Energy efficiency, renewable energy and climate
Working on many fronts to reduce climate impacts
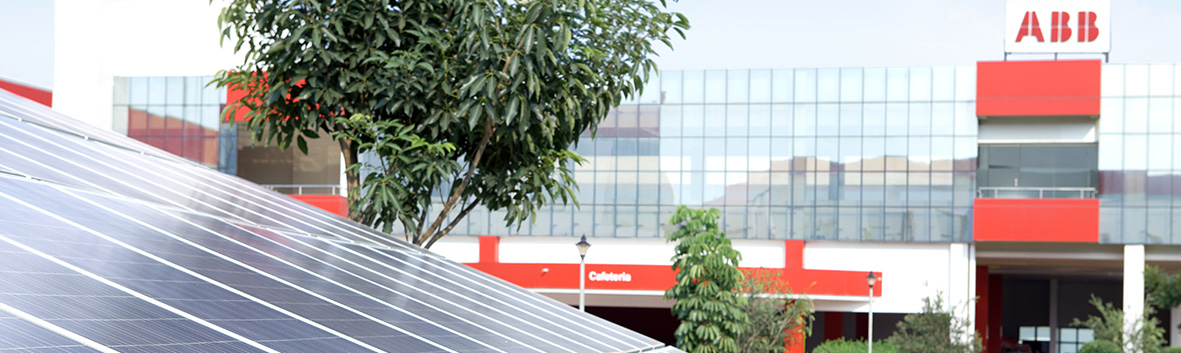
ABB’s greatest contribution to the reduction of greenhouse gas (GHG) emissions is through our energy efficient and renewable energy products, systems and services. But we also work hard to improve the energy-efficiency and reduce the carbon-intensity of our own operations.
Internally, we have set a target to reduce ABB’s energy intensity by 20 percent by 2020, from a 2013 baseline. This includes direct fuel consumption, as well as the use of electricity and district heating for manufacturing processes and to operate buildings. We also aim to cut GHG emissions from direct use of fuels, from purchased electricity and district heating, and from the handling of sulfur hexafluoride gas (SF6).
To support our goals, all ABB manufacturing, workshop and office facilities are required to implement energy savings plans, and to assess the main sources of GHG emissions and develop action plans to cut them. Improvement activities across the Group include conducting feasibility studies, modifying processes, updating equipment and infrastructure, working with suppliers, and changing behaviors.
While our efforts in 2015 resulted in absolute decreases in both GHG emissions and energy consumption, ABB’s energy intensity, measured as MWh per million US dollar sales, increased due to lower 2015 revenues and lower capacity utilization in some areas.
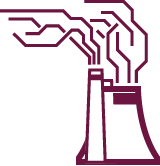
Energy efficiency in operations
During 2015, more than 190 individual energy efficiency projects were reported across the Group, estimated to result in 32.2 GWh of energy savings for the year. Many of these projects addressed the efficiency of compressed air systems and of heating, ventilation and cooling (HVAC) processes, while others focused on improving the energy efficiency of our buildings and heat recuperation from machines and processes.
As in previous years, the most common projects involved implementation of energy-efficient lighting solutions, generally in our production and testing facilities. Solutions involved increased use of daylighting, replacement of old lighting with LED technology, as well as application of lighting control systems.
To this end, we are using some of the lighting improvement projects to test new lighting concepts developed as part of our ongoing collaboration with Philips. Initiated in 2014, the collaboration aims to combine the companies’ expertise in building automation and LED technology to develop innovative, scalable lighting solutions for production and logistic halls, and warehouses.
For example, ABB and Philips developed a new lighting system for an ABB production facility in Turgi, Switzerland to provide better illumination of the production hall while significantly cutting electricity consumption and maintenance requirements. The project involved replacement of metal halide lamps with LED modules and installation of detection sensors and a control system that automatically adapts lighting levels to available daylight and usage requirements in the hall. We estimate the new lighting concept has reduced the annual electricity costs – and associated CO2 emissions – of the production hall by 50 percent. At the same time, the employees benefit from the improved brightness of the system, which greatly improves visual clarity for fine installation work.
Other facilities have undertaken comprehensive reviews of processes and infrastructure and are realizing significant energy savings. For example, our medium-voltage products plant in Nashik, India upgraded its lighting system, installed more efficient HVAC technologies, modified the fume extraction system to avoid continuous running, and developed new standby programs for energy-intensive processes. The facility also invested in new technology to control conditions in its cleanroom, reducing the related electricity consumption by more than 50 percent and eliminating 54,000 liters of diesel consumption. The efficiency projects are projected to save more than 1,200 MWh per year, approximately one-quarter of the energy consumed at the site in 2015.
