Right materials Eliminating unsafe substances
ABB is phasing out hazardous substances from products and processes wherever possible
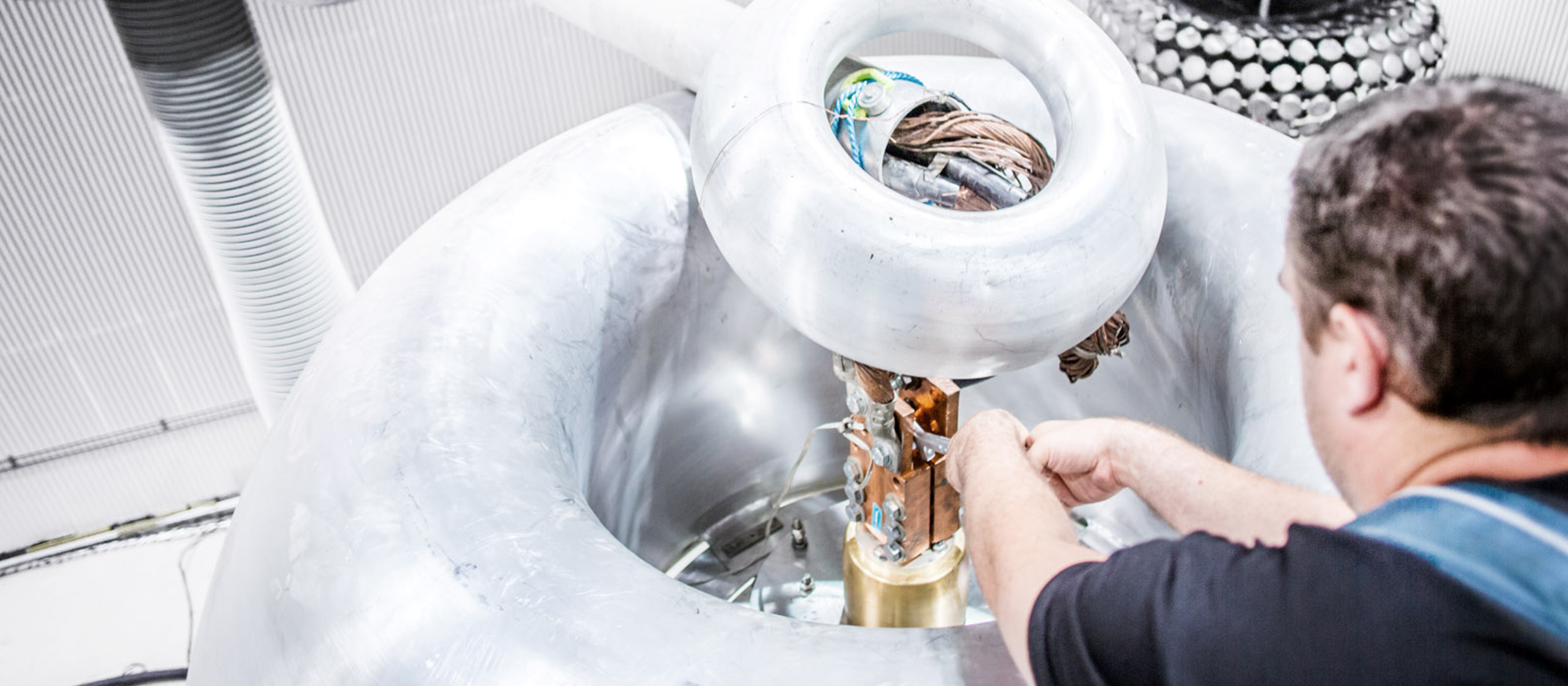
To expedite the reduction of hazardous substances in our operations, we have compiled the ABB List of Prohibited and Restricted Substances. This list, which is updated regularly in line with international regulations, applies to all our operations, including sourcing of goods, product development, production processes, products, packaging materials, service activities and construction sites.
