Resource efficiency
Improving processes, saving costs
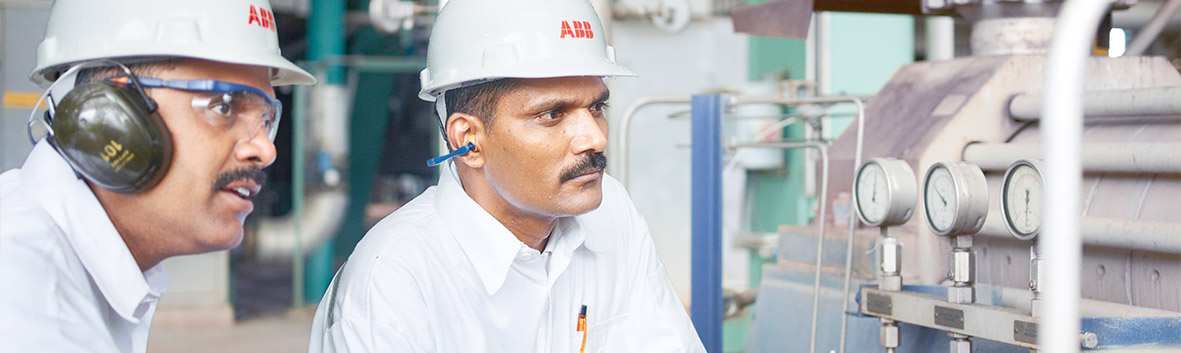
ABB is committed to minimizing our environmental impacts and to ensuring the health, safety and protection of people who come into contact with our products and business. This requires attention to product design and manufacturing processes, as well as to our supply chain, to optimize the use of resources, minimize waste and ensure that the materials and components we use and the products we produce comply with our own and our stakeholders’ standards.
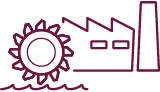
Addressing these issues contributes to our business success by reducing costs and risks, improving the work environment for our employees and helping to maintain our license to operate.
Reducing impact where it’s most needed
Given the impacts of water stress are felt most acutely locally, ABB is focusing our water conservation efforts in locations where the water stress is highest. We have committed to reduce absolute water use by 25 percent between 2013 and 2020 at facilities in watersheds with extremely high, high and medium-high baseline water stress.
We have mapped our facilities using the World Business Council for Sustainable Development’s Global Water Tool and classified them according to the level of “baseline water stress” of the watershed where they are located. Baseline water stress measures total annual water withdrawals (municipal, industrial, and agricultural) expressed as a percent of the total annual available flow. Higher stress values indicate more competition among users. Data on watershed water stress are based on work by the World Resources Institute1.
Of the 470 facilities mapped2, 57 are located in watersheds with extremely high water stress, 96 in areas with high stress and 76 in areas with medium to high stress. Even though approximately 50 percent of our facilities and employee headcount are located in these high water stress areas, the facilities accounted for only 33 percent of ABB’s global water withdrawal in 2015.
We have selected 64 of these sites as the initial focus of our water reduction commitment. Selection was based on 2014 facility water withdrawal greater than 5,000 m3 in extremely high and high stress watersheds (32 and 29 sites, respectively) and water withdrawal greater than 50,000 m3 in medium-high stress watersheds (3 sites). These facilities, in 23 countries, accounted for 79 percent of ABB’s water withdrawal in extremely high, high and medium-high stress watersheds and for 26 percent of ABB’s global water withdrawal in 2015.
Many of the selected facilities have already initiated activities to reduce their water withdrawals and improve their water efficiency. Some have redesigned processes to treat, recycle and reuse water, while others have made significant investments in new systems to reduce water consumption.
