Safe, healthy and secure operations Focusing on accountability and engagement
We consider the ABB value pair of safety and integrity as the bedrock of our organization, which means that the health and safety of our employees, contractors, customers and others affected by our activities are a top priority for ABB.
Our objective is that by 2020 all ABB operations will have an excellent health, safety and security culture embedded in their day-to-day business, targeting zero incidents.
Many programs and best practices already are in place to help achieve this goal and significant progress has been made, for example achieving a sustained decline in overall employee incident rates. However, we faced a challenging year in 2016 when we recorded a number of fatal contractor and road travel incidents, prompting a close review of how we support safety throughout our global operations.
Top leadership reinforces accountability
The results of this analysis prompted the ABB Executive Committee to launch a new framework to reinforce clear accountability and responsibility for health, safety and environment (HSE) in our operations. Within this HSE accountability framework, we established ‘lead organizations’ and ‘lead managers (HSE)’ for every ABB workplace across our organization.
Lead managers (HSE) now chair a local governance process to ensure that there is clear agreement, communication and understanding on responsibilities for managing HSE risks at every ABB workplace and for every shared or common area associated with that location. Consistent with ABB’s Next Level strategy, the HSE accountability framework reinforces the clear link between our core values, our behavior and delivering business value.
To further underline this link, all ABB employees are required to include a health and safety behavioral goal in their annual objectives. Additionally, management engagement with safety is incentivized by inclusion of the safety indicator “hazard reporting rate” in the internal ABB performance dashboard, which is factored into all managers’ variable compensation.
Other, key CEO-led programs continued to reinforce the Group safety message. The second annual CEO Safety Awards were presented at the Group Leadership Forum in 2016. The awards are open to all ABB employees around the world and acknowledge significant individual and team achievements that promote a strong safety culture. From more than 130 nominations, winners and runners-up were selected in each of four categories – Safety Leader, Project Safety Performance, Team Safety Improvement and Service Safety Award.
ABB Safety Week, launched by senior management in 2014 to mobilize ABB teams and contractors around safety, expanded further in 2016. Around 160,000 employees and contractors took part in more than 4,000 activities promoting safe and healthier habits, both at work and at home. Sessions focused on three drivers of ABB safety culture: Safety-related communication, key safety disciplines and the safety observation tour (SOT) process. To expand on the week’s communication theme, ABB employees also actively engaged their colleagues in more than 140,000 targeted conversations about health and safety topics important in their local area.
160,000 employees
and contractors took part in Safety Week 2016
Programs and tools supporting our strategy
During 2016, we also continued to deliver global improvement programs associated with our key risks and the work areas prioritized the previous year: Safety masterclasses for line management, streamlined HSE management system, and a comprehensive HSE audit program.
The safety masterclasses are leadership and HSE competence workshops for line managers, designed to extend their HSE knowledge and leadership skills and to help them apply these leadership practices in their daily work. Designed and piloted during 2015, the program was rolled out to more than 1,600 plant, local business unit (BU) and product group managers in 2016, with a further 200 completing the classes in the first half of 2017. While this first wave of the program was delivered in cooperation with an external training partner, we will now train our own personnel to deliver the classes, to enable a much broader reach across the organization.
To further promote business alignment on our common HSE goals, to drive efficiency and to provide a common base for our audit program, we are developing a Group HSE/Sustainability management system consistent with international standards. We laid the foundations for the system during 2016, and in 2017 will continue development and conduct pilots with selected BUs.
In 2016 we also launched a program to improve and align the way we provide HSE audit and assurance across the group. The program will focus on key, high impact and high frequency issues across all operations and will provide a comprehensive assessment of the implementation maturity of ABB’s HSE/Sustainability management system. A Group HSE audit and assurance manager was appointed in 2016, who is developing Group standard audit protocols and recruiting the audit team during 2017, with full program deployment planned for 2018.