Emissions of volatile organic compounds
As regulatory compliance is also part of ABB’s Global Terms and Conditions for suppliers and our Supplier Code of Conduct, we have developed a companion guide to the list to support suppliers’ understanding of their obligations. These obligations include their ongoing partnership with us to identify and prevent restricted substances and conflict minerals from entering ABB’s supply chain, as outlined in the ABB Policy on Conflict Minerals.
For hazardous substances, our 2020 target is to reduce ABB’s emissions of volatile organic compounds (VOCs) by 25 percent from 2013. This target further sharpens our strong focus on reducing the use of substances that are harmful to human health and the environment.
We performed well against our 2020 target over the past year, as our VOC emissions decreased by 11 percent compared to the year before. This means ABB has surpassed the 25 percent reduction target we set for 2020. Since 2013, ABB has reduced its VOC emissions by 27 percent, and we are committed to achieving even greater reductions in the years to come. We achieved this result through measures such as switching to paints and varnishes with less VOCs and the installation of more active carbon filters and other such equipment at our sites.
Case study Phasing out lead at ABB Sweden
Reveal case studyABB Sweden (SEABB) keeps track of all the materials used at its sites, identifies which ones are hazardous, and mandates that concrete phase-out plans be developed for the most hazardous ones.
One such hazardous material that SEABB was keeping track of was lead. It developed phase-out plans for it, and then successfully substituted less hazardous materials for it in production processes. The benefits of SEABB’s proactive approach became clear when lead became an EU REACH regulation candidate list substance in June 2018.
SEABB’s phase-out plans, such as the one they carried out for lead, are aggressively followed up until the hazardous materials in question have either been removed from its production processes or replaced by a less harmful substitute. Naturally, this is not a simple procedure, and it typically requires considerable R&D efforts to completely phase-out and replace a hazardous chemical.
Each year since 2014, SEABB has successfully phased out 10-15 percent of all hazardous materials or work activities that involve hazardous materials. At the same time, because previously non-hazardous chemicals are continually being reclassified as hazardous, it is not possible for the number of high-risk work activities at SEABB to decrease in step with the high phrase-out rate it is achieving.
