Responsible sourcing Forging a sustainable supply chain
ABB’s robust policies and procedures ensure we address the social and environmental impacts of our procurement processes
ABB closely monitors the sustainability performance of its suppliers. The Supplier Code of Conduct (SCoC), published in 16 different languages, communicates our expectations and performance standards to existing and potential business partners. It is one of our suppliers’ contractual obligations, as part of ABB’s general terms and conditions. In 2018, we updated our routine procurement processes to include sustainability parameters at the stage of qualification and performance evaluation.
True partnerships rely on responsibility, transparency and a “one team approach”
Barbara Myrczek – Fideltronik
ABB Stakeholder Panel
We continue to deploy a special intervention, the Supplier Sustainability Development Program (SSDP), to proactively screen and prioritize (using a combination of geographical, category and economic factors) the sustainability risks posed by suppliers, evaluate their adherence to the SCoC, and engage with them where necessary. The SSDP involves supplier trainings, onsite assessments and collaboration with suppliers to find sustainable solutions. The SSDP assesses supplier performance on 42 parameters across general management, working conditions, safety, environment, and associated local regulatory requirements.
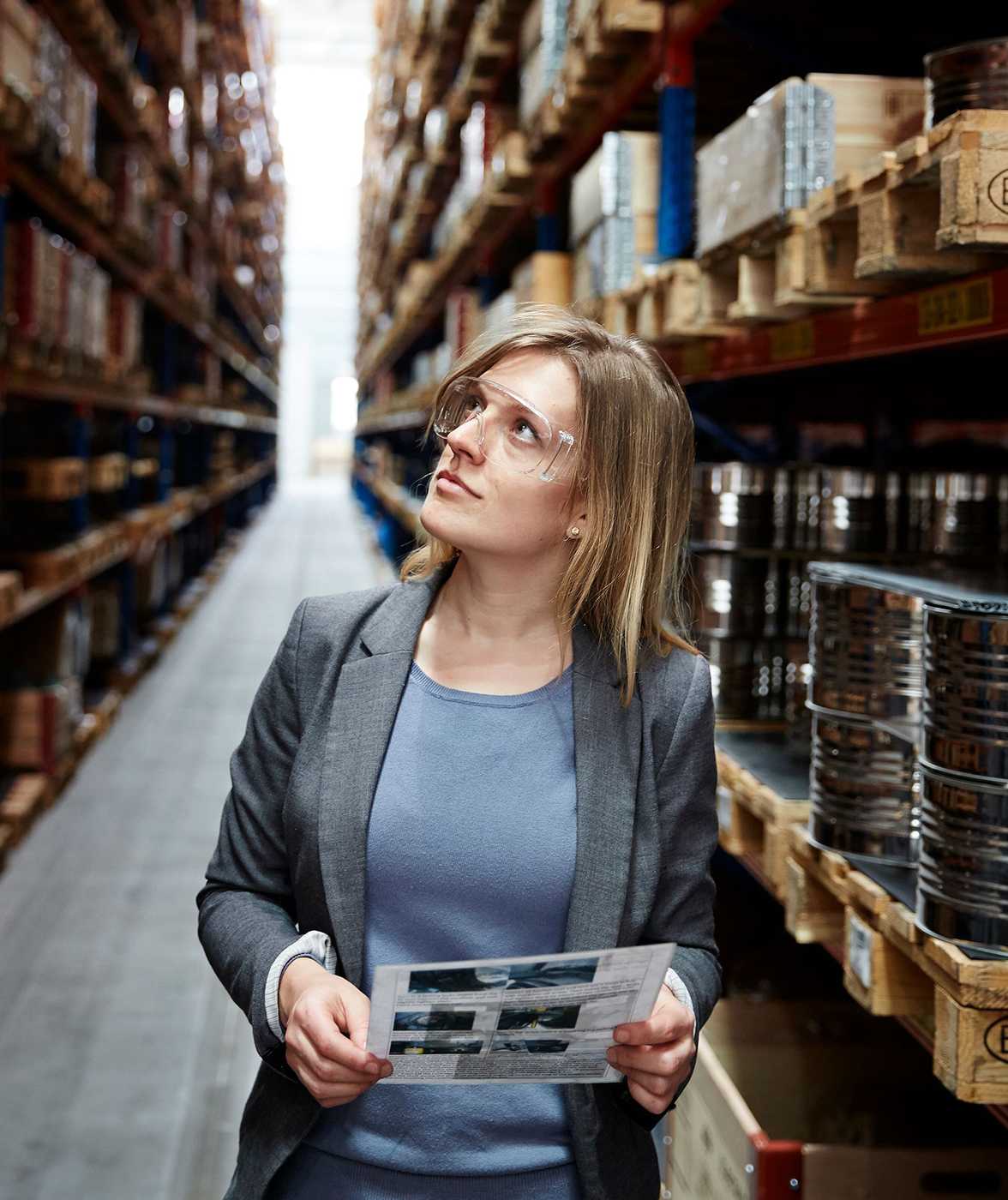
Every year, ABB trains, coaches and assesses hundreds of suppliers on sustainability topics. In a continuous process, old risks are closed and new ones are identified each year. The time required to close these risks typically ranges from eight months to over a year, in the case of complex issues that may require a collaborative effort to resolve. Since 2015, we have identified an average of 760 new risks each year. Due to the ongoing identification of new risks and the time required to mitigate them, our closure rate for identified risks can never be 100 percent.
