Responsible sourcing
Standardized processes, building relationships
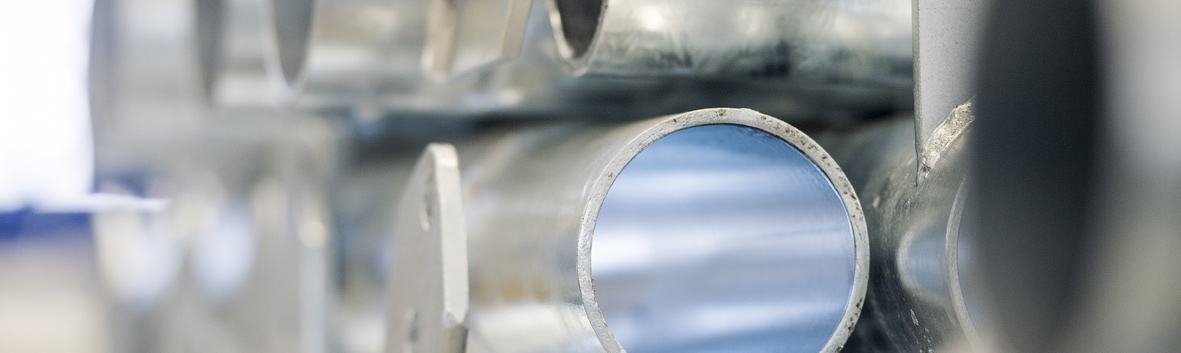
ABB is committed to improving its supply base. Our strategy is geared towards building relationships with best-in-class suppliers in the areas of sustainability, business ethics, quality, on-time delivery and total cost, ensuring compliance with ABB standards and continuous sustainable improvement.
With operations in approximately 100 countries, ABB manufactures products in over 300 product lines and has approximately 70,000 direct material and project service suppliers. We view these suppliers as an extension of our global enterprise and an integral component of our long-term success.
ABB is, therefore, committed to providing skilled resources to support our suppliers’ development and enable them to achieve a sustainable competitive advantage. Together, this moves us towards our goal to provide our customers with a competitive and sustainable supply chain.
ABB takes a structured approach to supplier qualification, performance evaluation, classification and development. Our process to register and pre-qualify new suppliers is operated through our partner Achilles, while supplier performance evaluation is conducted in-house, covering quality, delivery, commercial, sustainability and risk management topics. The results of these evaluations drive supplier development processes.
Strengthening processes
To support ABB’s strategy to build strategic relationships with the best-performing suppliers, we developed and launched new, common supplier qualification and classification processes during 2015. These processes are mandatory for all suppliers of direct material or project services where annual ABB spend is above $5,000. The new procedures are now being implemented step-wise, with initial focus on medium and high risk suppliers.
The supplier qualification process ensures that a supplier has the ‘basics’ in place and satisfies ABB minimum requirements. The new process is designed to reduce risks, improve supplier on-time delivery, quality performance and compliance, and enable sharing of qualification activities across different parts of ABB’s business.
An initial company risk evaluation, covering sustainability, compliance, quality, supply chain and financial risks, determines the required steps in the qualification process, with a higher risk rating leading to more stringent qualification steps. All suppliers now must be certified according to ISO 9001 or a similar quality management standard and suppliers of materials or services classified as high HSE risk are strongly recommended to be certified to ISO 14001 and OHSAS 18001 for environmental and health and safety management.
The new qualification process ensures consistency when ABB defines and implements standards, such as our Supplier Code of Conduct and conflict minerals requirements. It will strengthen relationships with our key suppliers as we work with them to achieve this.
The supplier classification process takes into account the supplier’s qualification status, compliance status, actual performance and overall strategic fit. It enables ABB to clearly identify the suppliers best aligned to our sourcing strategies and standards, and channel spend to those classified as ‘Preferred’ and ‘Approved.’
Implementation of the new processes has also been supported by the launch of the MyABB Supplier portal, a new self-service, single entry point for suppliers to access relevant information, tools and training materials across ABB applications. The portal offers greater flexibility in the training process, providing 24/7 access to materials and helping suppliers identify and prioritize applicable training.