Energy savings are also being realized as side benefits in other projects. At our robotics operation in Västerås, Sweden, a program designed to improve water filtration and cleaning in degreasing processes also resulted in a 75 percent reduction in energy used to heat the cleaning water. At our factory in Roigheim, Germany, changing a raw material to improve product quality also allowed the facility to save around 220 MWh during manufacturing processes.
Many facilities have also chosen to implement formal energy management systems (EnMS), with 48 of the 89 sites with an EnMS now externally certified to ISO 50001 or EN 16247. ABB in Spain has implemented a unified EnMS for six main manufacturing and service sites, representing more than 95 percent of ABB’s total energy consumption in the country, and achieved certification in early 2015. Each site sets annual targets based on its unique circumstances, with the goal to achieve a 20 percent reduction in country-wide energy intensity by 2020. The country is well on track to its target having reduced energy intensity (MWh/million Euro) by almost 15 percent between 2013 and 2015.
Total energy use and energy intensity
Download graph as XLS (21 kB) | Download graph as PNG (44 kB)
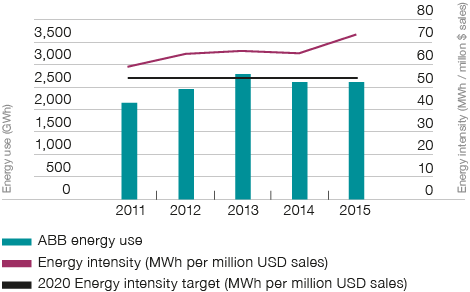
During 2015, ABB recorded a small year-on-year decline in absolute energy consumption, bringing total reduction since 2013 to 6.8 percent. Reductions in oil, diesel, district heat and electricity consumption were mostly offset by an increase in gas consumption, partially driven by fuel switching away from heating oil. Softer market conditions impacted activity levels and efficiency, partially offsetting the gains from energy efficiency programs. Energy intensity of global operations increased by 11.8 percent year-on-year (10 percent increase on the 2013 baseline) mainly due to the decline in 2015 revenues.
Energy use by type for 2015 (2014)
Download graph as XLS (22 kB) | Download graph as PNG (32 kB)
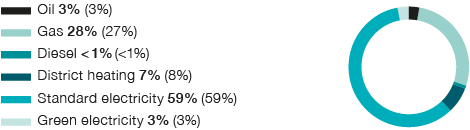
Building an efficient real estate portfolio
With a portfolio of around 8.8 million square meters of building space worldwide, ABB’s corporate real estate management also plays a key role in our energy efficiency performance. The ABB Green Building Policy, introduced in 2008, sets out criteria for all new buildings, including site selection, building design and the choice of materials to optimize resources. It also details policies required for new development, refurbishment, and selection and management of rented space.
The development of the new ABB country headquarters in France, located outside Paris, fully demonstrated this approach, combining energy efficiency with comfort and flexibility for the occupants. The 7,000 square meter office building was converted from a factory and is now equipped with a building management system that ensures the control of heating, air conditioning, ventilation, blinds and lighting. The system, equipped with ABB solutions, not only complies with the requirements of ISO 50001, but allows environmental control in individual offices as well as open spaces. Energy savings of 25 percent have been achieved since the site’s opening in July 2014.
As a further step to improve the sustainability of our buildings, ABB has implemented a focused corporate real estate energy efficiency program across Europe. Kicked off in 2013, the project now covers 90 sites in 14 countries and entails systematic energy monitoring, technical assessments and evaluation of efficiency measures. Assessments have now been completed at 55 sites and reports on efficiency measures completed for 31 of those sites. We intend to expand this energy efficiency approach globally.
Building on the experience gained from the Energy Efficiency Europe program, we have recently launched the ABB Energy Management System for Real Estate (ABB EnMS). The ABB EnMS is a modular system designed to improve energy efficiency within ABB’s global real estate portfolio and provide a step-wise approach to achieving ISO 50001 compliance. The system is applicable globally but provides the flexibility to cater to local needs and objectives. Read our Case study for more details
Reducing carbon intensity of energy
As well as working to improve the efficiency of our energy consumption, ABB also seeks to reduce the carbon intensity of our energy sources. In 2015, ABB in France decided to purchase all of its electricity from renewable sources, joining ABB operations in Belgium, Netherlands and United Kingdom in a commitment to “green” electricity. Thomas & Betts plants in these countries will also join these programs as their current contracts expire. In Sweden, almost 20 percent of electricity purchased was “green” energy. Globally, 4.4 percent, or 71 GWh, of ABB’s 2015 electricity was purchased as certified “green” electricity.