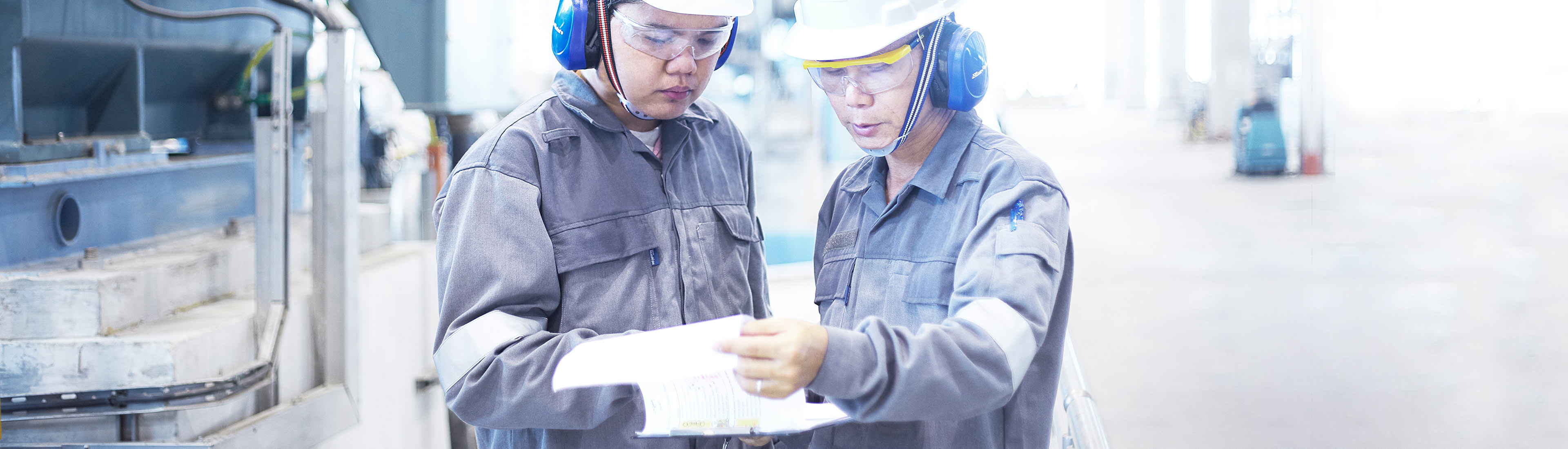
Health and wellbeing: Building resilience
As part of ABB’s focus on our people, during 2016 we expanded our employee health program beyond the existing risk management aspects of occupational hygiene, ergonomics, travel health and pandemic preparedness to bring a global focus on wellbeing and resilience.
Initially, we collected good practices across the company to develop Group policies and practices on health. We then established and started to roll out a new ABB health strategy, with the goal to integrate good health practices into the daily life of all our employees, both at work and at home.
All ABB country HSE/sustainability organizations were required to appoint a country wellbeing coordinator and to develop a country wellbeing plan as part of their overall 2017 HSE program. With the introduction of non-smoking policies as a cornerstone, HSE organizations also were required to develop a range of activities to promote topics such as healthy nutrition, fitness, medical checks, health awareness and addiction prevention. In addition, programs to promote physical, psychological and social resilience are in development during 2017, with the initial focus on stress management.
We expect this added focus to bring benefits both for our employees and for ABB, as the wellbeing of the people working for an organization is a determining factor in its long-term effectiveness and productivity.
Our health and safety performance
We saw significant improvement in many of our key safety metrics in 2016, but tragically we recorded five fatal workplace incidents involving contractors at work sites in China, Egypt, Guinea and India, and one road traffic accident in Peru resulting in the death of two contractors and an ABB employee.
In response, we are reinforcing our efforts at many different levels to ensure safe ways of working with contractors. Supplier qualification and classification processes have been enhanced, contractor management and project safety management are part of our code of practice for safe working and our safety leadership training, and project safety audits and the new governance processes provide assurance that the rules are being followed.
Additionally, we launched a global road safety campaign, including a handbook, videos, and monthly communications activities including articles, blogs and engagement.
In other areas, we are already seeing benefits from our increased focus on safety performance. The employee total recordable incident rate declined by 10 percent from 2015 and has improved by almost 40 percent since 2012, while we have also seen a significant reduction in severity of incidents, as measured by days lost rate. See Summary of indicators for full safety performance data.
Good progress has been made towards the 2020 targets for our leading indicators. The safety observation tour rate exceeded the 2020 target of 1.2 per employee, while the rate of hazard reporting was more than double the target rate of two per employee. From 2017, the hazard reporting target for ABB’s internal dashboard has been changed to proportion of hazards resolved, reflecting progress from safety awareness raising to hazard prevention.
Certified health and safety management systems were in place at 408 of 583 reporting locations (70 percent), covering 81 percent of employees. The development and roll out of The ABB Way, our common HSE/Sustainability management system will be completed by 2020, with the aim to ensure all ABB employees and contractors are included within its sphere of control and governance processes.
81% employees
covered by certified health and safety management systems
Secure operations
ABB is committed to conducting secure, ethical and respectful business globally by applying best practice when safeguarding our personnel, including contractors and other third parties under our legal care, our assets, both tangible and intangible, the resilience of our business and our reputation.
In an increasingly volatile and insecure world, ABB has been placing greater emphasis in recent years on the security of our people and contractors, particularly in high-risk countries or during crises. We have established travel security policies and procedures to protect the security and wellbeing of anybody traveling abroad on behalf of the organization and have established travel risk mitigation measures and tools that allow us to monitor our travelers and provide timely assistance and advice when needed.
