Responsible sourcingLearning from experience
As part of ABB’s core values, we strive to set the highest quality standards for our products and services. This is why we view our suppliers as an extension of our global enterprise and an integral part of our company’s long-term success. Through collaboration with best-in-class suppliers, we help to ensure supplier compliance with ABB standards and continuous, sustainable improvement, creating value for our customers, for ABB and for our suppliers.
With operations in approximately 100 countries, ABB manufactures products in over 300 product lines and has approximately 60,000 direct material and project service suppliers. We take a structured approach to supplier qualification, performance evaluation, classification and development, with the goal to improve supplier quality, on-time delivery and compliance, while consolidating our supply base and reducing risks.
ABB clearly outlines our expectations of suppliers in the ABB Supplier Code of Conduct (SCoC), which reflects the 10 principles of the UN Global Compact and the content of ABB’s Code of Conduct. During 2016, we updated the SCoC to address new legislation on human trafficking and modern slavery in the value chain and provided training to supply chain managers around the world on the issues involved, including how to identify and respond to risks.
Supply base management driving improvement
Our process to register and pre-qualify new suppliers is operated through our partner Achilles. The centralized, online supplier registration and prequalification system means up-to-date, accurate and validated information is available to all our purchasing specialists around the world.
Supplier qualification, performance evaluation and classification processes are conducted in-house, according to standard, global processes. These processes are mandatory for all suppliers of direct materials or project services where annual ABB spend is above $5,000.
An initial company risk evaluation, covering sustainability, compliance, quality, supply chain and financial risks, determines the required steps in the qualification process; a higher risk rating leads to more stringent qualification steps. All suppliers must be certified according to ISO 9001 or a similar quality management standard and suppliers of materials or services classified as high HSE risk are strongly recommended to be certified to ISO 14001 and OHSAS 18001 for environmental and health and safety management.
The supplier classification process takes into account the supplier’s qualification status, compliance status, actual performance and overall strategic fit. ABB can clearly identify the suppliers best aligned to our sourcing strategies and standards, and channel spend to those classified as ‘Preferred’ and ‘Approved.’
ABB’s supplier performance evaluation covers external suppliers of direct material and project services, as well as internal suppliers of direct materials and transport and logistics suppliers. The process is required annually for at least 60 percent of spend in each local business unit. The results of evaluations drive supplier development processes and are important input to supply base consolidation efforts.
3,500+
critical suppliers trained since 2011
As part of our continuous improvement efforts and to reinforce ABB’s health and safety requirements of project contractors, in 2016 we rolled out a new, global construction contractors qualification process (CCQP). By applying the CCQP to assess contractors’ health and safety practices and performance, previous project experience, capabilities, equipment, tools and personnel, we help to secure the quality, safety and compliance of our projects and also enable classification and sharing of our best contractors across ABB’s businesses. The process is now implemented for both new and existing contractors in all types of field construction services.
Promoting material compliance
ABB’s suppliers also play a significant role in helping to ensure that hazardous, prohibited and restricted materials are controlled along our supply chain. To make sure that the materials and components we use and the products we produce comply with our own and our stakeholders’ standards, ABB has compiled a list of prohibited and restricted substances, referencing international regulations. Our suppliers are required to comply with this list and we have produced a guide and training materials to support suppliers’ understanding of their obligations.
Our suppliers are also key partners in identifying and preventing “conflict minerals” entering ABB’s supply chain. ABB, along with many other companies, is required to report to the United States Securities and Exchange Commission (SEC) on the extent to which we use what are known as “conflict minerals”, principally gold, tin, tungsten and tantalum (3TG), mined in the Democratic Republic of Congo or an adjoining country. Under the Dodd-Frank Act, companies must report annually to the SEC to describe our ongoing efforts to determine the origin of the 3TG minerals used in ABB products. In 2016, we provided our third report, covering 2015 activities.
During that reporting year our engineering and R&D teams identified the products and components likely to contain 3TG minerals for a large part of our impacted product portfolio and supply chain management linked these to the relevant suppliers. Each year, ABB requests thousands of suppliers to provide information on the use of comflict minerals in the products supplied to ABB and in this reporting year, the response rate improved significantly to 72 percent. In addition, ABB provided conflict minerals training to around 3,800 suppliers and to around 3,000 ABB employees in engineering, R&D, sales and supply chain management. So far, 379 smelters and refiners of 3TG used by our extended supply chain have been identified and reported.
ABB has also increased our participation in the Conflict-Free Sourcing Initiative and provided assistance to increase the number of identified smelters and refiners participating in the Conflict-Free Smelter Program.
