Safe operations Leveraging clarity of accountability and lessons learned to eliminate incidents
ABB’s paramount concern is to provide for the safety and security of its people and its assets
Health and safety is at the center of everything we do. Our first priority is to assure the health and safety of all ABB employees; this priority is embedded into our core values.
A significant area of focus for the company in 2018 was the implementation of the ABB Way. This new HSE/SA global management system is a key element of our sustainability governance framework, and its implementation has enabled us to reduce our more than 300 independently certified HSE/SA management systems down to one standard system for everyone.
As an investor, we’re interested in the connection between a company’s sustainability efforts and the health of the business
Laura Kunkemueller – Mellon
ABB Stakeholder Panel
Implementing the ABB Way has clarified and simplified our expectations for performance, while enhancing awareness and knowledge of performance requirements across the organization. Once this single management system was firmly established, we were able to increasingly define and consolidate our health, environment and security performance standards. In parallel with this project, we successfully implemented further global applications from our new information systems (IS) platform for HSE/SA management.
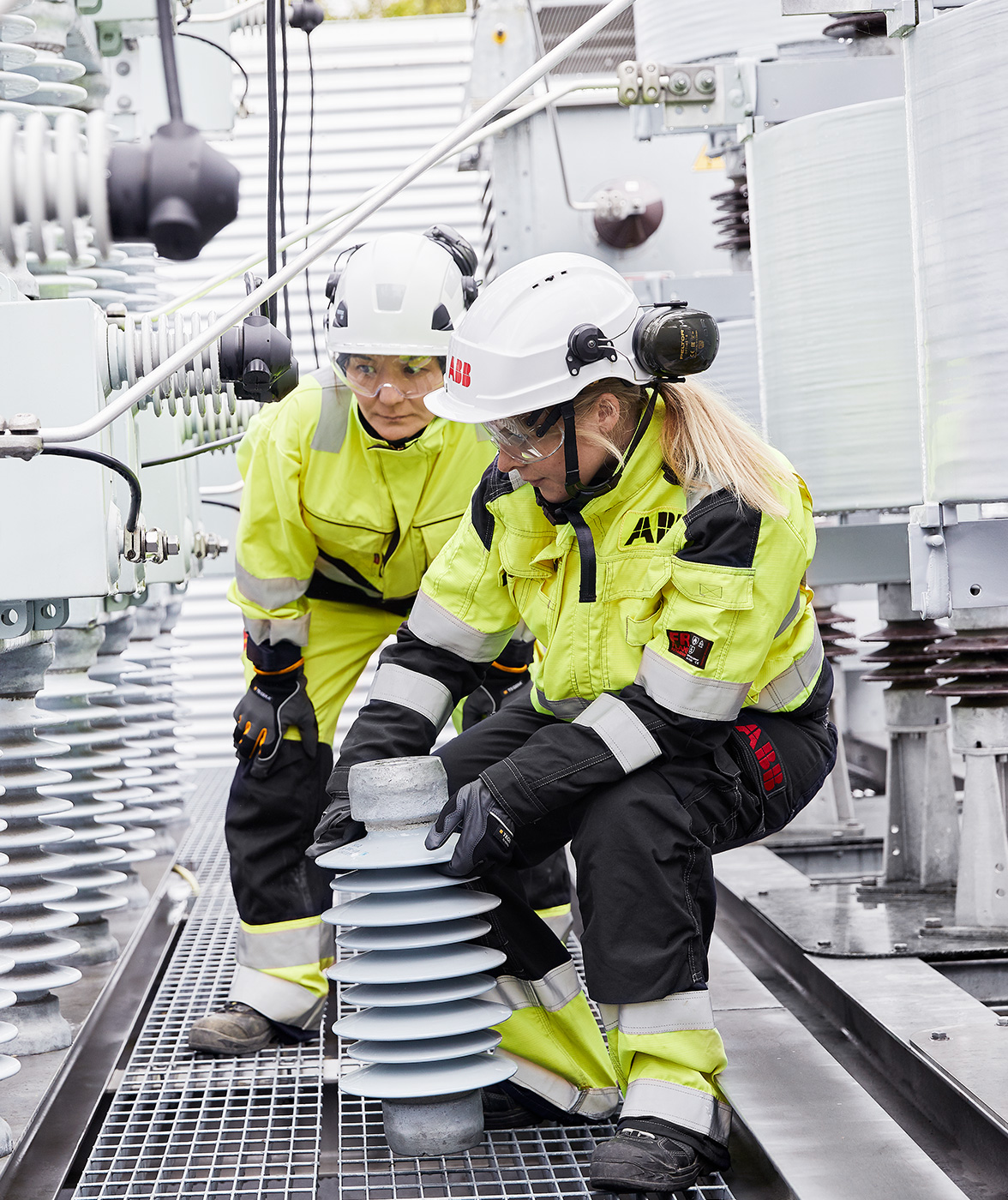
Together, the common standards and the IS platform provide the strong foundations for ABB’s performance and will support our continued drive towards zero incidents.
