Safe and secure operations
Embedded in our culture
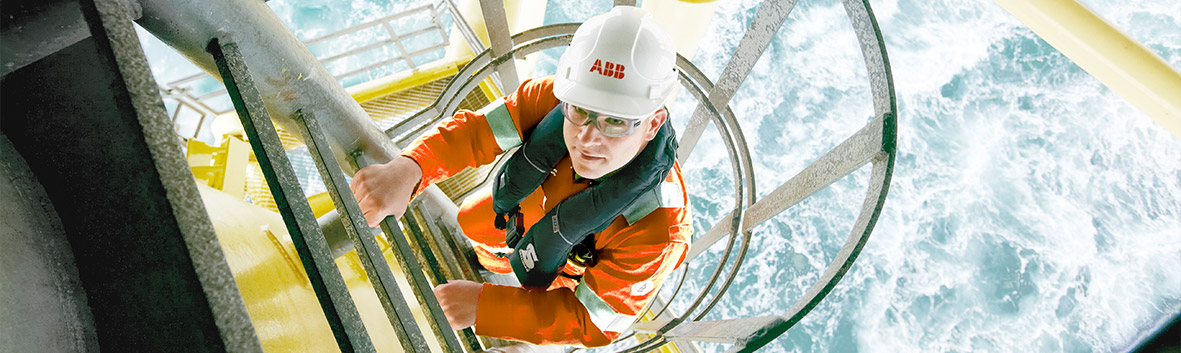
Safety, along with integrity, is one of ABB’s core value pairs and, as such, determines the way we work. It influences the type of business we accept, the personal responsibilities expected of each employee, and the way we manage people and interact with our colleagues.
Our objective is that by 2020 all ABB operations will have an excellent health, safety and security culture embedded in their day-to-day business, targeting zero incidents.
To achieve this ambition, we have established targeted, Group-wide initiatives to supplement our long-standing safety program. These initiatives are underpinned by key performance indicators (KPIs) with quantitative targets that are tracked and reported regularly to top management.
The KPIs – rate of safety observation tours (SOTs) conducted, rate of hazard reporting, percentage of operations covered by certified health and safety management systems – were deliberately selected as “leading” indicators, with the goal to identify and eliminate hazards before they cause harm or injury. We continue to monitor the outcome of our programs – our safety performance – using “lagging” indicators, such as total recordable incident rates.
Consistent message from the top
ABB’s Next Level strategy explicitly defines responsibilities at all levels of the organization, with accountability for safety assigned along business lines. These responsibilities and accountabilities clearly link business value with the ability to deliver safely and with integrity - prerequisites to achieving our ambitious growth targets.
To reinforce this link, the “hazard reporting rate” KPI has now been included in ABB’s internal dashboard that is used to monitor business performance across the Group. The performance improvement of each division and business unit is reviewed annually, according to a defined scoring system, and outcomes are factored into managers’ variable compensation.
Additionally, all ABB employees must include a health and safety behavioral goal in their annual objectives. To support consistency and rigor, we have developed a package of defined objectives with appropriate underlying metrics that can be selected according to the individual and their role, responsibilities and seniority.
Our CEO continued to reinforce the Group safety message with the presentation of the inaugural CEO Safety Awards at the Group Leadership Forum in 2015. The awards, open to all ABB employees around the world, acknowledge significant individual and team achievements that promote a strong safety culture.
From more than 150 nominations, winners and runners-up were selected in each of three categories. Catherine King, Health, Safety and Environment (HSE) Manager at ABB in Australia was named winner of the Safety Leader award for demonstrating exceptional HSE leadership in the workplace. The ABB team responsible for the Al-Rayyan Village substation project in Qatar won the Project Safety Performance award, while the Team Safety Improvement award went to the ABB Shanghai Motors Co. Ltd. for major progress in HSE workplace improvement. Read our Case study for more details
Following the success of ABB’s first global Safety Week in 2014, Safety Week 2015 more than doubled the number of training sessions delivered globally (5,600 compared to 2,500 in 2014), and also expanded its reach from 140,000 participants to 186,000 in 2015. Training sessions included three main topics - key safety risks, safe ways of working, and working safely with contractors - while additional trainings were prepared according to locally identified needs, such as office ergonomics, use of defibrillators, first aid training, health awareness and stress management, among many others.
