Learning from experience
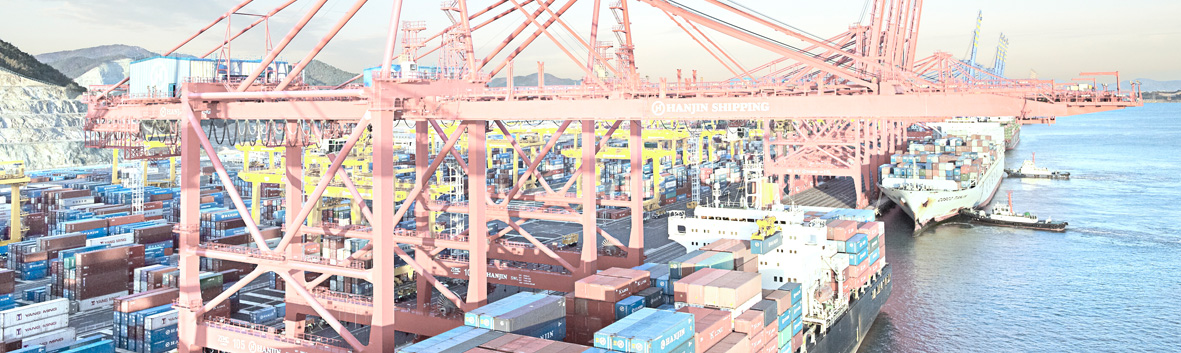
ABB currently has thousands of active direct material and project service suppliers all over the world who represent an extension of our own enterprise. These suppliers are expected to follow the same standards as ABB with respect to fair and legal labor conditions, occupational health and safety, environmental responsibility and business ethics. These standards are defined in the ABB Supplier Code of Conduct.
The ABB Supplier Sustainability Development Program (SSDP) helps suppliers to live up to our Supplier Code of Conduct by raising awareness, helping them to comply with sustainability principles and incentivizing them to improve performance continuously. The program also builds our capacity to ensure that appropriate assistance can be provided to suppliers. Together, this moves us towards our goal to provide our customers with a competitive and sustainable supply chain.
We prioritize suppliers to participate in the program according to a risk matrix, which includes criticality of the supplier, country risk, commodity risk based on operations characteristics, and spend volume. The selected suppliers receive training about ABB’s global requirements regarding sustainability standards and on practical ways to improve their performance. We then conduct sustainability assessments at the suppliers’ premises to identify remaining gaps, and help suppliers to develop improvement plans. After that we assess the timely implementation of these plans. Read more about the program on our website.
Strengthening processes
In 2013, we worked to strengthen support for our suppliers. The Supplier Code of Conduct was updated to provide more specific requirements around material compliance and procurement practices by our suppliers, as well as a new section to describe the channels through which suppliers can report any misconduct by ABB. We also released a detailed Supplier Sustainability Implementation Guide, providing advice on best practices along with country-level information about relevant laws and standards.
Internally, a dashboard of SSDP key performance indicators was developed, implemented and is regularly updated, allowing performance tracking and analysis across business units, divisions and countries in all levels of our organization. This is helping us to identify geographies, businesses or elements of the program that need extra focus or support.
150 supply chain sustainability assessments in 2013
Improving performance
Over the last three years we have trained around 1,800 ABB supply chain and quality experts (408 in 2013) and over 1,800 critical suppliers (630 in 2013). Our internal assessor training program, launched in Mexico in 2012, was extended to China in 2013 where 19 participants achieved third-party certification as supplier sustainability assessors.
Over the course of the year, we conducted 150 supplier sustainability assessments, focusing mainly on Brazil, China, India and Mexico. These assessments, on average, resulted in 14 corrective actions per supplier.
Twelve of the assessments were conducted in the Czech Republic to evaluate ABB’s risk exposure with our main Eastern European suppliers. These assessments, however, did not reveal any critical findings and resulted in an average of only three corrective actions. Based on these encouraging results, the Czech Republic will no longer be in the focus of the SSDP moving forward.