Our 2020 target is to close 65 percent or more of identified risks from supplier assessments. In 2018, ABB is on track to exceed our target, closing 76 percent of identified risks by Q4 2018, up from 72 percent in 2017. We achieved this strong result by using all of the expertise, knowledge, resources and best practices at our disposal to support our suppliers. For every area of noncompliance identified during our supplier assessments, we launch a major supplier support action to systematically address each issue in turn. Our support actions include capacity building, customized participatory workshops, sharing best practices, jointly implemented collaborative programs, and transfer of knowledge and expertise. In 2018, this proactive approach resulted in a better supplier response and improved performance standards.
Among other key initiatives in 2018, we designed a participatory workshop for ABB suppliers in India, China, Saudi Arabia and Indonesia on the local legal requirements that correspond with ABB’s SSDP requirements. We also launched support programs in China, India, Turkey, Bulgaria and Poland to work hand-in-hand with suppliers to find innovative solutions for some of the chronic challenges they face regarding working conditions. On the technical side, an ABB pilot project used a business intelligence tool to reduce the manual intervention in our data reporting processes. We will deploy this tool across ABB in 2019.
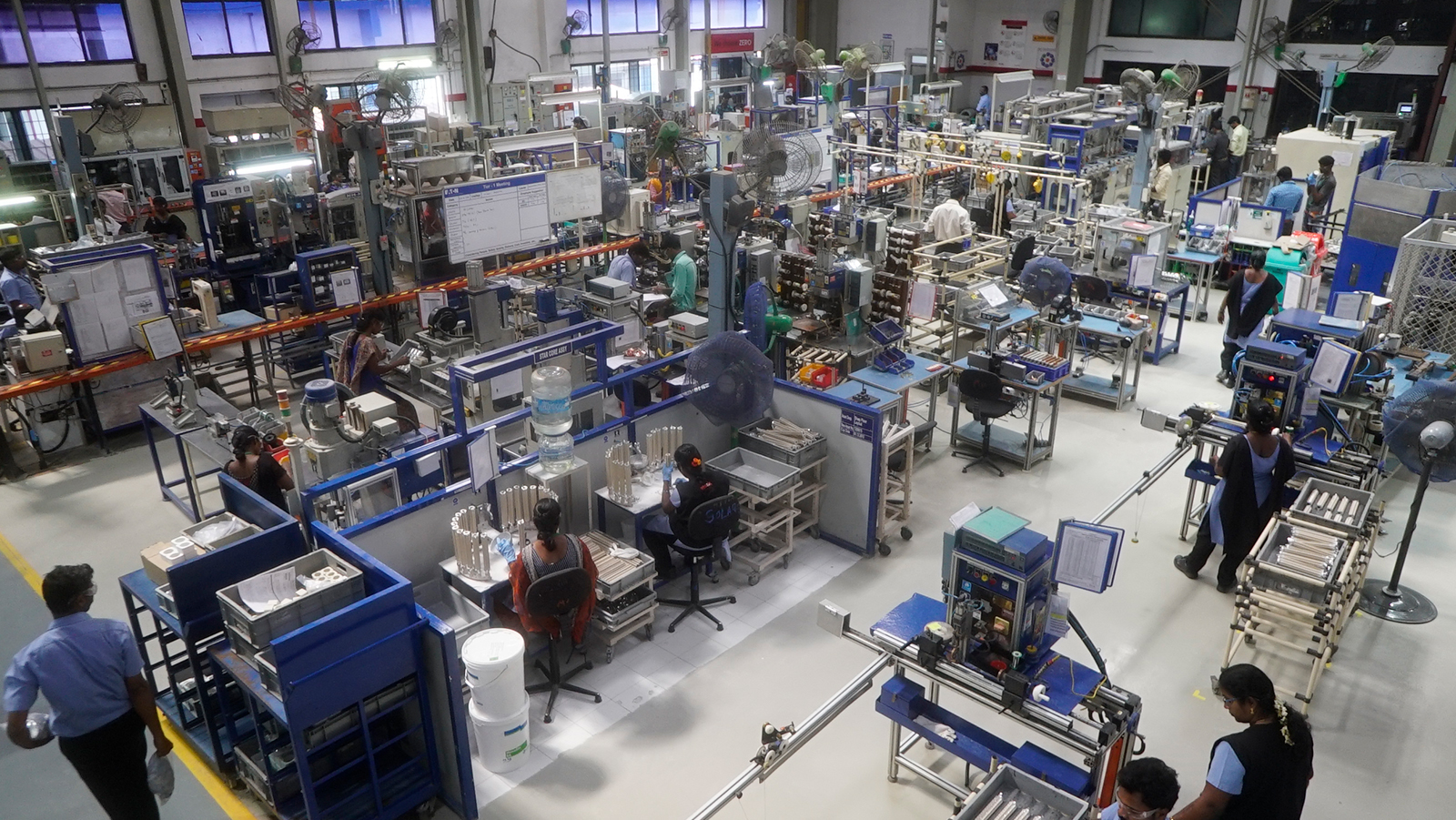
Case study Sustainability measures improve supplier’s operational and business efficiency
Reveal case studyBy working with our suppliers to find solutions for their chronic sustainability challenges, we can boost their operational performance while solidifying ABB’s supply base.
In one such collaboration, we partnered with a key supplier to ABB’s drives business in India to help it cut down on excessive overtime. This common challenge for suppliers presents regulatory, safety and health risks. As typical resolution mechanisms are “believed” to reduce business efficiency, suppliers are often skeptical of proposed solutions.