For a second year running, ABB has been recognized for responsible sourcing of minerals. Two independent benchmark studies, conducted by Development International and Responsible Sourcing Network, assessed and ranked the performance of companies working to prevent conflict minerals entering their supply chains.
Developing supplier sustainability performance
ABB’s Supplier Sustainability Development Program (SSDP) focuses our efforts to ensure compliance with the ABB Supplier Code of Conduct and to support continual improvement in the sustainability performance of our suppliers. The program is structured around a combination of training for both suppliers and ABB employees, on-site assessments and monitoring of performance improvement plans.
980+
in-depth supplier sustainability assessments conducted since 2010
We prioritize suppliers to participate in the program according to a risk matrix, which includes the criticality of the supplier, country risk, commodity risk based on operations characteristics, and spend volume. The selected suppliers receive training about ABB’s global requirements regarding sustainability standards and on practical ways to improve their performance. We then conduct sustainability assessments at the premises of selected suppliers to identify remaining gaps, and help them to develop improvement plans, which are monitored to ensure timely completion. We focus on tier one suppliers in priority countries, which included Argentina, Brazil, China, Colombia, India, Indonesia, Malaysia, Mexico, Peru, Poland, South Africa, Thailand, Turkey and Vietnam by the end of 2016.
Download XLS (23 kB) |
Supplier Sustainability Development Program a |
2016 |
2010 - 2016 |
||||||||
|
||||||||||
Number of ABB employees trained |
377 |
2,011 |
||||||||
Number of suppliers trained b |
326 |
3,549 |
||||||||
Number of suppliers assessed b |
226 |
984 |
||||||||
Number of risks identified c |
839 |
3,162 |
||||||||
Number of risks mitigated d |
693 |
2,178 |
Focusing on continuous improvement
To support suppliers on their journey and to better focus our development activities on the relevant supplier needs, ABB periodically reviews the gaps identified during supplier assessments and identifies the most common non-compliances. During 2016, we repeated this review, covering more than 80 percent of the suppliers assessed during 2014-2016. The analysis was performed both at global and at regional level and identified supplier inability to conduct health and safety risk assessments and environment risk assessments as the root cause of several, common non-compliances. ABB regional teams then used these conclusions to reinforce their supplier training programs.
During the year we also revisited our overall training approach. Instead of conventional classroom and discussion based training, we deployed a more problem oriented, application based approach. A pilot for this was launched in India, where we conducted three workshops at manufacturing locations in Bangalore, Vadodara and Nashik. The workshop participants worked as teams to address selected problems and later presented their conclusions in plenary for discussion and peer review. In order to reach out to even more suppliers, we introduced e-learning programs covering the issues of ethics and integrity, and health and safety. The e-learnings are based on practical situations that might arise during the course of suppliers’ operations, and could lead to compromised integrity of the business or safety of its workers.
Top ten sustainability non-compliance issues |
||
General management |
|
|
Labor and human rights |
|
|
Health and safety |
|
|
Environment |
|
|
To further support the implementation of robust health and safety practices, we made ABB’s Code of Practice for Safe Working freely available to our suppliers. The document details safety risks involved in various industrial activities and outlines appropriate mitigation actions. The content is also demonstrated in e-learning modules.
Internal training efforts during 2016 included a series of 10 live webinars covering the concept of responsible sourcing and ABB’s supplier development initiatives. The facilitated discussions that followed these training sessions provided further input regarding common ‘gaps’ or non-compliances identified among suppliers, which then fed into local prioritization of supplier support activities.