Although supplier training programs are resulting in improved supplier performance, assessments continue to reveal situations where ABB’s standards are not met. The most frequently identified root cause includes lack of knowledge of applicable labor, health, safety and environmental regulations, which can then result in unsafe working conditions, poor environmental practices and excessive overtime. The 10 most frequently identified non-compliance issues are shown in the following table:
Number of ABB employees trained
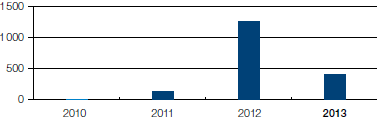
Number of suppliers trained
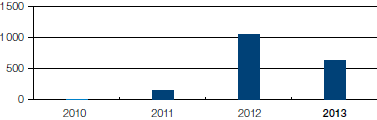
Number of suppliers assessed
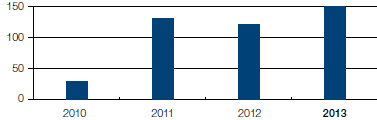
|
|
|
General Management |
|
|
---|---|---|
Labor and human rights |
|
|
Health and safety |
|
|
|
|
|
|
|
|
|
|
|
Environment |
|
|
|
|
|
|
|
|
|
|
|
During the year, 14 suppliers were blocked due to unsatisfactory progress with their corrective action plans. One of the four suppliers blocked during 2012 closed their action plan and was allowed to return as an active supplier, bringing the total number of blocked suppliers to 17. We actively monitor global ABB spend with blocked suppliers to ensure that their blocked status is respected across divisions and geographies.
ABB supply chain staff also visited suppliers to our recently-acquired companies. At one location, two cases of child labor were detected. Remedial action was taken immediately and no evidence of child labor was found during subsequent unannounced visits.
In addition to the SSDP, ABB’s global sustainability network conducts environmental audits of suppliers, as part of our own facilities’ ISO 14001 management systems. More than 1,100 documented environmental audits of suppliers were performed during 2013. Overall, 50 percent of more than 2,000 key suppliers are externally certified to ISO 14001 and a further 13 percent have implemented “self-declared” environmental management systems.
Challenges and different approaches
Now that the SSDP has been running and evolving for several years, we took the opportunity to review it during 2013 to see what lessons we have learned and what we could further improve.
From an internal perspective, we realized that the program is most effective in countries where there is strong local ownership of training, assessment and continual improvement processes and communication, rather than a strong reliance on the corporate offices. Therefore, we have taken action to strengthen and empower local supply chain sustainability teams, to formalize common Group standards and processes that can be applied at local level and to provide common tools to assist in tracking program performance locally. Training programs have been diversified and customized, depending on needs.
We are also aware that some of the issues that surface during supplier assessments cannot simply be fixed by supplier training and improving management processes; they require real partnership between ABB and our suppliers to understand the root causes and it can take time to develop lasting solutions.
One such issue is excessive overtime. We have found that some suppliers consider extended working hours to be normal business practice, a necessity to meet production deadlines. In certain regions, suppliers’ employees often rely on overtime pay as a necessary supplement to their normal wages and will move to another employer if their total working hours are reduced.
Through close work with our suppliers, we have found that redesign of work processes and workforce deployment can result in greater process efficiency, improved labor productivity and better allocation of skilled labor, improving business performance and reducing overtime requirements. For example, suppliers in India and Mexico have found that looking at their businesses with fresh eyes can change mindsets and help them to a safer, more equitable and more profitable future. Read more in our case study.
We are now focusing on preventive actions: engaging and training suppliers on this topic, communicating about the benefits of effective overtime control and also sharing supplier success stories.
Moving forward in 2014
The SSDP will continue to expand and develop in 2014. New focus countries, South Africa and Malaysia, will be added to the program, and we will also put a special focus on contractor safety development in Saudi Arabia. The internal SSDP assessor certification program, already operating in Mexico and China, will be launched in Brazil, India and South Africa. Communication of successes and challenges will increase and supplier support materials will be translated into local languages.
Our Supplier Sustainability Development Program is helping us to embed sustainability principles along our value chain. The results are encouraging, with many of our suppliers finding real business benefits in the program while improving their sustainability performance. However, new challenges arise and we will continue work on addressing them.