Improving performance and reducing emissions
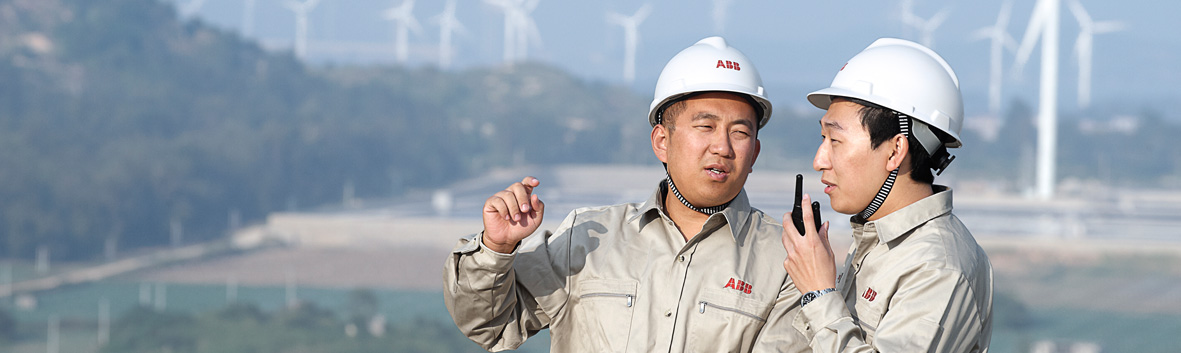
Just as we target mitigation of climate change, and energy and resource efficiency for ABB’s customers through our product and solution portfolio, we have also been working for many years to manage and reduce the impacts of our own operations. At our plants and offices, and along our value chain, actions to reduce energy consumption and greenhouse gas emissions take many forms.
Energy efficiency in operations
ABB has a relatively light energy impact within our own operations, but as part of our goal to increase progressively the efficiency of our own operations, we set ourselves the target of reducing energy use by 2.5 percent per employee per year through to the end of 2013. This includes both direct and indirect energy use, for manufacturing processes and to operate buildings. To implement the objective, our most energy-intensive sites were required to undertake energy audits and all sites were required to develop an energy saving program.
For continuing operations – those included in the 2012 energy baseline – we achieved our 2013 objective, reducing our energy consumption per employee by 3.5 percent. However, inclusion of 2013 energy data from Thomas & Betts, a company acquired during 2012, increased our energy intensity result. This is due to the more energy-intensive nature of manufacturing processes undertaken by some of the Thomas & Betts facilities, such as galvanizing and electroplating.
3.5% improvement in energy efficiency in 2013
With the release of ABB’s new Sustainability Objectives 2014–2020, we continue our commitment to energy efficiency improvement. We now target a 20 percent improvement in energy efficiency by 2020, from a 2013 baseline that includes Thomas & Betts operations.
A wide variety of energy savings projects were implemented across the company to achieve our 2013 result. Most commonly – and cost effectively – facilities implemented energy efficient lighting solutions. Other activities included investigating and enhancing compressed air systems, optimizing heating, ventilation and cooling processes, and implementing or updating heat recuperation from machines and processes, often using our own technology.
Megawatt-hours (MWh) per employee
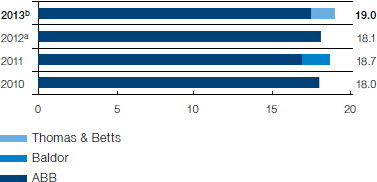
a Baldor facilities included; Thomas & Betts not included
b Baldor and Thomas & Betts facilities included
Total energy use (Gigawatt-hours – GWh)
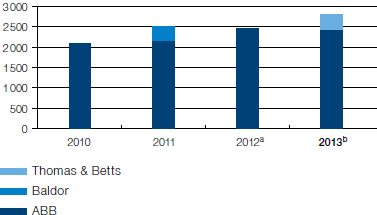
a Baldor facilities are included; Thomas & Betts not included
b Baldor and Thomas & Betts facilities included
Direct and indirect energy use by type for 2013a (2012b)
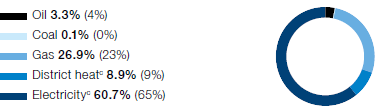
a Thomas & Betts facilities included
b Thomas & Betts facilities not included
c Not including losses at utilities
For example, our plant at South Boston in the United States, one of our top ten energy intensive facilities, undertook a systematic review of energy consumption, including lighting, motors, fans, pumps, insulation and control processes and technologies. In 2013, it began a step by step improvement plan and is already seeing results. The replacement of oversize DC motors with Baldor AC motors and ABB drives and control systems is saving energy and maintenance costs and has significantly improved productivity. We expect a payback on the more than $600,000 investment in less than two years.
