Energy efficiency, renewable energy and climateWorking to reduce climate impacts
As part of our Group-wide sustainability objective to progressively increase the efficiency of our own operations, we have set ourselves the target to reduce the energy intensity of our business by 20 percent by 2020 from a 2013 baseline. This includes both direct fuel consumption and the use of electricity and district heating for manufacturing processes and to operate buildings. We also aim to cut greenhouse gas (GHG) emissions by reducing direct fuel consumption, converting to lower carbon sources of energy and improved handling of sulfur hexafluoride gas (SF6).
To implement the objective, all sites were required to establish an energy savings program and to undertake actions to reduce GHG emissions. By the end of 2016, country energy savings plans were in place for 40 countries, covering 99 percent of ABB energy use, and more than 280 energy savings projects were under way at ABB sites.
9%
reduction in energy consumption since 2013
These focused activities have brought results, with absolute reductions in both energy consumption and GHG emissions realized between 2013 and 2016. However, due to lower revenues and capacity utilization, ABB’s energy intensity, measured as MWh per million US dollar sales, was 13 percent higher in 2016 than the 2013 baseline.
Energy efficiency in our operations
A wide variety of energy savings projects were implemented across the company to achieve the reductions observed in 2016. Most commonly, and cost effectively, facilities implemented energy-efficient lighting solutions. Other activities included optimizing heating, ventilation and cooling processes, investments in more efficient equipment, investigating and optimizing compressed air systems, behavioral change programs, and implementing or updating heat recuperation from machines and processes, often using our own technology.
ABB in Switzerland continued its program of lighting system upgrades, with projects completed at facilities in Altstetten, Baden and Untersiggenthal during 2016. Energy-efficient LED lights were installed along with ABB’s KNX control systems with daylight sensors and dimming/motion detectors, resulting in better quality illumination of workspaces and significant energy and cost reductions. The company expects an annual energy saving of 1,600 MWh from these three facilities alone. In total, more than 120 lighting replacement projects were undertaken across ABB in 2016, with expected annual energy savings of more than 8,500 MWh.
Total energy use and energy intensity
| XLS (21kB) PNG (53 kB)
A number of sites reviewed their compressed air systems, including Rogersville in the US, where actions to address the findings of an air leak survey are expected to save up to two percent – over 450 MWh – of the site’s annual energy consumption. The Kecskemet facility in Hungary installed new, more energy-efficient compressors and now also uses the waste heat generated by the equipment to produce hot water, saving 120 MWh.
Other, novel approaches to heating and cooling are also providing promising results. At the Nowa Wies Leborska site in Poland, analysis of heating needs resulted in the replacement of natural gas heating with floor heating film, bringing savings of more than nine percent of the site’s total energy consumption. The Oiartzun site in Spain installed a system to extract and redirect waste heat from one part of the factory to the employees’ locker rooms, enabling deactivation of the original heaters. While in Bulgaria, installation of efficient groundwater pumps and heat exchangers connected to the plant’s cooling system has provided highly energy efficient additional cooling capacity needed to cover the plant’s requirements and to create a better working environment.
Many facilities have also chosen to implement formal energy management systems (EnMS), with 48 of the 99 sites with an EnMS now externally certified to ISO 50001 or EN 16247. ABB in Spain has implemented a unified EnMS for six main manufacturing and service sites, representing more than 95 percent of ABB’s total energy consumption in the country, and achieved certification in early 2015. Each site works towards annual targets based on its unique circumstances and, through these efforts, ABB in Spain reached its 2020 goal to achieve a 20 percent reduction in country-wide energy intensity by the end of 2016.
Driving efficiency in our real estate portfolio
ABB’s corporate real estate management also plays a key role in our energy efficiency performance. The ABB Green Building Policy guides the acquisition, development, refurbishment and management activities related to our worldwide portfolio of about 8.4 million square meters of building space. The policy covers both owned and rented space and sets out detailed criteria, including site selection, building design, and choice of materials to optimize resources. Implementation of the policy is helping ABB to achieve our goals for improved environmental performance, financial savings and greater employee satisfaction.