During 2015, we surveyed 15 of our large country operations to better understand the opportunities for and potential barriers to procurement of renewable electricity in different regions and to learn from those already doing so. Preliminary results indicate potential cost-effective opportunities, which we will further investigate during 2016.
ABB facilities have also installed on-site photovoltaic (PV) power plants to reduce environmental impacts, as well as to demonstrate ABB’s solar capabilities. PV plants are now installed at 25 sites in 15 countries across Asia-Pacific, Latin America and Europe, with further installations in planning or construction phase. While contributing only a small proportion of our global electricity needs, these plants are often a key part of local energy strategies, reminding employees of ABB’s energy efficiency and low carbon commitments.
Greenhouse gas emissions
ABB’s total greenhouse gas (GHG) emissions (direct + indirect) decreased by 8.8 percent in 2015, from 1.81 million tons in 2014 to 1.65 million tons, mainly due to a significant reduction in SF6 emissions from production processes and gas handling on site. During 2015, we analyzed and redesigned certain production processes to reduce and, where possible, eliminate SF6 use. Other facilities continued their programs to improve handling, leak detection and storage procedures for the gas.
Indirect GHG emissions from purchased energy declined slightly due to decreased consumption, while indirect GHG emissions from air travel declined by more than 8 percent due to reduced travel. (See Approach to reporting section for details of our GHG calculation methodology.)
Reduction in air travel has been facilitated to some extent by the greater availability and quality of virtual meeting solutions that support collaboration within ABB and with external partners. ABB has transferred approximately 125,000 employees to Office 365 to provide a common enterprise-wide foundation for business communication. Integrated voice and video desktop solutions are being rolled out to all employees over time to improve productivity, generate savings and reduce environmental impacts.
Total greenhouse gas (GHG) emissions and GHG intensity
Download graph as XLS (22 kB) | Download graph as PNG (43 kB)
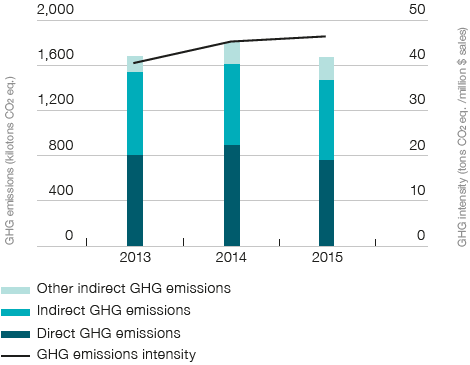
Transport, logistics and packaging
During 2015, we worked to develop a better Group-level view of our global fleet and related GHG emissions. We also learned from local good practices in low-carbon fleet and travel policies, such as the Green Fleet policy of ABB in Switzerland, which incentivizes staff to select lower CO2 emission vehicles. Additionally, staff members who choose not to take a parking space for their private car receive a payment of CHF 400 in the form of “Reka Checks” which can be used to pay for train travel. We will continue this work in 2016, sharing best practices and developing a more detailed estimate of fleet GHG emissions.
Programs to optimize logistics continued during 2015, resulting in cost savings, improved quality and reduced emissions. Following a successful pilot in China, the Transportation Management Center (TMC) concept will be rolled out globally during the next three years. TMCs provide coordinated transport management for ABB business units, integrating domestic and international transportation needs, coordinating vendor, transport management center and factory through a unified operational process. The goal is to include up to 90 percent of ABB’s freight in the program to increase efficiency.
Our global packaging optimization project also continues to make progress. The project focuses on cargo packaging, sourcing and supply base reduction and involves systematic review of packaging needs and assessment of the potential to optimize packaging type, size and weight. As well as sustainable cost reductions, improved packaging and loading can increase transport efficiency, thus reducing emissions and material consumption, improving ergonomics and providing better product protection.
Optimization programs have also been initiated at business unit (BU) level. For example, our BU Transformer factories in Lodz, Poland and Ludvika in Sweden have cooperated to develop a “round tour truck” project that has significantly reduced the number of trips from Lodz to Ludvika and identified an efficient use for the return trips. This concept has now been extended to include returnable packaging. Reusable boxes have been designed with dimensions standardized according to product designs and to fully utilize space in the trucks. Each box can be used 30-60 times, replacing single-use wooden boxes.