Close case studySince 2015, we have made tremendous progress in our effort to phase hazardous materials out of ABB’s production processes. We have reduced our use of chlorinated paraffins by 100 percent, dimethyl phthalate by 100 percent, lead chromate pigments by 87 percent, boric acid by 83 percent, amines by 61 percent, and aluminosilicates by 46 percent. Major initiatives, such as the screening program ABB’s Electrification Products division set up in 2018 with its suppliers to monitor and eliminate hazardous substances from components supplied to ABB, are key to our continued success in this important endeavor.
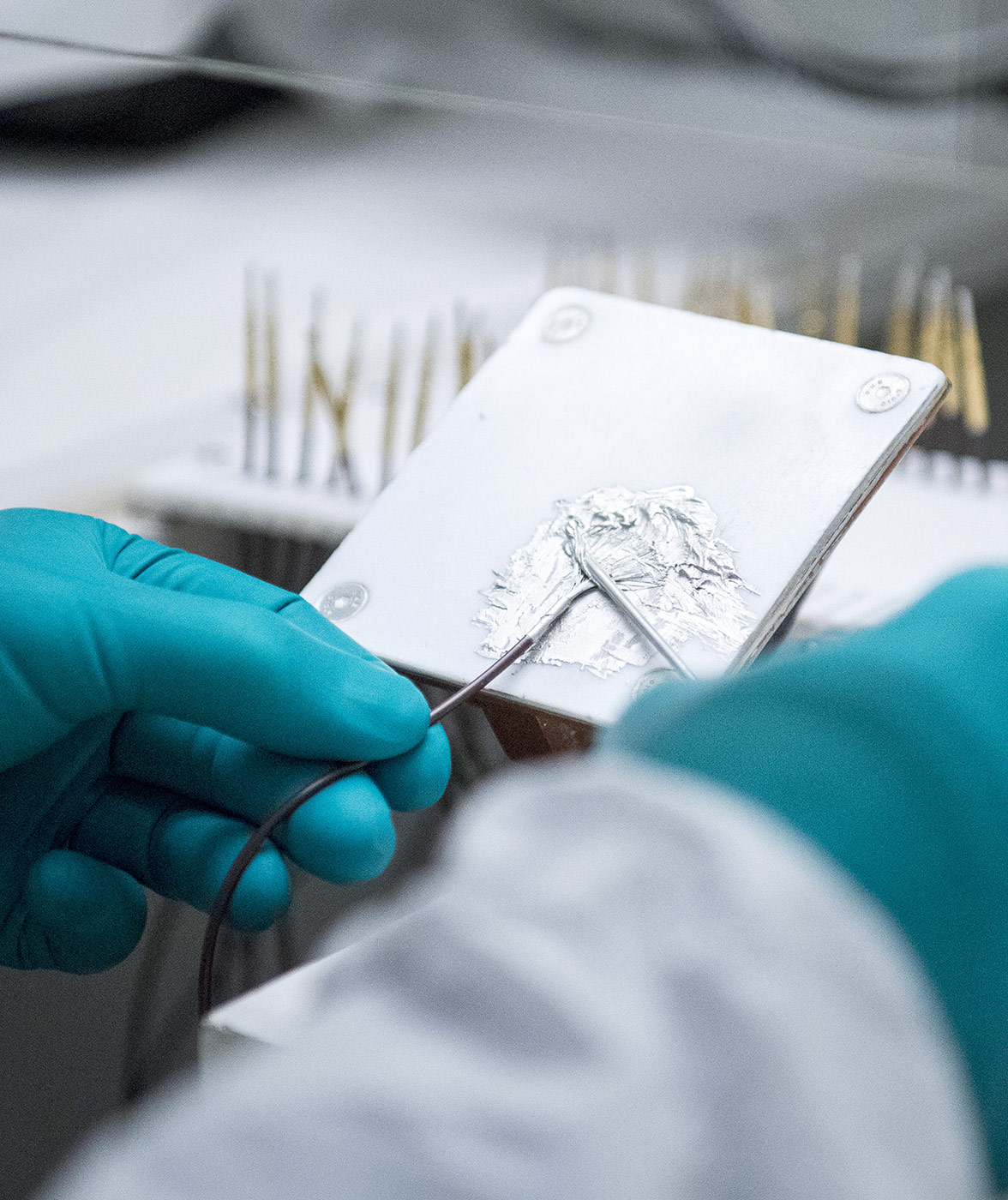
In 2018, we strengthened the cross-functional material compliance team that we formed in 2017 by adding new members to its roster. The team’s mission is to facilitate a standardized and systematic approach to the increasingly complex material compliance regulations we face in our global markets, based on best practices. In 2018, the team launched a newly updated material compliance portal to better spotlight business-critical information. The team also conducted the first set of live trainings using a new webinar training package to educate employees on the REACH regulation, RoHS directive and the ABB List of Prohibited and Restricted Substances. Feedback on this webinar, titled “REACH, RoHS and ABB List at a glance,” from ABB’s business units was positive. The company-wide release of this webinar is part of ABB’s HSE/SA business plan for 2019.
Additional initiatives include the introduction of new control standards for R&D and product development, a new approach to supporting supplier communication processes that enable ABB to perform active due diligence, and simplifying reporting processes for hazardous substances and VOCs used in ABB’s operation. This last initiative will markedly improve the quality of our reported data.
In 2018, 37 projects were underway to reduce and phase out hazardous substances and VOC emissions. Due to the variety of products and manufacturing processes across our organization, hazardous substances are generally reduced on a site-by-site basis.
For example, our electric motor factory in Weaverville, North Carolina, USA, redesigned its Sleevoil bearings offering so they could use tin instead of lead in this product. This step reduced the annual amount of lead ABB sells and distributes around the world by 58 tons, while reducing the amount of lead-bearing hazardous waste at the Weaverville site by 4.5 tons.