Resource efficiency Making our operations smart and sustainable
ABB is progressively reducing the environmental footprint of its sites around the world
In our drive to reduce ABB’s environmental impact, we are optimizing our use of resources, minimizing waste from our operations, increasing the share of waste that is reused or recycled, and ensuring that the products we produce and the materials we use comply with our own and our stakeholders’ standards.
Distribution of water withdrawal in 2018 (2013)
Water withdrawal in water-stressed areas 2014–18
In the area of resource efficiency, we have established two targets. The first target is to reduce absolute water withdrawals by 25 percent from 2013 to 2020 at facilities located in watersheds with medium to extremely high baseline water stress. Even though most of our manufacturing processes do not consume significant amounts of water, ABB remains committed to reducing the water impacts of its operations. We use the World Resources Institute’s Aqueduct global water risk tool to map our facilities and classify them according to the level of baseline water stress of the local watershed. Of the 554 ABB locations mapped in 2018, 73 face an extremely high level of water stress, 109 face a high level, and 94 face a medium-to-high level.
Waste and recycling
For all ABB sites in stressed watersheds, total water withdrawals in 2018 were 12 percent lower than the 2013 baseline. The addition of new ABB sites in China and the Middle East contributed to a 3 percent increase to ABB’s withdrawals in stressed watersheds compared to 2017. Thanks to structural changes at several ABB sites in Europe, in 2018 ABB’s total water use went down by 5 percent, to 8,800 kilotons.
Our primary water-saving practice is the use of closed-loop systems, which saved 75 percent of all industrial water use and 47 percent of all cooling water use at ABB sites worldwide. There are more than 20 ongoing water reduction projects running across ABB in 2018. For example, by improving the closed loop technology for its board and paper machine, ABB’s transformer insulation material site in Roigheim, Germany, saved 144 kilotons of freshwater in 2018, 50 percent more than was saved in 2017.
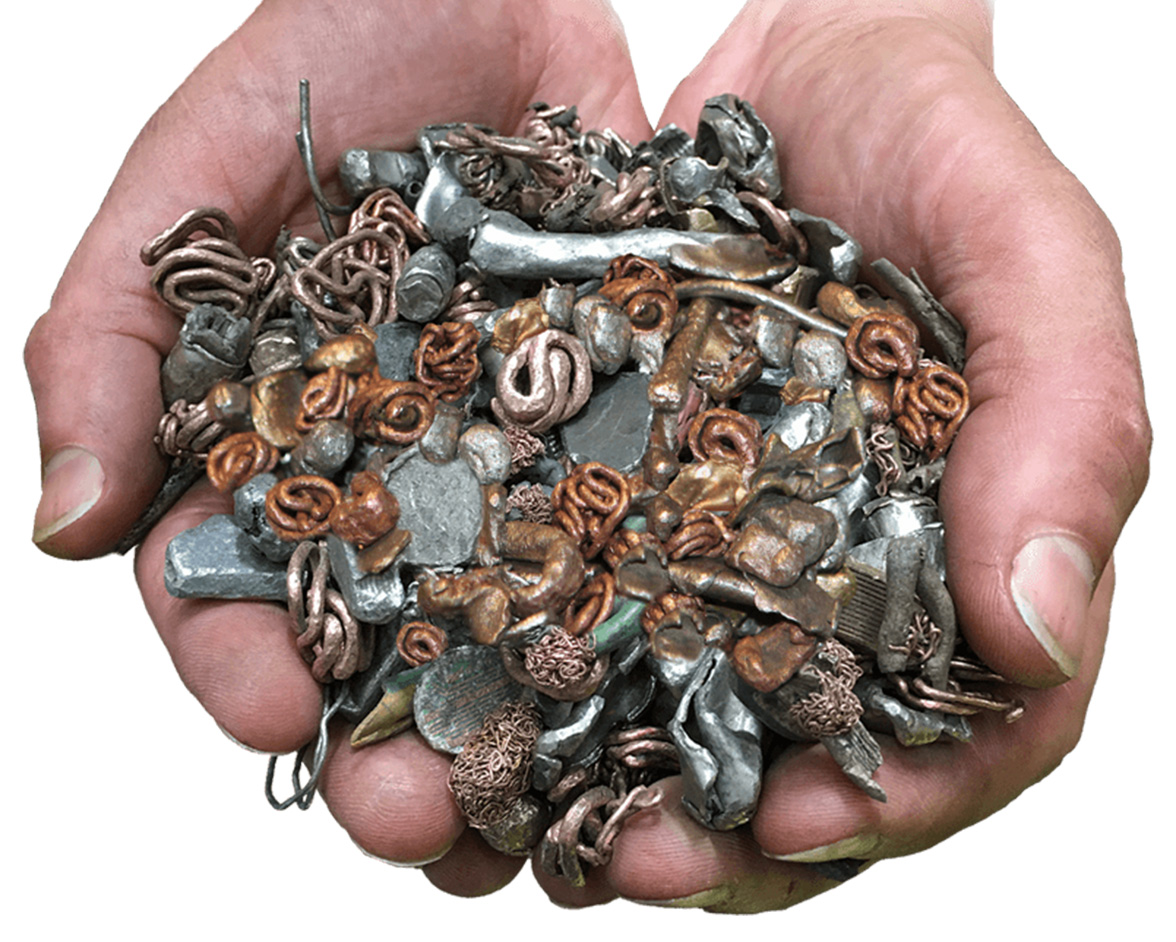
One important water-related initiative in 2018 was to significantly simplify the way we report on ABB’s use of water. This change will make it easier to monitor ABB’s water use and track our progress against our targets. Another important step was improving the ability of our business lines to track their performance regarding resource efficiency, and our business leaders have been fully briefed on the reasons why resource efficiency, water management, waste reduction and recycling are important to ABB.
