycling instructions.
In 2012, 82 percent of total waste was sent for recycling. In-house recycling, mainly of thermoplastics and packaging material, reduced the amount of waste by approximately 23 kilotons, a significant increase from 3.2 kilotons in 2011. The lead used as counterweights for robots and the cadmium used in industrial batteries are also recycled materials.
ABB generated approximately 12 kilotons of hazardous waste in 2012, but around 34 percent of that amount was sent for recycling rather than disposal, including batteries, electronics and used oil. The waste sent for disposal was mostly used for heat recovery at specialized plants. ABB follows legal regulations to transport and dispose of hazardous waste only through officially authorized disposal agents.
Many different plant level waste reduction and recycling programs were undertaken during 2012, depending on the characteristics of the production process and the local waste infrastructure. Facilities in India reduced scrap metal quantities through specialized material yield projects, while in South Africa the focus was on reducing copper wire offcuts. Many plants investigated how to recycle used oil instead of sending it for incineration, including developing methods to separate the used oil from water-based mixtures. In another plant, scrap wooden pallets were ground and sent to a paper mill for reuse and as fuel.
Hazardous substances
ABB continues to phase out the use of hazardous substances in our products and processes, where technically and economically feasible. We have developed lists of prohibited and restricted substances to guide this process and update them regularly, in line with international regulations.
Our recent acquisitions, Baldor Electric Company and Thomas & Betts, use different processes and products at their facilities, so we are looking at the substances they use and, where necessary, we will update their monitoring and reporting processes related to hazardous substances. As ABB’s suppliers are also required to apply the list of prohibited and restricted substances to their own processes and supply chain, we will also work towards including these areas in the integration process.
Possibly the most extensive ABB program to reduce hazardous substances is the ongoing Volatile Organic Compounds (VOC) reduction program in the Transformers Business Unit of our Power Products division, involving 62 factories in 27 countries. The challenge is to reduce VOCs by replacing the solvent-based paint used on transformer tanks with water-based and high-solid paints.
The roll-out is a complex process that must be planned around commercial aspects such as frame contract conditions and coordination of customers with differing requirements, as well as robust quality assurance and training programs. Plants in Finland, Poland, Saudi Arabia, Sweden, Turkey, the United States and elsewhere have already converted to low VOC systems and work is ongoing in other countries.
Conventional paints emit VOC and the main sources in ABB operations are the paint shops for transformers and motor manufacturing. Previously, the transformers business has been the most significant source of VOC emissions for ABB. However, the acquisition of the Baldor Electric Company, specializing in motor manufacturing, has resulted in a significant increase in our Group VOC emissions.
Plant-specific hazardous substance phase-out programs are showing results, with some materials such as organic lead in polymers almost completely eliminated. During 2012, the use of lead solder was eliminated in some U.S. facilities and some Indian facilities switched to non-chlorinated solvents.
Biodiversity and conservation
ABB’s manufacturing and workshop facilities are not located in, or adjacent to, protected areas or areas of high biodiversity value, as defined in internationally recognized listings or national legislation or internationally recognized listings such as the International Union for Conservation of Nature Protected Areas Categories 1–4, world heritage sites or biosphere reserves. Nonetheless, ABB works to rehabilitate our own sites and some of our operations are working with partners to contribute to local biodiversity and conservation efforts.
For example, in China the anti-desertification efforts of ABB, Inner Mongolia Electric Power, and Ordos Electric Power Bureau are succeeding in preventing soil erosion and in protecting power transmission lines.
Desertification and soil erosion are major issues in China. Every year sandstorms engulf the region even as far away as Beijing, which not only threatens the environment and the livelihoods of people, but also the infrastructure that feeds the region with electric power, the loss of which has huge economic implications.
ABB has worked with our partners to plant a corridor of fast-growing plants that thrive in desert environments in Inner Mongolia to bind the sand and prevent it from forming dunes that damage the pylons and overhead power lines.
Prior to the creation of the corridors, maintenance teams from the Inner Mongolia Power Company had to constantly clear the ever-drifting sand to prevent power interruptions and maintain the compulsory 11-meter safety distance between the lines and earth. Now that the dunes are more stable, a further agreement to expand the initiative has been signed by the three parties.
Additionally, ABB supports local forest preservation and tree planting schemes in China, Italy and the U.S. ABB employees in the Philippines and Qatar help to preserve local beach and marine environments, while ABB in Malaysia, Peru and Taiwan partner with local parks to support the rehabilitation and maintenance of wetlands.