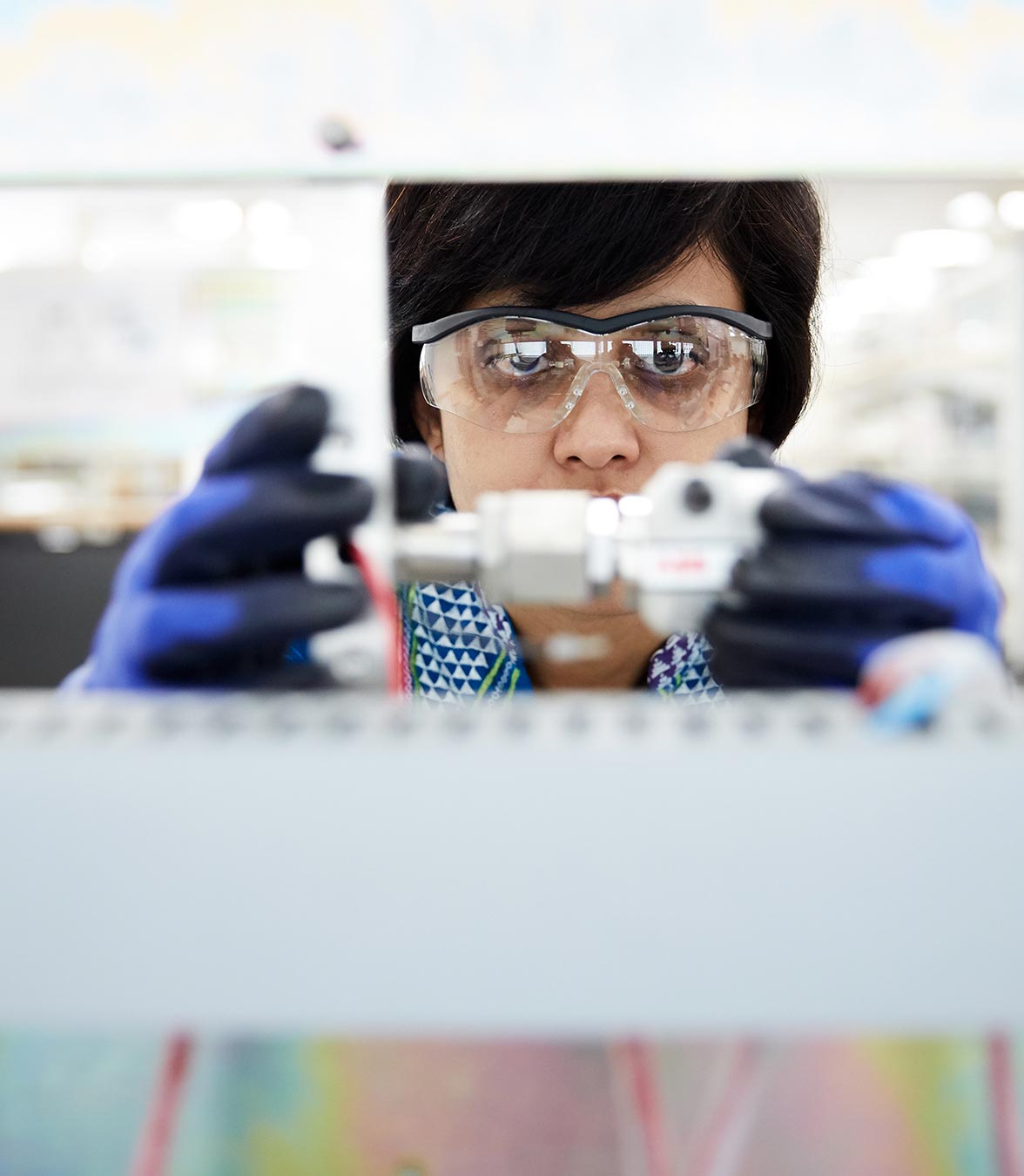
During 2016, we implemented a new travel risk management and approval process for ABB international business travelers, to provide a simpler, faster and more automated procedure that helps to ensure all travelers are both registered in our tracking system and provided with appropriate information regarding their destinations. We significantly extended the range of travel risk awareness and preparedness training available for our travelers.
Additionally, training our employees to understand how to act and react under exceptional circumstances is vital to ABB’s ability to exercise our duty of care. Crisis task forces have been established at the Group, region, country and local levels and regular and mandatory training sessions are held to ensure that these teams know how to behave in the event of a natural or man-made crisis.
As part of this commitment, the management teams in countries where ABB has operations and major projects receive crisis training every three years. During 2016, ABB’s internal corporate security staff led 23 face-to-face crisis training sessions, with a total of 84 sessions run during the period 2014 - 2016. In many cases, training is tailored to perceived threats in a region. In some countries, the threat of kidnap for ransom or extortion are seen as the greatest risk, whereas in other areas, natural catastrophes such as earthquake, fire or flood are perceived as more likely occurrences.
For our facilities and project sites, ABB’s physical security program covers a range of measures to minimize the possibility of malicious harm to anybody under the legal care of ABB and to reduce the likelihood of loss of or damage to property, information and/or reputation to as low as reasonably practicable. Standards and guidelines describe the elements that must be included in site security plans for ABB facilities and for project security plans, based on local and site- or project-specific risks.
While it is not advisable to go into detail about security challenges that ABB confronted in 2016, our security management systems and training helped us to safeguard our people, protect our assets and meet our customers’ needs – efforts that we know are likely to increase in the future.