Developing supplier sustainability performance
In early 2015, ABB presented the GF foundry in Leipzig, Germany with the Global ABB Supplier Sustainability Award to honor the supplier’s commitment to health and safety, social responsibility and efficient use of energy. With multiple units supplying ABB, GF - based in Switzerland - has adopted robust and effective practices and represents a model to which all ABB suppliers can aspire. Read our Case study for more details
ABB initiated the Global Supplier Sustainability Award to recognize sustainability leaders in our supply chain and will continue to identify award candidates using our supplier qualification, development and performance data.
ABB’s Supplier Sustainability Development Program (SSDP) helps us to focus our efforts further to support improvement in the sustainability performance of our suppliers. The program prioritizes suppliers according to a risk matrix combining country risk, commodity risk based on operations characteristics, criticality of the supplier and spend volume. Training on sustainability priorities is provided for both suppliers and ABB employees, on-site assessments evaluate performance status, and improvement plans are monitored to ensure timely completion. We focus on tier one suppliers in priority countries, mainly Brazil, China, India, Mexico and South Africa.
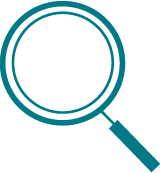
Expanding activities in 2015
During 2015, we launched the SSDP assessment program in Indonesia, Thailand and Vietnam and expanded the SSDP to Poland with training sessions and on-site assessments. The ABB internal assessor program continued, with additional supply chain specialists in Brazil, China and India obtaining third-party certification.
We also enhanced support material for the program during 2015 with the launch of SSDP e-learning courses for suppliers and providing local translations of SSDP training material for Indonesia, Poland, Thailand and Vietnam. E-learnings on responsible sourcing and the SSDP were also developed for ABB employees during the year, while training on root cause analysis and action plan preparation was conducted for ABB teams.
The following table summarizes SSDP activities during 2015 and achievements since the start of the program.
Supplier Sustainability Development Program
Download XLS (23 kB) |
|
2015 |
2010-2015 |
|
||||
|
|||||||
Number of ABB employees trained |
259 |
1.634 |
a |
||||
Number of suppliers trained |
421 |
3,222 |
a |
||||
Number of suppliers assessedb |
179 |
777 |
a |
||||
Number of risks identified |
441 |
1,523 |
|
||||
Number of risks mitigated |
311 |
986 |
|
After on-site assessments, suppliers are assigned a risk rating based on the assessment findings. The risk rating determines the required pace of corrective action and whether an on-site reassessment is required for the closure of corrective actions. The 10 most frequent non-compliance issues identified during assessments are shown in the table below. ABB uses this information to further develop the program and associated support processes.
While we see significant performance improvement through implementation of corrective action plans, we continue to assess how well suppliers maintain those improvements. In 2015 we revisited 22 suppliers who had successfully closed all corrective actions from previous assessments. As in 2014, we discovered some repeat findings, and are assisting those suppliers with root cause analysis to prevent recurrence.
Top 10 sustainability non-compliance issues
|
|
General management |
|
Labor and human rights |
|
Health and safety |
|
Environment |
|
Addressing challenging issues
As we have reported previously, some of the issues identified during supplier assessments require analysis to understand the root causes and it can take time to develop lasting solutions. One such issue is excessive working hours, which is often categorized as a social compliance issue, but is at the core, a business and financial issue.
Working with a peer company and external consultant, in 2015 we developed the ABB Training and Development Program for Factory Working Hours, a detailed training program that enables factories to conduct root cause analysis, and to define and implement changes that result in positive business value, not simply working hours compliance. The program was piloted with 15 suppliers during 2015, with outcomes to be evaluated in early 2016. Read our Case study for more details
While ABB focuses on working with suppliers to improve performance, there are consequences for suppliers unwilling to align their performance standards with ABB requirements. During 2015, 20 suppliers were blocked due to unsatisfactory progress on their corrective action plans, bringing the total number of blocked suppliers to 43.
Moving forward in 2016
We will continue to scale up and replicate the SSDP in 2016, with plans to roll out the program in Argentina, Colombia, Peru and Turkey. Training for suppliers will be further enhanced with the development of new training materials and an increased number of trainings.
Once the updated supplier qualification and classification system is fully implemented in 2016, we will review the supplier base selected for inclusion in the SSDP and aim to develop new quantitative targets for the program.