For example, our measurement products facility in Ossuccio, Italy, uses significant amounts of water to cool production machinery. The cooling system, designed originally as a continuous-flow, open-loop system taking water from the municipal water system and returning it to a small creek adjacent to the facility, has now been upgraded to a fully-closed process, saving both water and costs. The new system was commissioned in 2015, saving more than 35,000 m3 (more than 30 percent) in 2015 water withdrawal compared with 2014. Read our Case study for more details
1 Gassert, F., M. Landis, M. Luck, P. Reig, and T. Shiao. 2014. “Aqueduct Global Maps 2.1.” Working Paper. Washington, DC: World Resources Institute.
2 We did not include facilities with fewer than 20 employees on site.
Water in our global operations
Across ABB Group, water withdrawals were reduced by 4 percent (430,000 m3) during 2015, including a 5 percent reduction in water purchased from municipalities and a 14 percent reduction in surface water extraction. Water discharge also declined by almost 4 percent, mostly due to reduction in discharge to surface and ground water.
Site-level water efficiency projects ranged from repair and refurbishment of water systems, to upgrading processes to enable increased recycling or reuse of water, to collection of rain water for use in process work or domestic facilities. Water conservation training and awareness-raising programs continued for employees at many facilities.
Sources of water withdrawals in 2015 (2014)
Download graph as XLS (21 kB) | Download graph as PNG (37 kB)
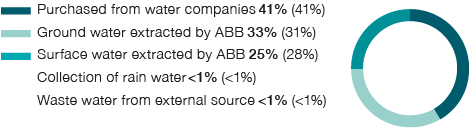
Water withdrawals in 2015 per water stress status
Download graph as XLS (22 kB) | Download graph as PNG (31 kB)
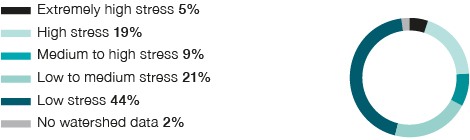
In Ludvika, Sweden, installing flow control valves and rebuilding the pipes to vapor phase ovens is helping to reduce the consumption of cooling water, as well as saving electrical energy from reduced pumping requirements. At nearby Västerås, a project to achieve more efficient filtration of water used in degreasing processes is expected to dramatically increase the number of cycles the water can be reused, resulting in a 75 percent reduction in water use.
In 2015, almost 50 percent of ABB’s water withdrawals were used for cooling processes, 20 percent for manufacturing processes and the remainder for domestic purposes such as sanitation, cooking or garden maintenance.
Of those sites that use water for process purposes, more than 30 percent use closed-loop systems. Excluding cooling water returned to the source of extraction, the use of closed-loop processes and the reuse of water in other ways saved approximately 5,200 kilotons (5.2 million m3) of water in 2015. Without this recycling and reuse, ABB’s water withdrawals would have been 54 percent higher.
Some 51 percent of our water discharge was to public sewers, with about 30 percent of that volume first processed at our own treatment plants. Another 42 percent was discharged to surface or ground water, with 90 percent of that volume pre-treated. The remainder was handled by hazardous waste water treatment companies.
Water withdrawals and water reused / recycled (kilotons)
Download graph as XLS (21 kB) | Download graph as PNG (24 kB)
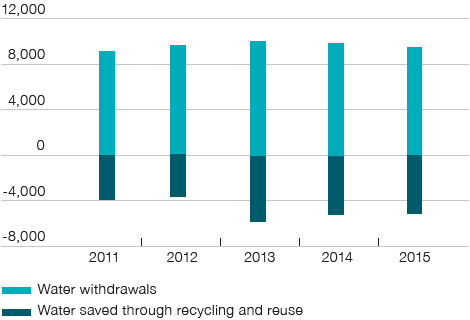
Waste and recycling
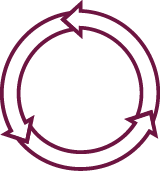
of waste sent for recycling in 2015
ABB products contain mostly steel, copper, aluminum, oil and plastics. Consequently, the main waste streams at ABB facilities are metal, oil and plastic, as well as wood and cardboard from packaging materials and paper from office activities.
