Striving to reduce energy use and climate impacts
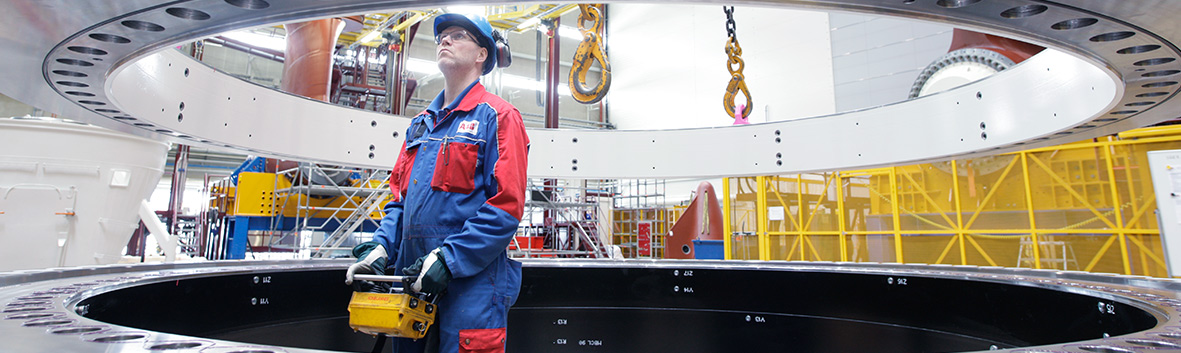
ABB’s mission is to help our customers to use electrical power efficiently, to increase industrial productivity and to lower environmental impact in a sustainable way. Just as we target mitigation of climate change, and energy and resource efficiency for ABB’s customers through our product and solution portfolio, we have also been working for many years to manage and reduce the impacts of our own operations.
As part of our Group-wide sustainability objective to progressively increase the efficiency of our own operations, we have set ourselves the target to reduce the energy intensity of our business by 20 percent by 2020 from a 2013 baseline. This is measured as megawatt-hours (MWh) of energy per million US dollars of sales and includes both direct fuel consumption and the use of electricity and district heating for manufacturing processes and to operate buildings.
To implement the objective, our most energy-intensive sites were required to undertake energy audits and all sites were required to develop an energy saving program. At our plants and offices, and along our value chain, actions to reduce energy consumption and greenhouse gas emissions take many forms, as reported below.
Energy efficiency in operations
During 2014, we recorded a 1.6 percent improvement in the energy intensity of our operations, resulting in energy consumption of 66.02 MWh per million US dollar sales. Absolute energy consumption declined by 6 percent year on year, driven by reductions in electricity and gas consumption and a significant decrease in district heating. Approximately one-third of the absolute energy reduction was due to business divestments during 2014, which primarily impacted Group electricity and gas consumption.
Total energy use and energy intensity
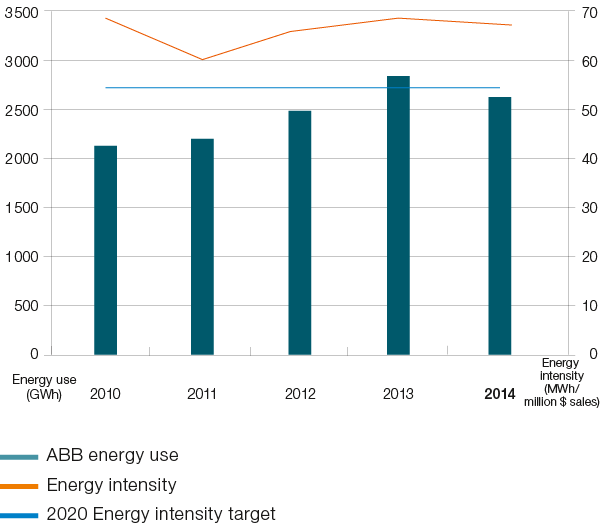
A wide variety of energy savings projects were implemented across the company to achieve our 2014 result. More than 200 individual energy efficiency projects were reported across the Group, estimated to result in 34.4 GWh of energy savings.
Most commonly – and cost effectively – facilities implemented energy-efficient lighting solutions. Other activities included optimizing heating, ventilation and cooling processes, investments in more efficient equipment, investigating and optimizing compressed air systems, behavioral change programs, and implementing or updating heat recuperation from machines and processes, often using our own technology.