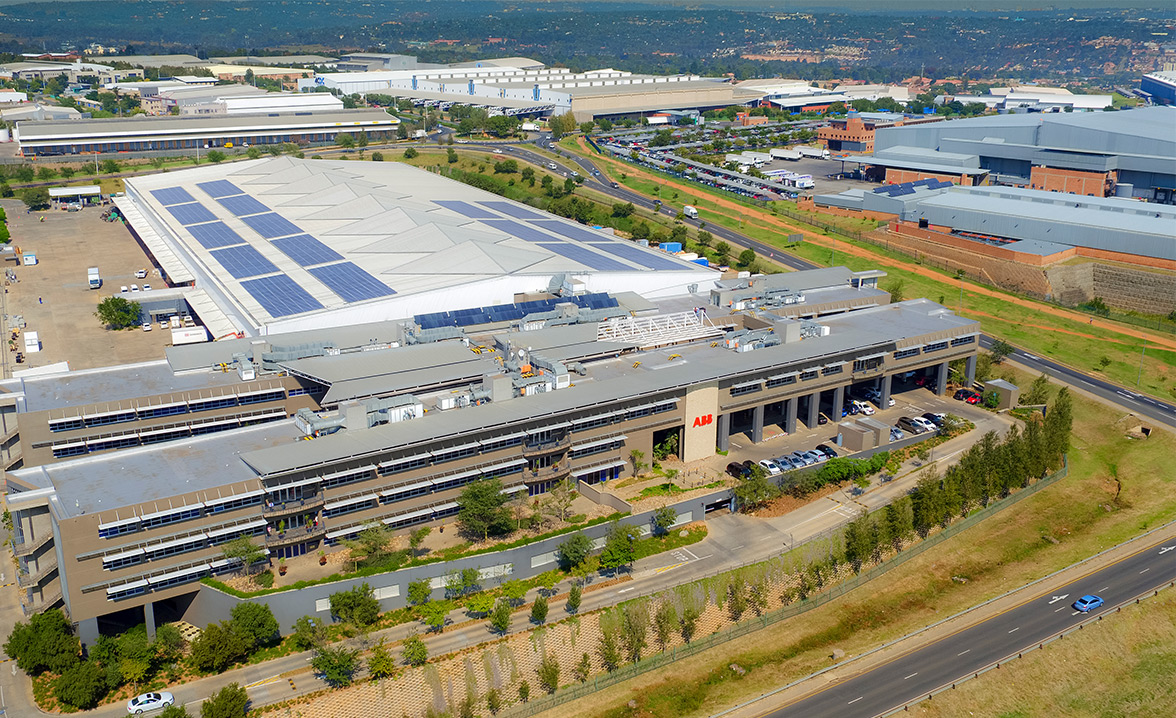
To supplement site by site improvement projects, in 2013 ABB real estate management kicked off a significant project to introduce systematic real estate energy efficiency programs across Europe. Energy monitoring, technical assessments and evaluation of efficiency measures were completed at more than 70 sites across 13 European countries by the end of 2016. Sites in two further countries were expected to complete their projects by early 2017.
More than 600 energy efficiency measures were identified in the course of the projects, along with three key, recurrent themes: lighting, distribution grids and compressed air. To help structure and expedite relevant energy efficiency improvement activities, we created guidelines for our real estate network and compiled useful information around these common issues.
Beyond Europe, the energy efficiency project was expanded to Canada, the US and China in 2016, with activities in India and Brazil scheduled to start in 2017.
Reducing carbon intensity of energy
As part of our goal to cut both direct and indirect GHG emissions, ABB seeks to reduce the carbon intensity of our energy sources. Several ABB countries – Belgium, France, Italy and the Netherlands – now purchase all of their electricity from renewable sources. Thomas & Betts plants in these countries will also join these programs as their current contracts reach expiration. In Sweden, almost 20 percent of electricity purchased was “green” energy, while globally, 130 GWh, or almost 8 percent of ABB’s 2016 electricity was purchased as certified “green” electricity.
