Responsible sourcing Ensuring sustainable supply chains
ABB’s procurement processes help minimize social and environmental impacts
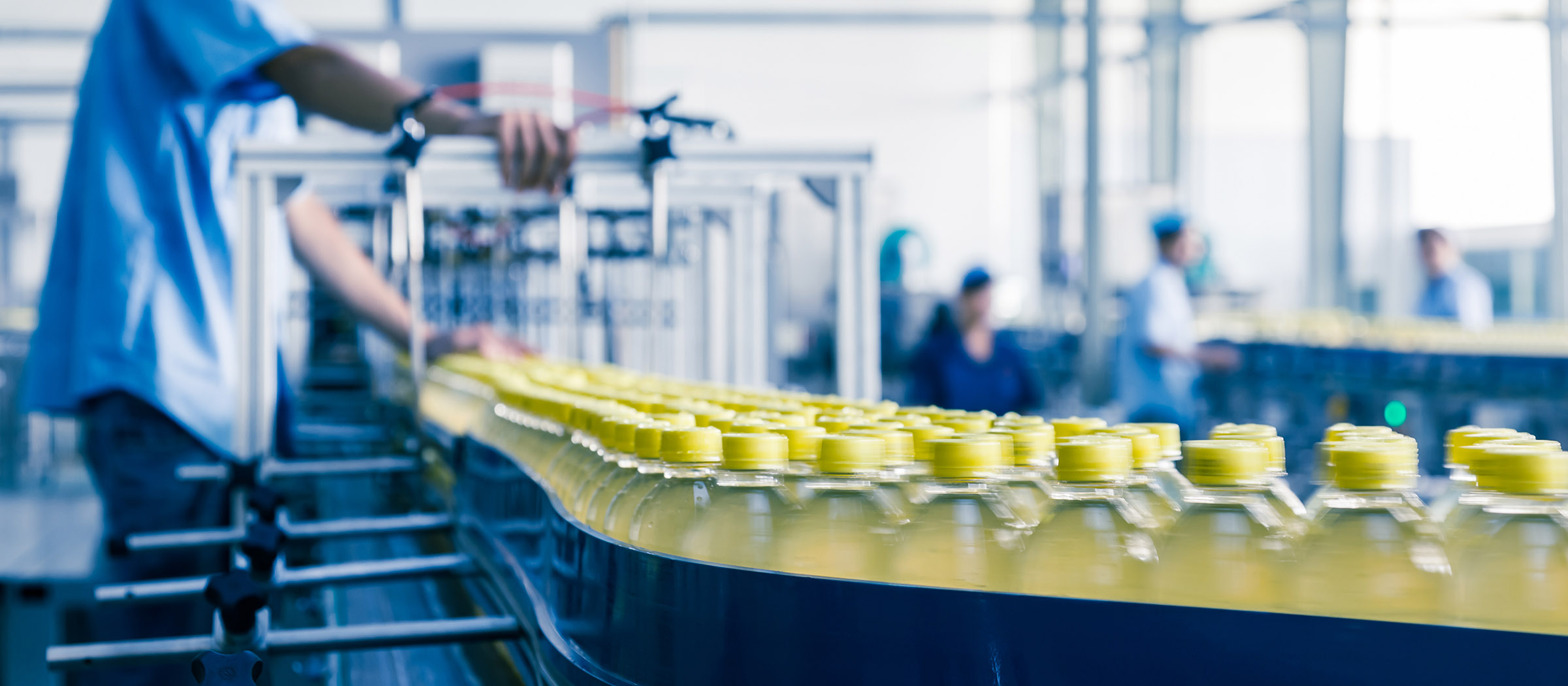
ABB is committed to improving the sustainability of our supply base. The ABB Supplier Code of Conduct (SCoC), which is published in 16 languages, lays out the standards that we require of our existing and potential business partners. The SCoC forms part of our suppliers’ contractual obligations, highlighting expectations with regard to areas such as human rights, fair labor conditions, business ethics, health & safety and environment & material compliance, as part of ABB’s general terms and conditions.
To further enhance responsible sourcing, we continue to deploy the ABB Supplier Sustainability Development Program (SSDP), which proactively screens and prioritizes (using a combination of geographical, category and economic factors) sustainability risks posed by suppliers, evaluates their adherence to the SCoC and engages them when necessary. The SSDP includes supplier trainings and onsite assessments on 42 parameters related to general management, labor rights, social benefits, health and safety and environment.