This improvement has significantly increased, at all levels, our business lines’ accountability for the environmental impacts of their operations. It has not only contributed to our achievements related to our 2020 water target, but also to our second resource-efficiency target, which is to reduce the share of waste ABB sends to final disposal – both hazardous and non-hazardous – by 20 percent from 2013 to 2020.
In 2018, we reduced the proportion of waste sent to final disposal to 16 percent, compared to 20 percent in 2013. In-house recycling and reuse, mainly of packaging materials and thermoplastics, reduced the amount of waste by 1,800 tons. Compared to 2017, we reduced the amount of hazardous waste ABB sends for final disposal by more than 20 percent to 6,200 tons. More than 90 recycling and waste reduction projects were underway at ABB in 2018.
For example, ABB’s manufacturing site for solar inverters in Terranuova Bracciolini, Italy, started recycling the metal parts from inverters taken back from customers; this initiative saves roughly 100 tons of metal and more than US$450,000 every year.
It is critically important for industry to work toward the creation of a circular economy
Prof. Dr. Volker Hoffmann – ETH Zurich
ABB Stakeholder Panel
To support the achievement of our waste reduction target in 2018, we shared best practices across ABB and provided further guidance on how to reduce waste generation and increase recycling rates.
Case study Eliminating waste at ABB facilities
Reveal case studyIn 2018, ABB’s motors and generators facility in Shelby, North Carolina, USA, achieved zero-waste landfill status. By using some of the same vendors who enabled ABB’s manufacturing facilities in Greenville, South Carolina, and Marion, North Carolina, to become zero-waste sites, the Shelby site was able to rapidly engage companies that could take its waste and either recycle it or turn it into energy.
Regardless of the production processes used, the manufacture of motors, generators and other industrial products will always create some waste, including scrap wood, copper and other metals, rubber, coolants, oil, used batteries, shredded documents, and even e-waste. At ABB Shelby, the largest portion of its total waste stream was this kind of rubbish that, until recently, was disposed at landfills. By partnering with VLS Recoveries in Gray Court, South Carolina, Shelby was able to turn all its roughly five tons per month of plant waste into energy.
To find out if ABB Shelby’s waste could be processed, a sample was sent to VLS Recoveries. The company analyzed the sample waste stream and deemed that no additional sorting would be required. In turn, ABB Shelby performed an environmental compliance audit on VLS to validate their processes.
Close case study