11%
reduction in GHG emissions (Scope 1 + 2) since 2013
Increasing numbers of ABB facilities are also installing on-site photovoltaic (PV) power plants to reduce environmental impact and demonstrate ABB’s solar capabilities. PV plants are now installed at 33 sites in 22 countries across Asia-Pacific, Europe and Latin America. While contributing only a small proportion of our global electricity needs, these plants are often a key part of local energy strategies to replace diesel generation with low carbon reliable power.
Extending this concept, ABB installed an integrated solar PV-diesel-battery microgrid at our Longmeadow facility in Johannesburg, South Africa in 2016. The microgrid integrates multiple energy sources and battery-based stabilization technology within a smart control system, supplying reliable power 24/7 while also optimizing the site’s use of solar energy sources. In late 2016, ABB also announced that we will install a fully integrated microgrid at our Vadodara facility in Gujarat, India to help boost renewable energy generation while reducing dependency on fossil fuel.
Total greenhouse gas (GHG) emissions and GHG intensity
| XLS (22kB) PNG (45 kB)
Cutting greenhouse gas emissions
ABB’s total GHG emissions (Scope 1 + 2) decreased by 7 percent in 2016 to 1.38 million tons, with an overall 11 percent reduction since 2013. Around 70 percent of the saving in 2016 was due to an overall reduction in the carbon intensity of electricity supply. That is, CO2 emissions from electricity consumption were 10 percent lower in 2016 than 2015, even though electricity consumption remained essentially unchanged year on year.
The remainder of the savings were due to decreased gas consumption and a reduction in SF6 emissions from production processes and gas handling on site. During 2016, a number of facilities redesigned certain production processes to reduce and, where possible, eliminate SF6 use. For example, one of our US facilities eliminated the use of SF6 in its die casting process, reducing emissions by more than 4,500 t CO2e. Other facilities took measures to improve handling, leak detection and storage procedures for the gas. See the “Approach to reporting” section of this report for details of our GHG calculation methodology.
Transport, logistics and packaging
Implementation of ABB’s global fleet management tool and processes progressed during 2016. Fleet procurement and management processes were harmonized across Europe and will be rolled out in the Americas and Asia in 2017. Baseline, global fleet data were assembled and uploaded to our fleet management tool during the year, with actual fuel and mileage data entry to follow during 2017. The tool will enable tracking of fleet efficiencies and sharing of good practices across our businesses.
Mobility initiatives were also undertaken in a number of locations during 2016. ABB in Canada implemented a pilot GPS service vehicle monitoring program at six of its sites, allowing identification of the closest service vehicle to reduce distance traveled, plus other efficiencies, expected to reduce fuel consumption by 15 percent. In time, this program will be extended to all ABB vehicles in North America. Driver training programs were implemented by a number of businesses to improve both safety and fuel efficiency, while ABB Benelux received a Lean & Green Personal Mobility Award for their actions to reduce CO2 emissions from transport. Initiatives included greening the company car fleet, driver training and providing a pool of electric vehicles for use by employees.
ABB is also significantly expanding its program to optimize logistics operations, with the introduction of ten Transportation Management Centers (TMCs) to serve all ABB businesses globally.
A successful TMC pilot in China consolidated the transport, trade and logistics processes of 36 factories into one TMC location in Shanghai. The new set up, covering all ABB businesses in China, led to significant improvements in all key performance indicators, achieving over 98 percent on-time delivery (OTD) and 99.9 percent damage-free shipments, along with significant reductions in cost and transport-related CO2 emissions.
As a further step, we have invested in a cutting-edge transportation management system (TMS), which suggests route- and load-optimized shipment plans. It will be deployed across all TMCs as they are rolled out. With this tool, ABB’s supply chain management is digitalizing the planning and execution of the physical movement of goods, enabling real-time monitoring and reductions in cost, lead time and inventories.
In 2016, the TMC in Bangalore, India was the second global center to go live, covering domestic freight for 39 local plants. During 2017, the remaining eight Transport Management Centers will be rolled out, enabling more efficient management of millions of shipments worldwide. TMCs will play an active part in making ABB a stronger, more agile and productive company, helping us to increase customer satisfaction while reducing both costs and environmental impacts.