Energy use by type for 2014 (2013)
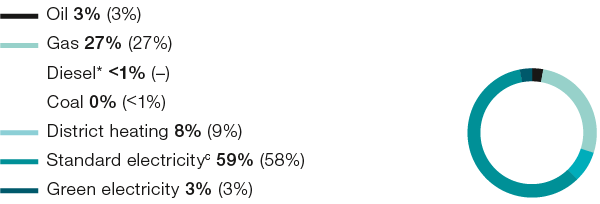
* Diesel consumption reported separately for the first time in 2014. Previously reported with oil consumption.
Some actions were as simple as reducing the temperature of a varnish oven, which not only reduced energy consumption at our facility in Ozark, Arkansas in the US, but also saved over $24,000 during the year.
Other activities were planned as part of multi-year, facility-wide or country-wide programs. For example, our plant at Ludvika in Sweden – one of our top five energy intensive facilities with more than 2,800 employees on-site – undertook a systematic review of energy consumption during 2013. With cross-functional coordination between real estate, environment and production engineering, they began a step-by-step improvement plan that is continuing into 2015.
Measures taken so far include upgrading lighting systems, repairs and upgrades in the compressed air systems, installation of energy metering, introducing timers on drying ovens and significant training for employees. The program is already showing results and is even exceeding expectations in some projects, such as installation of LED lighting and sensors. With further activities planned for 2015, including installation of heat recovery in the painting area, additional energy metering and further lighting upgrades, we expect to see increasing savings in future.
In other areas, ABB businesses are choosing to implement certified ISO 50001 energy management systems (EnMS) to guide their activities. In 2014, ABB in Spain decided to implement a unified EnMS for six of its manufacturing and service centers, while ABB in Egypt implemented an EnMS at its most energy-intensive site, covering three different business units, which will later be extended to other sites in the country. The program in Egypt not only focuses on energy efficiency but also includes investigation of renewable energy generation and alternatives to fossil fuels in transportation equipment.
Building an efficient real estate portfolio
ABB’s corporate real estate management also plays a key role in our energy efficiency performance. Acquisition, development, refurbishment and management activities related to our worldwide portfolio of about 8.8 million square meters of building space are guided by the ABB Green Building Policy.
In refurbishment projects, our real estate managers are expected to consider a range of factors, including energy efficiency and renewable energy opportunities, flexibility of spaces, working conditions for employees plus site-specific factors related to building use. Addressing these factors not only improves the environmental performance of the buildings, but leads to financial savings and greater employee satisfaction.
For example, there was a significant focus on improving overall design and functionality, as well as energy efficiency during the 2014 refurbishment of ABB’s staff restaurant in Dättwil, Switzerland. Installation of skylights and LED lighting provide a bright and friendly atmosphere while reducing electricity consumption by over 11 MWh per year. Heat recovery systems, ABB control technology for heating and ventilation, and upgraded building insulation will improve comfort levels for staff and also save over 200 MWh per year. Rooftop solar panels will produce almost 20 MWh of electricity each year, which can be used in-house or fed back into the grid. Additionally, building materials were chosen to ensure no hazardous indoor emissions and all wood-based materials were selected on the basis of sustainable forest management.
To supplement site by site improvement projects, in 2013 ABB Real Estate kicked off a significant project to systematically introduce real estate energy efficiency programs across Europe. The project covers 100 sites in 14 countries and aims to identify improvement potential according to a common methodology and to initiate measures to reduce energy consumption. By year end, kick off workshops had been conducted in 13 countries, and detailed reports for three countries completed, outlining the results of energy monitoring, technical assessments and evaluation of efficiency measures. As part of the program, a total of 36 locations in eight European countries were integrated into the central Energy Monitoring System. Read more in our Case study
Many of the LED lighting upgrades undertaken at our office and manufacturing facilities during 2014 were part of ABB’s collaboration agreement with Philips. The collaboration aims to provide a solution to simplify the integration of connected lighting systems and building device control for commercial buildings. ABB and Philips are working together to develop a simple, scalable solution to streamline the introduction of this technology in commercial buildings.
Reducing carbon intensity of energy
As well as working to improve the efficiency of our energy consumption, ABB also seeks to reduce the carbon intensity of our energy sources. Several ABB countries – Belgium, Netherlands and United Kingdom – have decided to purchase all of their electricity from renewable sources. Thomas & Betts plants in these countries will also join these programs as their current contracts reach expiration. In Sweden, almost 20 percent of electricity purchased was “green” energy, while globally, more than 4 percent, or 68 GWh, of ABB’s 2014 electricity was purchased as certified “green” electricity.