The majority of the material used in our products is reclaimable at the end of the product’s life, and we aim to enhance the ability to recycle by designing products that can be dismantled more easily and by providing users with recycling instructions.
At our sites, we aim to optimize material use, reduce the amount of waste generated and increase the share of waste that is reused or recycled. We are committed to reduce the amount of waste sent to final disposal – both hazardous and non-hazardous – by 20 percent by 2020. This will be measured as the proportion of total waste sent for final disposal and compared with a 2013 baseline.
During 2015, the total generation of waste was essentially unchanged from 2014, while the proportion of waste sent to final disposal improved slightly from 21 percent in 2014 to 20 percent in 2015.
To support this objective, all sites are required to develop plans to increase the share of waste reused or recycled and to reduce the amount of waste sent for final disposal in absolute terms.
In total, we generated less than 16,000 tons of hazardous waste in 2015, 12 percent less than in 2014, and sent about one-third of that amount for recycling rather than disposal. In-house recycling, mainly of packaging materials and thermoplastics, reduced the amount of waste by more than 5,700 tons, an improvement of 17 percent from 2014.
ABB operations undertake a wide range of waste reduction and recycling initiatives that reduce environmental impacts as well bringing cost benefits for the business. The type of activities undertaken generally depends on the characteristics of the production processes and the local waste infrastructure, but common themes emerge.
As a first step, many locations focus on awareness building and on ensuring that processes are designed to support material efficiency and waste sorting for improved recycling. Process improvements have included changing purchasing practices to encourage the supply of goods in bulk containers, thus reducing packaging waste, and reusing transport crates and pallets or repurposing the wood. At the New Berlin facility in the US, wooden pallets are now recycled by a third party, with the wood used for commercial mulch or as sawdust and the metals separated for scrap recycling. This action is estimated to save the facility approximately $100,000 per year in disposal costs.
Some facilities are working with waste management vendors to optimize recycling options, such as the San Luis Potosí site in Mexico, where improved waste separation processes enabled the sale of certain waste streams, totaling almost $160,000 for the year. In the US, some sites have negotiated agreements with their waste vendors to manage the waste streams, facilitating a significant reduction in landfill disposal.
Other sites have reviewed processes and procedures in order to minimize waste generation. For example in China and in Spain, facilities have reduced resin waste by changing control processes to enhance resin quality and reduce resin utilization rate. Staff training and sensitization has further improved performance. In ABB’s high-voltage products factory in Ludvika, Sweden, the zinc spray-coating process was redesigned and optimized, resulting not only in significant savings of raw material from reduced wastage, but also a cleaner and healthier work environment due to dust reduction.
Even though there are many activities under way at our sites around the world, we are not yet seeing sufficient progress at Group level. Consequently, in 2016 all sites will be required to analyze their sources of waste and identify areas where generation of waste can be reduced. At Group level, we will systematically review the current state of waste reduction and recycling efforts, identify common elements, document best practices, and develop clear guidelines on required and recommended practices.
Waste and recycling
Download graph as XLS (22 kB) | Download graph as PNG (55 kB)
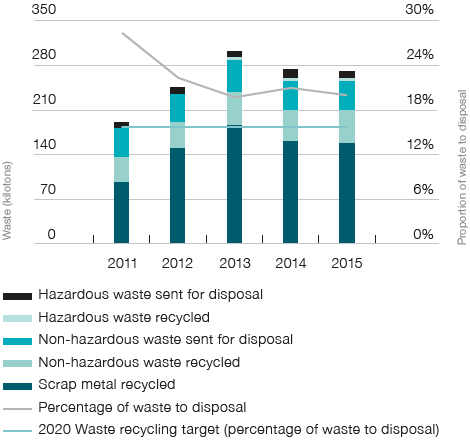
Improvement by design
ABB’s Research and Development (R&D) engineers and scientists are key to ensuring that our environmental and health and safety ambitions are designed into ABB’s products and solutions.