Creating value for suppliers
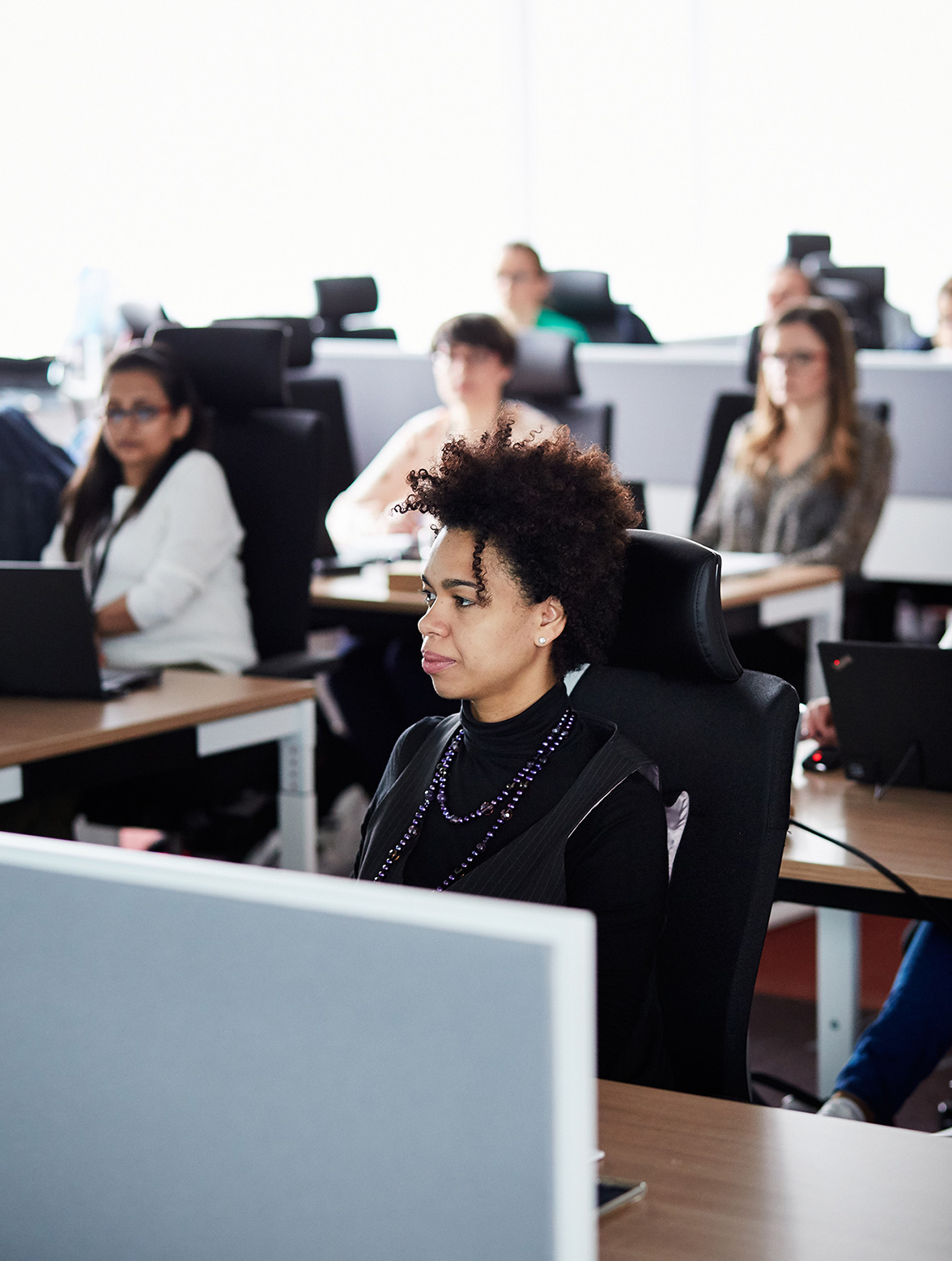
Although there is no doubt that developing sustainable manufacturing practices brings benefits for suppliers, such as productivity improvement, reduced overheads and improved regulatory evaluations, the benefits achieved are not always easy to quantify. This can fuel a misconception that working in a responsible and compliant manner leads to higher costs, which can lead to skepticism and limit suppliers’ interest in SSDP participation.
In order to address these concerns and provide fact-based business cases for suppliers, ABB has collated a number of case studies outlining the value created for suppliers following participation in the SSDP. Some of the past cases have shown instances of over 30 percent improvement in productivity, along with dramatically reduced working hours and increased organizational maturity.
For example, early assessment of our supplier, Unique Punch System Pvt. Ltd in India, identified improvement potential in several areas, including safety and environmental parameters and risk assessments. Initial hesitation from the supplier’s end was overcome by intensive engagement by the ABB supply chain management team, leading to successful implementation of risk assessment over the course of a year. This resulted in safer operations, proper waste management, increased understanding of statutory requirements, better relations with customers and readiness to enter new markets.
Moving forward in 2017
The supplier sustainability development program will continue to grow, expanding into three new countries, Bulgaria, Saudi Arabia and United Arab Emirates, in 2017. In preparation, the local supply chain teams were on boarded and localization of global ABB supplier sustainability requirements was completed during 2016, ready for program kick off early in 2017.
We will also continue our initiative to quantify and document the cases of benefits achieved from implementing sustainable manufacturing practices. Initiatives will be launched in India and Turkey, where we have identified the need for additional supplier engagement.