Programs and tools supporting our strategy
To support the achievement of our safety objectives, we prioritized three work areas during 2015: development of safety master-classes for line management, strengthening of safety instructions and standards, and development of enhanced internal HSE audit arrangements.
The safety master-classes are leadership and HSE competence workshops for line managers, designed to extend their HSE knowledge and leadership skills, and helping them to apply impactful leadership practices in their daily work. The workshops will train managers to identify hazards and manage risks, to identify the roles and responsibilities required to achieve a culture of excellence in HSE and to influence behaviors to achieve these outcomes. The workshop format and content were developed in 2015, with pilots and initial roll-out to plant, local business unit (BU) and product group managers planned for 2016.
We also conducted a global review of our safety instructions and standards, to create a high profile, common base for improved alignment, and as the common base for a comprehensive audit program to drive compliance and continuous improvement in HSE. Additionally we have developed and implemented a new Lessons Learned process, underpinned by an assurance procedure that requires review, gap analysis and action by each local BU manager. This process helps ensure critical lessons are shared across all our operations, with line managers accountable for full application of required actions. A further tool and process to help businesses share good practices across the Group was also launched during the year.
To strengthen HSE governance and reinforce line management accountability, we developed an HSE audit protocol to be applied in the Group internal audit program, trained all internal auditors and conducted audits in all regions and in all divisions. During 2016, we plan to expand the scope and application of the audit program. This new program will facilitate peer to peer auditing to promote sharing and learning across operations, identification of improvement opportunities and standardization of HSE processes across ABB to best practice level.
Occupational hygiene
The impact of an infectious disease in the workplace can be significant, even when few employees are affected. ABB takes action to protect our employees from such occurrences and has developed a Sanitary Threat Tool and Pandemic Guidebooks designed to give our operations the tools to cope with fast-moving incidents of infectious disease, such as MERS-CoV, Ebola or Zika virus. The guidebooks contain generic corporate action plans applicable to most commonly occurring infectious diseases in ABB’s areas of operations, and ensure local adaptation to meet legal and medical requirements and best practice. The tools were rolled out to all ABB country and region crisis task forces during 2015.
Our health and safety performance
We saw significant improvement in many of our key safety metrics in 2015, but sadly we recorded two fatal incidents involving ABB contractors working at project sites in India and Saudi Arabia.
Ensuring safe ways of working with contractors is an ongoing challenge, which we are addressing at many different levels: in our supplier qualification and classification processes, in our contractor management and safety leadership training and through project safety audits.
In other areas, we are already seeing the benefits of our increased focus on safety performance. We have seen a significant reduction in severity of incidents, as measured by the days lost rate, while the employee total recordable incident rate declined by 10 percent from 2014 and has improved by more than 30 percent since 2011.
We also made good progress towards the 2020 targets for our leading indicators. The rate of hazard reporting exceeded the 2020 target of 2 per employee, while the Safety Observation Tour rate showed the target of 1.2 per employee is within reach. Certified health and safety management systems are in place at 421 of our 602 reporting locations (70 percent), providing an excellent platform from which to work towards our 95 percent 2020 target. Progress on this target will be pursued following the release of the new ISO 45001 occupational health and safety management system standard and following a review of our current strategy.