ABB’s Group-wide approach to product and technology development follows the ABB Gate Model which defines a series of gates, or decision points, to determine the progress of projects. The intention is to ensure appropriate consideration of legal, technical, strategic, manufacturing, customer and other requirements.
Sustainability aspects are built into the Gate Model and include a standardized Life Cycle Assessment (LCA) procedure and a handbook to guide consideration of environmental, and health and safety aspects during design. These aspects include how to:
- reduce the use of hazardous substances
- assure compliance with relevant laws and regulations
- avoid environmental and health risks during product manufacturing and operation
- minimize consumption of resources
- design for recycling and easy end-of-life treatment
We have developed support materials such as a health, safety and environment checklist (HSE Checklist) and training packages for our research technologists to improve understanding and ensure sustainability aspects are incorporated into design.
During 2015, we updated material selection guidelines and the HSE Checklist to strengthen “design for environment” principles and to include practical tools to facilitate the process. We trained a further 139 engineers and technologists, both in corporate research centers and in business units, to use the checklist and guidelines, and also established a sustainability network for our global research centers to share good practices and achievements related to ABB’s sustainability objectives.
As part of our external collaborations, we also consulted with the scientific community and peer companies in 2015 to improve internal processes related to the Gate Model and to ensure that the content of the HSE Checklist remains consistent with current science.
Reduction of hazardous substances
ABB continues to phase out hazardous substances in products and processes, where technically and economically feasible. We have compiled lists of prohibited and restricted substances to guide this process and update them regularly, in line with international regulations. These lists help our engineers and suppliers to comply with regulatory requirements, ensure a high level of protection for human health and the environment, and manage risks encountered by chemicals present in various products.
Our suppliers are requested to comply with these regulations, which are also part of ABB’s Global Terms and Conditions and Supplier Code of Conduct. We have developed a Guide for Suppliers to the ABB List of Prohibited and Restricted Substances to support suppliers’ understanding of their obligations.
The ABB list of prohibited and restricted substances is updated regularly, in line with regulations in our main markets. ABB facilities are required to ensure compliance with the ABB list and to work to phase out hazardous substances in their processes and products.
Use of hazardous substances (tons)
Download XLS (23 kB) |
|
2015 |
2014 |
2013 |
2012 |
2011 |
---|---|---|---|---|---|
Phthalates – softener for PVC |
878 |
258 |
21 |
28 |
47 |
PBB and PBDE – flame retardants |
0 |
1.9 |
2.9 |
~0 |
~0 |
Lead in submarine cables |
8,376 |
7,842 |
7,236 |
5,633 |
5,725 |
Organic lead in polymers |
1.4 |
0.1 |
0.6 |
0.9 |
1.3 |
Lead in other products, eg, backup batteries and counterweights in robots |
1,684 |
1,884 |
2,601 |
363 |
227 |
Cadmium in industrial batteries delivered to customers |
0.8 |
4.4 |
4.4 |
5.6 |
1.6 |
Cadmium in rechargeable batteries |
97.5 |
75.1 |
67.6 |
6.3 |
10 |
Cadmium in lead alloy and other uses |
6.4 |
6.0 |
5.7 |
4.5 |
4.3 |
Mercury in products delivered to customers |
0.007 |
0.071 |
0.012 |
0.011 |
0.030 |
SF6 insulation gas (inflow to ABB) |
1,658 |
1,483 |
1,438 |
1,139 |
1,052 |
SF6 insulation gas (outflow from ABB) |
1,648 |
1,466 |
1,425 |
1,118 |
1,040 |
Emissions of volatile organic compounds (tons)
Download graph as XLS (21 kB) | Download graph as PNG (24 kB)
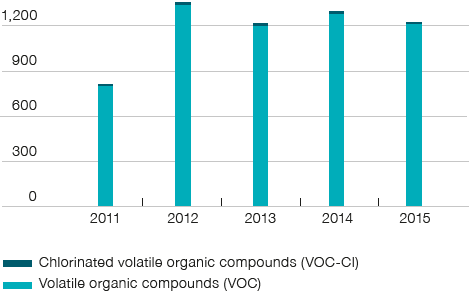
As we continue to integrate our recent, large acquisitions, Baldor and Thomas & Betts, we continue to review the processes and substances used at these sites and to improve the quality of reporting, especially of complex mixtures and polymers. In 2015, a further two facilities reported on the use of phthalates, which are used as plasticizers in polymers, leading to a significant increase in reported use. Alternatives to these substances are under active investigation.