To address sustainability in our procurement activities, ABB assesses hundreds of suppliers on their sustainability practices and provides training on improvement actions. This engagement helps ABB to strengthen our supply base and gives our customers confidence in the sustainability of their extended supply chain.
Timo Ihamuotila – Chief Financial Officer
For every area of non-compliance identified by our supplier assessments, we launch a supplier support action to systematically address each issue in turn. Our support actions include capacity building, customized participatory workshops, sharing best practices, jointly implemented collaborative programs and the transfer of knowledge and expertise. We have found this proactive approach results in better supplier responses and improved performance standards.
Every year, ABB trains, coaches and assesses hundreds of suppliers on their sustainability practices. This is a continuous process, in which old risks are closed and new ones are identified each year. The time required to close a sustainability risk can range from one month to over a year, depending on its complexity. Since 2015, we have identified an average of 723 new risks each year. Due to the ongoing identification of new risks and the time required to mitigate them, our closure rate for identified risks can never be 100 percent.
Our 2020 target is to close 65 percent or more of identified risks from supplier assessments. In 2019, ABB continued to exceed this target, closing 78 percent of identified risks in 2019, up from 76 percent in 2018. We achieved this strong result thanks to our focused program management, continued engagement with our suppliers, onsite support, pre-assessment training and focused workshops for our suppliers.
Top ten sustainability non-conformance issues in 20191
|
|||
General management |
|
||
Labor and human rights |
|
||
Health and safety |
|
||
Environment |
|
While ABB believes in working with suppliers to improve their performance, there are consequences for suppliers who are unwilling to align their performance standards with our requirements. During 2019, ABB terminated business with three suppliers due to unsatisfactory progress on their respective corrective action plans.
In 2019, we analyzed supplier assessments conducted from 2014 to 2018 and found the most frequent major non-conformance issues observed were unsafe working practices, lack of environmental management system compliance, no health & safety risk analysis and no environmental risk analysis. To address these shortcomings, we continued to raise awareness through initiatives such as our specially designed workshops on health, safety, environmental and labor requirements of the SSDP.
Among other key initiatives in 2019, we designed and implemented multiple workshops in China on various sustainability compliance concerns that were identified during supplier assessment. More such workshops will be organized in other countries in 2020. We also continued our collaboration with suppliers to find solutions for some of the chronic challenges they face regarding working conditions. On the technical side, we supported suppliers with operational data analysis and visits to their factories to identify potential areas for intervention.
In 2019, we assessed 168 suppliers, identifying 574 risks. We mitigated 562 risks during this period. In other activities to support responsible sourcing, we trained 245 ABB employees and 195 suppliers during the year.2
Case study Implementing sustainable process improvements
Reveal case studyABB has been working with an important supplier in China to initiate a cross-functional project to reduce excess overtime. Together, we analyzed their full production cycle – from order receipt to dispatch – to identify major areas of concern. Among other issues, we noted a workforce skills gap, the unbalanced allocation of resources, machine breakdowns and the taking of unexpected sick leave.
This detailed analysis enabled the supplier to take targeted action to improve productivity and establish key performance indicators (KPIs). ABB teams worked together with the supplier to track these KPIs and realign actions where needed. In addition, process improvements were implemented for both the supplier’s machinery and their production lines.
This collaborative effort brought about process changes, increased focus on waste reduction and put in place very strict control procedures. As a result, the supplier was able to reduce excess overtime by more than 20 percent and decreased in-process inventory on a particular production line by 20 percent. Productivity of the line was improved by 23 percent.
Close case study2 Risk is defined as the danger posed to ABB by the non-compliant operations of the supplier. Risk level is assigned as extremely high, high, medium or low, depending upon the severity of instances of supplier non-compliance identified during onsite audits. To reflect the degree of severity of the supplier’s non-compliance, we multiply the total number of instances of extremely high risk by a factor of 5, the total number of instances of high risk by a factor of 3, the total number of instances of medium risk by a factor of 1, and the total number of instances of low risk by a factor of 0. The total risk identified is the sum of the weighted risks assigned to each supplier who has completed an on-site assessment and has outstanding corrective actions. Satisfactory completion of corrective actions by a supplier results in an increase in risks mitigated.