Injuries, lost days, diseases and fatalities
Download XLS (26 kB) |
|
2015 |
2014 |
2013 |
a |
2012 |
b |
2011 | ||||||||||||||||
---|---|---|---|---|---|---|---|---|---|---|---|---|---|---|---|---|---|---|---|---|---|---|---|
|
|||||||||||||||||||||||
Employee work-related fatalitiesc |
0 |
1 |
0 |
|
1 |
|
0 |
||||||||||||||||
Incident rated |
0.00 |
0.01 |
0.00 |
|
0.01 |
|
0.00 |
||||||||||||||||
Employee business travel fatalitiesc,f |
0 |
0 |
0 |
|
1 |
|
0 |
||||||||||||||||
Incident rated |
0.00 |
0.00 |
0.00 |
|
0.01 |
|
0.00 |
||||||||||||||||
Contractor work-related fatalitiesc,e |
2 |
2 |
7 |
|
2 |
|
0 |
||||||||||||||||
Contractor business travel fatalitiesc,f |
0 |
0 |
0 |
|
0 |
|
0 |
||||||||||||||||
Members of the public fatalitiesc |
1 |
0 |
1 |
|
0 |
|
0 |
||||||||||||||||
Employee total recordable incident numbere,g |
1,310 |
1,500 |
1,664 |
|
1,750 |
|
1,505 |
||||||||||||||||
Incident rated |
8.79 |
9.95 |
10.94 |
|
13.04 |
|
13.17 |
||||||||||||||||
Contractor total recordable incident numbere,g |
343 |
333 |
310 |
|
348 |
|
307 |
||||||||||||||||
Incident rated |
8.02 |
7.76 |
7.52 |
|
8.21 |
|
7.47 |
||||||||||||||||
Employee lost time incident numbere |
531 |
652 |
686 |
|
683 |
|
722 |
||||||||||||||||
Incident rated |
3.55 |
4.34 |
4.70 |
|
4.80 |
|
5.70 |
||||||||||||||||
Contractor lost time incident numbere |
163 |
200 |
158 |
|
159 |
|
148 |
||||||||||||||||
Incident rated |
3.81 |
4.65 |
3.83 |
|
3.76 |
|
3.60 |
||||||||||||||||
Employee lost days due to industrial incidentsh |
7,831 |
8,415 |
10,591 |
|
10,345 |
|
9,478 |
||||||||||||||||
Days lost rated |
52.56 |
55.22 |
77.50 |
|
74.64 |
|
69.56 |
||||||||||||||||
Employee occupational health diseases |
46 |
17 |
10 |
|
10 |
|
7 |
||||||||||||||||
Employee occupational health disease rated |
0.31 |
0.11 |
0.14 |
|
0.07 |
|
0.06 |
||||||||||||||||
SOT numbere |
139,124 |
|
|
|
|
|
|
||||||||||||||||
SOT rate |
0.92 |
|
|
|
|
|
|
||||||||||||||||
Hazard numbere |
520,942 |
|
|
|
|
|
|
||||||||||||||||
Hazard rate |
3.51 |
|
|
|
|
|
|
Secure operations
ABB has strengthened its security capability in recent years to better protect our people and assets, and to ensure business resilience.
In common with many global enterprises, we face a series of threats, ranging from terrorism, crime and kidnapping through to natural disasters and cyber security. Whereas in the past the likelihood of threats could be mapped relatively easily or was likely to be confined to high-risk areas, this is no longer the case.
The terror attacks in Paris in 2015, as well as violent incidents and social unrest in the Middle East, North Africa and other parts of Africa underline that a company increasingly has to factor in security into its policies, processes, project planning and costs.
Mapping the movement of ABB travelers - there may be several thousand people on the move at any one time - is vital. Our security personnel need to be able to warn staff members away from certain areas at short notice, to stop travel, to evacuate or advise a lockdown in the event of an incident. For this reason, significant progress has been made on online tools to advise and track the movement of our employees and contractors. Travelers who have booked their journeys through our preferred travel agents can be located and accounted for at short notice, and be kept informed about rapidly changing events.
Training on different aspects of security is vital to our ability to exercise our duty of care. We have ongoing training programs at Group, region and country levels to help our employees to understand how to act and react under exceptional circumstances.
The face-to-face training sessions in 2015, led by internal corporate security staff, focused on country management crisis training (22 conducted), physical and personal security, travel and project security, workplace violence, extortion awareness and family liaison in which selected employees are briefed on how to approach and work with the family members of victims of violence. In many cases, training is tailored to perceived threats in a region: There are countries where workplace violence is perceived as a more likely occurrence; in other areas, the threat of kidnap for ransom or extortion are seen as a greater risk.
All these training sessions are supported by online learning. The most frequently used online tools in 2015 were those focusing on travel security, project security and crisis management.
While it is not advisable to go into detail about security challenges that ABB was confronted with in 2015, we demonstrated our ability to proactively prepare for risk and manage difficult situations in different parts of the world. We helped to safeguard our people, protect our assets and meet our customers’ needs - but we know the need for such efforts is likely to increase in the future.