During 2014, two more ABB facilities in Egypt and Australia installed on-site photovoltaic (PV) power plants to reduce environmental impacts as well as to demonstrate ABB’s solar capabilities. PV plants are now installed at 22 sites in 13 countries across Asia-Pacific, Latin America and Europe. While contributing only a small proportion of our global electricity needs, these plants are often a key part of local energy strategies, designed as a reminder to employees of ABB’s energy efficiency and low carbon commitments.
Greenhouse gas emissions
Despite reductions in gas, district heat and electricity consumption, ABB’s total greenhouse gas (GHG) emissions (direct + indirect) increased by 4 percent in 2014, from 1.87 million tons in 2013 to 1.95 million tons. ABB’s direct GHG emissions are mainly from fuel used in our operations, as well as from SF6 emissions during production processes and gas handling on site. During 2014, our SF6 emissions increased by over 30 percent due to increased production at several units that handle high volumes of the gas and to unsuccessful trials of a new gassing process at one plant. As part of ABB’s energy and climate objective, we are focusing on strengthening local SF6 management plans to improve handling, leak detection and storage procedures.
Total greenhouse gas (GHG) emissions and GHG intensity
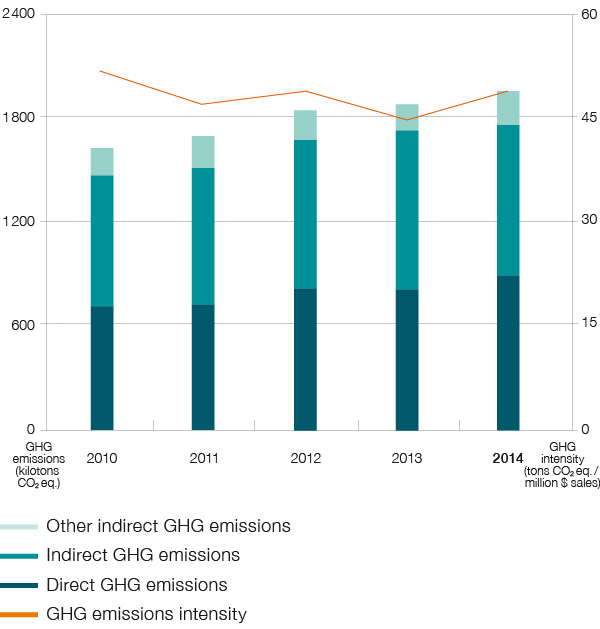
Indirect GHG emissions from purchased energy declined due to decreased consumption, while indirect GHG emissions from air travel increased by 29 percent. This increase was, in large part, due to the first time inclusion of Thomas & Betts travel data and full inclusion of ABB China employees’ air travel. (See Approach to reporting section for details of our GHG calculation methodology.)
Logistics and packaging
Programs to optimize logistics continued during 2014, resulting in cost savings, improved quality and reduced emissions. The Transportation Management Center (TMC) project in China, providing coordinated transport management for all ABB business units around the regions of Xiamen, Beijing and Shanghai, was expanded to include international service during the year. This program is now realizing sustainable logistics cost savings of more than 10 percent.
ABB in India began implementation of a TMC project at one site during 2014, with the intention to cover the remainder of ABB operations in the country and all transport modes by the end of 2015. We will also investigate the feasibility of TMC roll outs in Dubai, Brazil and South Africa in 2015.
200+ energy efficiency projects under way in 2014
Our global packaging optimization project continues to make progress. The project involves systematic review of packaging needs and assessment of the potential to optimize packaging type, size and weight. Improved packaging and loading can increase transport efficiency, thus reducing emissions and material consumption, improving ergonomics and providing better product protection.
More than 80 facilities have systematically reviewed their packaging needs, with 20 sites at implementation stage. Some sites are already seeing the benefits. For example, in Faridabad in India, a change from hand-built rubber wood crates to manufactured plywood improved health and safety, reduced storage space for empty packaging, improved product protection and reduced lifetime CO2 emissions. Similar improvements have been observed in Shanghai, China with a change from rainforest plywood packaging to a lighter, more sturdy solution. At Dalmine in Italy, several projects related to both inbound and outbound transports are under way, and are expected to yield annual savings of well over $300,000. Read more in our Case study