ABB worked with this supplier to introduce shorter planning and review cycles, coupled with close tracking of performance data from the shop floor. This corrective measure enabled the supplier to track the hours worked by each employee on a daily basis and to recognize which employees were on the verge of crossing the legally mandated limit for working hours. On the preventive side, we worked together to eliminate production bottlenecks and increase its proportion of multi-skilled employees from 30 to 80 percent.
Thanks to these measures, the supplier was able to reduce its overtime by 30 percent in 2018. It also achieved a 93 percent reduction in cycle time, doubled its output, and reduced the need for human intervention by 75 percent, for certain processes.
Close case studyDuring our supplier assessments in 2018, a supplier audit uncovered one instance where a large supplier in Malaysia routinely retained the passports of its migrant workers. When these workers applied for the return of their passports, a third-party employment agency would retain one month’s salary until the worker returned to the supplier. Further details on this incident and the corrective measures taken by ABB can be found in the case study featured on page 36 of this report.
In 2018, we assessed 190 suppliers, identifying 676 risks. We mitigated 674 risks during this period. In other activities to support responsible sourcing, we trained 136 ABB employees and 415 suppliers during the year.1
1 Risk is defined as the danger posed to ABB by the non-compliant operations of the supplier. Risks can be extremely high, high, medium, or low, depending upon the severity of supplier non-compliance identified during onsite audits. To reflect the degree of severity associated with instances of non-compliance, we multiply the total number of extremely high risk suppliers by a factor of 5, the total number of high risk suppliers by a factor of 3, the total number of medium risk suppliers by a factor of 1, and the total number of low risk suppliers by a factor of 0. The total number of risks identified is the summation of all individual risks. Satisfactory completion of corrective actions by a supplier results in a reduced number of risks.