Building an efficient real estate portfolio
With a portfolio of around 8.8 million square meters of building space worldwide, ABB’s corporate real estate management also plays a key role in our energy efficiency performance. The ABB Green Building Policy, introduced in 2008, sets out criteria for all new buildings, including site selection, building design and the choice of materials to optimize resources. It also details policies required for new development, refurbishment, and selection and management of rented space.
As a further step to improve the sustainability of our buildings, ABB is now implementing a focused corporate real estate energy efficiency program across Europe as a precursor to extending the project across the globe. The project is based on the highly successful Green Corporate Real Estate Management (Green CREM) strategy developed by ABB in Germany. Launched in 2007, the Green CREM program has reduced energy consumption in our German real estate by 35,000 MWh and CO2 emissions by 8,000 tons. Read more in our case study.
Reducing carbon intensity of energy
As well as working to improve the efficiency of our energy consumption, ABB also seeks to reduce the carbon intensity of our energy sources. Around five percent, or 85 GWh, of ABB’s 2013 electricity was purchased as certified “green” electricity, saving more than 18,000 tons of CO2 emissions.
Additionally, more ABB facilities are installing on-site photovoltaic (PV) power plants to reduce environmental impacts as well as to demonstrate ABB’s solar capabilities. PV plants are installed at 21 sites in 16 countries across Asia-Pacific, Latin America and Europe. Although the installations contribute only a small proportion of our global electricity needs, PV plants in Japan, Hungary and Mexico can contribute 50 percent or more of the installation’s electricity needs.
During 2013, ABB in Mexico was awarded the prestigious Mexican International Renewable Energy Congress (MIREC) Award 2012 for excellence in the development of clean energy. The award recognized ABB’s leadership in clean energy, demonstrated by the photovoltaic solar field at our San Luis Potosi facility. ABB was the first private company in Mexico to invest in a photovoltaic solar field of utility-type dimensions. The solar field, commissioned in 2012, generates 1.2 megawatts (MW) and prevents annual emissions of around 1,700 tons of CO2.
Greenhouse gas emissions
ABB’s direct greenhouse gases (GHG) emissions are mainly from fuel used in our operations, as well as from SF6 emissions during production processes and gas handling on site. Thanks to product and process re-design, as well on-going programs to improve handling, leak detection and storage, our SF6 emissions declined by almost 20 percent in our ongoing operations. However, ABB’s total direct GHG emissions remained relatively stable from 2012 to 2013, mainly due to the higher proportion of gas used as fuel at Thomas & Betts facilities. ABB’s total GHG emissions (direct + indirect) increased slightly from 1.85 million tons in 2012 to 1.87 million tons in 2013.
Direct and indirect energy use by type for 2013a (2012b)
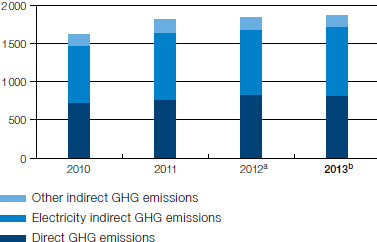
a Thomas & Betts facilities included
b Thomas & Betts facilities not included
c Not including losses at utilities
Logistics and travel
Programs to optimize logistics continued during 2013, resulting in cost savings, improved quality and reduced emissions. The largest program under way is the Transportation Management Center project in China. In the regions of Xiamen, Beijing and Shanghai, transport management for the local business units has been combined into a single operation and team. The regional teams integrate all domestic transportation needs, coordinating vendor, transport management center and factory through a unified operational process. The program will expand in 2014 to include international service from Shanghai and pilot projects at locations in India and Switzerland.
We have also made significant progress with our global packaging optimization project. More than 70 facilities have now systematically reviewed their packaging needs and are assessing the potential to optimize packaging type, size and weight. Improved packaging and loading can increase transport efficiency, thus reducing emissions, cut material consumption, improve ergonomics and provide better product protection.
Greenhouse gas emissions from business air travel decreased by almost eight percent during 2013, not including Thomas & Betts activities. To support both emissions and cost reduction targets, many locations have implemented local improvement goals to replace a certain number of internal, face-to-face meetings with virtual meetings. This has been supported by investment in improved facilities and technologies for virtual meetings.