Environmental performance: Other GRI indicators
EN1 Use of hazardous substances (tons)
Download XLS (18 kB) |
|
2012 |
a |
2011 |
b |
2010 | ||||
---|---|---|---|---|---|---|---|---|---|
| |||||||||
Phthalates – softener for PVC |
28 |
|
47 |
|
31 | ||||
PBB and PBDE – flame retardants in plastics |
~0 |
|
~0 |
|
~0 | ||||
Lead in submarine cables |
5,633 |
|
5,725 |
|
3,632 | ||||
Organic lead in polymers |
0.9 |
|
1.3 |
|
52 | ||||
Lead in other products, e. g. backup batteries and counterweights in robots |
363 |
|
227 |
|
265 | ||||
Cadmium in industrial batteries delivered to customers |
5.6 |
|
1.6 |
|
1.7 | ||||
Cadmium in rechargeable batteries |
6.3 |
|
10 |
|
5.9 | ||||
Cadmium in lead alloy and other uses |
4.5 |
|
4.3 |
|
2.9 | ||||
Mercury in products delivered to customers |
0.011 |
|
0.030 |
|
0.038 | ||||
SF6 insulation gas (inflow to ABB) |
1,139 |
|
1,052 |
|
968 | ||||
SF6 insulation gas (outflow from ABB) |
1,118 |
|
1,040 |
|
959 |
Water
EN8 Water consumption
EN10 Water recycled and reused
Water withdrawals (kilotons)
Download XLS (18 kB) |
|
2012 |
a |
2011 |
b |
2010 |
| ||||||||
---|---|---|---|---|---|---|---|---|---|---|---|---|---|---|
| ||||||||||||||
Purchased from water companies |
3,900 |
c |
3,400 |
c |
3,300 |
c | ||||||||
Groundwater extracted by ABBd |
3,000 |
|
3,200 |
|
2,700 |
| ||||||||
Surface water extracted by ABBd |
2,800 |
|
2,600 |
|
2,900 |
| ||||||||
Total water withdrawal |
9,700 |
|
9,200 |
|
8,900 |
| ||||||||
Water saved through recycling and reuse |
3,700 |
|
3,900 |
|
3,000 |
|
Air emissions
EN19 Emissions of Volatile Organic Compounds (tons)
Download XLS (16 kB) |
|
2012 |
a |
2011 |
b |
2010 | ||||
---|---|---|---|---|---|---|---|---|---|
| |||||||||
Volatile Organic Compounds (VOC) |
1,355 |
|
810 |
|
786 | ||||
Chlorinated Volatile Organic Compounds (VOC-Cl) |
12 |
|
13 |
|
11 |
The major constituents of VOCs and VOC-Cls are xylene, thinner and perchloroethylene. The significant increase in 2012 was due to the inclusion of Baldor facilities.
EN20 Emissions of NOX and SOX (tons SO2 and NO2)
Download XLS (17 kB) |
|
2012 |
a |
2011 |
b |
2010 | ||||
---|---|---|---|---|---|---|---|---|---|
| |||||||||
SOX from burning coal |
0 |
|
0 |
|
0 | ||||
SOX from burning oil |
69 |
|
68 |
|
84 | ||||
NOX from burning coal |
0 |
|
0 |
|
0 | ||||
NOX from burning oil |
52 |
|
51 |
|
63 | ||||
NOX from burning gas |
120 |
|
90 |
|
92 |
These figures are for fossil fuels consumed in ABB premises for heating and process purposes. The significant increase in NOX from burning gas in 2012 is due to the inclusion of Baldor facilities, which use higher quantities of gas than the existing ABB facilities.
Waste and recycling
EN22 Waste generated (kilotons)
Download XLS (18 kB) |
|
2012 |
a |
2011 +Baldor |
a |
2011 |
b |
2010 |
| ||||||||
---|---|---|---|---|---|---|---|---|---|---|---|---|---|---|---|---|
| ||||||||||||||||
Scrap metal sent for recycling |
150 |
|
161 |
|
97 |
|
135 |
c | ||||||||
Other waste sent for recycling |
41 |
|
42 |
|
39 |
|
44 |
| ||||||||
General waste sent for disposal |
43 |
d |
47 |
d |
45 |
d |
38 |
d | ||||||||
Hazardous waste |
12 |
d |
11 |
|
9 |
|
9 |
| ||||||||
Total waste |
246 |
d |
262 |
d |
190 |
d |
227 |
c |
Environmental incidents and penalties
EN23 Numbers of significant spills
EN28 Significant fines for non-compliance
Number of incidents
Download XLS (16 kB) |
|
2012 |
a |
2011 |
b |
2010 | ||||
---|---|---|---|---|---|---|---|---|---|
| |||||||||
Oil spills |
6 |
|
5 |
|
4 | ||||
Chemical spills |
0 |
|
0 |
|
0 | ||||
Emissions to air |
5 |
|
4 |
|
0 | ||||
Others |
0 |
|
0 |
|
3 |
The emissions to air involved the accidental release of SF6 gas in four incidents and one release of HCFC-22 from an air conditioning system. The oil spills were contained and adequate decontamination procedures were implemented to prevent any permanent contamination of soil and water. Root causes of the incidents were analyzed and corrective actions, such as improved control systems, upgraded secondary containment and additional training, have been taken to reduce the risk of future spills or emissions. Combined costs of remediation and corrective actions were approximately $150,000.
During 2012, one of our U.S. facilities was fined less than $1,000 for the late submission of an annual air report in 2011.
EN30 Environmental protection expenditure and investments
For 2012, ABB’s expenditure on environmental management throughout our global sustainability affairs network was as follows:
Download XLS (16 kB) |
Expenditure on environmental management |
$ thousands |
---|---|
Group level |
10,750 |
Country level |
5,300 |
Site level |
4,300 |
Total |
20,350 |
ABB limits the accounting of sustainability to the costs of implementing and maintaining environmental management systems to ISO 14001, health and safety management systems to OHSAS 18001, and running the sustainability network, including personnel costs and the cost of developing sustainability tools, education and training.
This does not include costs related to improvement projects. For example, the decision to invest in a new manufacturing process is the result of integrating many decisions in addition to environmental considerations.