Promoting responsibility along the value chain
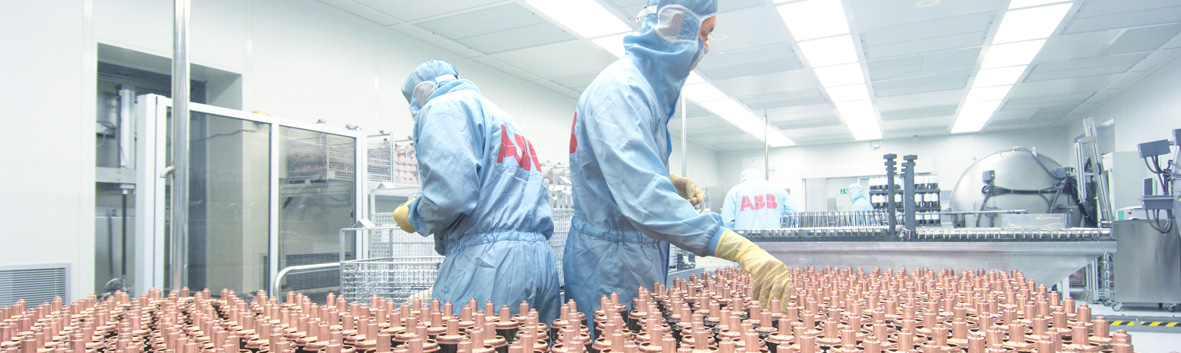
ABB is committed to minimizing our environmental impacts and to ensuring the health, safety and protection of people who come into contact with our products and business. This requires attention to product design and manufacturing processes, as well to our supply chain, to ensure that the materials and components we use and the products we produce comply with our own and our stakeholders’ standards.
Improvement by design
When it comes to product and technology development in any part of the ABB Group, we use a process we call the ABB Gate Model. This decision model defines a series of gates, or decision points, to determine whether or not the project should continue. The intention is to ensure appropriate consideration of all aspects needed to satisfy the project’s defined objectives. These include consideration of legal, technical, strategic, manufacturing, customer and other requirements.
Sustainability aspects are built into the Gate Model and include a standardized Life Cycle Assessment (LCA) procedure and a handbook to guide consideration of environmental, and health and safety aspects during design. These aspects include how to:
- reduce the use of hazardous substances,
- assure compliance with relevant laws and regulations,
- avoid environmental and health risks during product manufacturing and operation,
- minimize consumption of resources,
- design for recycling and easy end-of-life treatment.
We have developed support materials such as checklists and training packages for our research technologists to improve understanding and ensure sustainability aspects are incorporated into design.
In 2013, ABB’s Corporate Research Center (CRC) in Sweden decided to take this a step further and established an award for “Green Project of the Year”. The award was established to increase awareness at the CRC of the breadth of environmental aspects that technologists can influence through product and process design and elicited entries covering a wide range of technologies. Read more in our case study.
11% reduction in Volatile Organic Compounds (VOC) emissions in 2013
LCA is not only required as part of a product’s research and development phase, it is also used in the concept development phase for next generation products. ABB develops Environmental Product Declarations to communicate the environmental performance of our core products over their life cycle. Declarations are based on LCA studies, created according to the international standard ISO/TR 14025. More than 80 declarations for major product lines are published on our website.
Reduction of hazardous substances
ABB continues to phase out hazardous substances in products and processes, where technically and economically feasible. We have compiled lists of prohibited and restricted substances to guide this process and update them regularly, in line with international regulations. These lists help our engineers, our suppliers and other partners like OEMs to comply with regulatory requirements, ensure a high level of protection for human health and the environment, and manage risks encountered by chemicals present in various products.
Download XLS (17 kB) |
|
2013 |
a |
2012 |
b |
2011 |
c | ||||||
---|---|---|---|---|---|---|---|---|---|---|---|---|
|
||||||||||||
Phthalates – softener for PVC |
21 |
|
28 |
|
47 |
|
||||||
PBB and PBDE – flame retardants |
2.9 |
|
~0 |
|
~0 |
|
||||||
Lead in submarine cables |
7,236 |
|
5,633 |
|
5,725 |
|
||||||
Organic lead in polymers |
0.6 |
|
0.9 |
|
1.3 |
|
||||||
Lead in other products, e.g. backup batteries and counterweights in robots |
2,601 |
|
363 |
|
227 |
|
||||||
Cadmium in industrial batteries delivered to customers |
4.4 |
|
5.6 |
|
1.6 |
|
||||||
Cadmium in rechargeable batteries |
67.6 |
|
6.3 |
|
10 |
|
||||||
Cadmium in lead alloy and other uses |
5.7 |
|
4.5 |
|
4.3 |
|
||||||
Mercury in products delivered to customers |
0.012 |
|
0.011 |
|
0.030 |
|
||||||
SF6 insulation gas (inflow to ABB) |
1,438 |
|
1,139 |
|
1,052 |
|
||||||
SF6 insulation gas (outflow from ABB) |
1,425 |
|
1,118 |
|
1,040 |
|
Emissions of volatile organic compounds (tons)
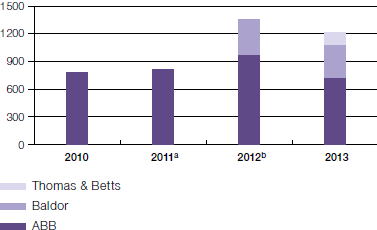
a Baldor facilities not included
b Baldor facilities included; Thomas & Betts not included
Our suppliers are requested to comply with these regulations, which are also part of ABB’s Global Terms and Conditions and Supplier Code of Conduct. We have developed a Guide for Suppliers to the ABB List of Prohibited and Restricted Substances to support our suppliers to understand and implement the ABB List and to provide guidance on our suppliers’ obligations.
ABB facilities are required to ensure compliance with the ABB List and to work to phase out hazardous substances in their processes and products. These programs are showing results, with significant reductions in the use of substances such as phthalates, used as a softener in PVC, and almost complete elimination of organic lead in polymers. Other activities are targeting, for example, elimination of solder containing lead and the substitution of various chemicals used in metal cleaning processes.
With the integration of our recent acquisitions, Baldor Electric Company and Thomas & Betts, we are seeing changes in the profiles of hazardous substances used on sites and in products due to different processes and product ranges. In particular, we have seen an increase in lead and cadmium in batteries delivered to customers and in polybrominated flame retardants used in polymers. We are working together to ensure implementation of the ABB List and to develop improvement programs.
Alongside plant-specific schemes, global Business Unit (BU) focus programs continue. The most extensive of these programs is an initiative to reduce Volatile Organic Compounds (VOCs) in the Transformers BU of our Power Products division. The goal of the initiative is to reduce the solvent emissions from painting across the complete manufacturing spectrum of the BU.
The program involves 62 factories in 27 countries and targets the reduction of VOC emissions by almost 300 tons, equivalent to the yearly VOC emission of 25,000 cars. Besides reducing emissions, this program has helped standardize paint operations and improve paint quality – benefits for our customers, our business and the environment. Read more in our case study.
Promoting material compliance
Stricter legal frameworks have been put in place worldwide, which means ABB is required to monitor the source of certain minerals more closely, as well as to phase out the use of hazardous substances in our products and processes.
ABB is aware of and concerned by the conflicts occurring in the Democratic Republic of the Congo. We are actively working to identify which products and material from suppliers may contain conflict minerals and are engaging with our customers regarding their disclosure obligations.
Like many other companies tracing conflict minerals, it will take time for a company of our size and complexity to collect the information needed for us to fully understand our use of conflict minerals and therefore be able to address related customer concerns.