Good progress has been made to eliminate the use of polybrominated flame retardants in polymers. For example, at our plant in Scarborough, Canada, polybrominated diphenyl ether (PBDE)-containing bobbin material has been replaced with non-PBDE material, not only reducing the hazardous substances at the facility, but cutting costs by more than $10,000 per year.
Emissions of chlorinated volatile organic compounds were reduced by one-third during 2015, as facilities continued to phase-out the use of chlorinated solvents.
Other facilities have continued to move to lead-free solder, have eliminated the use of rinsing solvent or have found alternatives to certain epoxies or flooring materials. ABB in Poland has taken a country-wide approach to enable better monitoring and systematic management of hazardous substances.
Promoting material compliance
ABB’s network of environmental specialists works alongside our product development and supply chain function to promote material compliance. During 2015, we reinforced our continuing work around REACH compliance through the delivery of 13 training sessions on different aspects of the regulation to our cross-functional, REACH network.
During 2016, we will work to increase this collaboration between supply chain, environment and R&D staff to continue to strengthen our organizational capability as REACH and other regulatory requirements expand.
As well as targeting the phase-out of hazardous substances in our products and processes, ABB has also initiated programs to monitor the source of certain minerals more closely.
Currently, there is a conflict in the Democratic Republic of Congo where armed groups are being funded through the sale of tin, tungsten, tantalum, and gold (“conflict minerals” or “3TG”) from mines which they control. We are actively working to identify whether any of the conflict minerals contained in our products have been obtained from the mines supporting armed groups.
In 2015, we provided our second report, covering 2014, regarding conflict minerals in our products to the United States Securities and Exchange Commission according to the requirements of section 1502 of the Dodd-Frank Wall Street Reform and Consumer Protection Act.
We continue to assess our product portfolio to identify the use of tin, tungsten, tantalum or gold in our products and utilize ABB product experts, including representatives from supply chain management, engineering, and research and development, in making these product portfolio assessments.
To assess whether the necessary conflict minerals in our products originated from the Democratic Republic of Congo or any of its nine bordering countries, we performed a “reasonable country of origin inquiry” (RCOI) in line with the internationally recognized due diligence framework set forth in the Organisation for Economic Cooperation and Development Due Diligence Guidance for Responsible Supply Chains of Minerals from Conflict-Affected and High-Risk Areas and identified direct suppliers of products likely to contain 3TG .We then surveyed these suppliers using the Conflict Minerals Reporting Template as developed and issued by the Electronic Industry Citizenship Coalition — Global eSustainability Initiative (EICC/GeSI).
In 2015, we expanded the number of suppliers covered by our RCOI procedures. We also increased our efforts to identify the specific components within each of our products. This enabled us to refocus our supplier selection procedures based on the results of the detailed analysis of our product components. Conclusions from this work will be included in ABB’s next report on conflict minerals to the Securities and Exchange Commission, due later in 2016. This, and earlier reports can be found at this link.
ABB’s work on responsible sourcing has been recognized by two independent benchmarking studies, showing that our efforts are focused in the right direction. We will continue collaborating with external initiatives and will continue to work over time to expand the level of awareness along our supply chain and to improve the information that is available.