Our target for safety and security is to reduce the employee total recordable injury frequency rate (TRIFR) to less than 0.7 by 2020. We performed well in 2018, with our employee TRIFR ending the year at 0.58, down from 0.75 in 2017. This continued progressive improvement to industry standards represents 251 fewer lost time injuries than the previous year. While we are currently ahead of our 2020 target, we are fully aware that past performance is no guarantee of future results. That is why we are committed to maintaining our strong positive momentum, and to working toward achieving a TRIFR of zero.
Regrettably, even though the indicators are all positive, ABB also sustained four fatalities in 2018. Under ABB’s new, improved common standards for investigations and revised processes for the training and assignment of lead investigators to all levels of incidents, these unfortunate incidents were thoroughly investigated to understand their root causes, take action to mitigate them, and derive all possible lessons learned. For example, we are now working to improve our initial evaluation processes for contractors and approved service providers; our goal is to maintain high levels of competence among all those engaged to work on ABB’s behalf.
ABB’s global independent HSE/SA audit and assurance program is also proving to be a valuable means of enhancing the company’s knowledge and skills. In 2018, the first full year of this program, we completed nearly 200 individual standardized assurance audits across our businesses and global operations. These audits, which provided excellent opportunities for engagement and learning for local teams, are well received, and all action items are recorded, followed up, and tracked to completion.
Case study The ABB Life-Saving Rules
Reveal case studyThe “Don’t look the other way” initiative, which encourages employees to proactively report any potentially unsafe actions or conditions, has become a cornerstone of ABB culture. Safety is ABB’s top priority, and our people have fully bought in to the idea that “looking the other way” is unacceptable.
To underpin this culture of safety, ABB recognized it needed to provide its people with clear, observable expectations for practical, safe behavior. To this end, in 2018 a cross-business working group analyzed global best practices for life-saving rules and researched internally existing ad-hoc and individual life-saving rules. Based on their findings, the working group used an incident and risk-based perspective to determine which life-saving rules would be most suitable for ABB’s global operations.
These rules were then aligned with the ABB Fair Process to ensure they can be consistently and fairly applied. This resulted in the ABB Life-Saving Rules, which are eight simple, positive actions all ABB people can follow and observe. These rules were introduced during Safety Week 2018, and we will launch a full campaign in 2019 to promote them. The ABB Life-Saving Rules perfectly complement ABB’s Safety Commitment, which was publicly endorsed by the Executive Committee in 2014.
Close case studyThroughout the year, we continued to enhance our global safety programs, including those related to key risks, project safety, contractor management and electrical safety. In these areas, our Center of Expertise was able to gather knowledge from specialists around the world and leverage it to develop solutions and efficiently run our programs. A newly introduced program of particular note in 2018 was the ABB Life-Saving Rules. These issue-based rules complement our existing safety commitment and represent another aspect of our drive to bring clarity, simplicity and enhanced learning to all employees and contractors working on behalf of ABB.
In the coming years, we expect our sharp focus, strong programs and dedicated teams will continue to increase the safety of ABB’s operations and reduce the number of incidents across the organization.