Committed to high standards of integrity
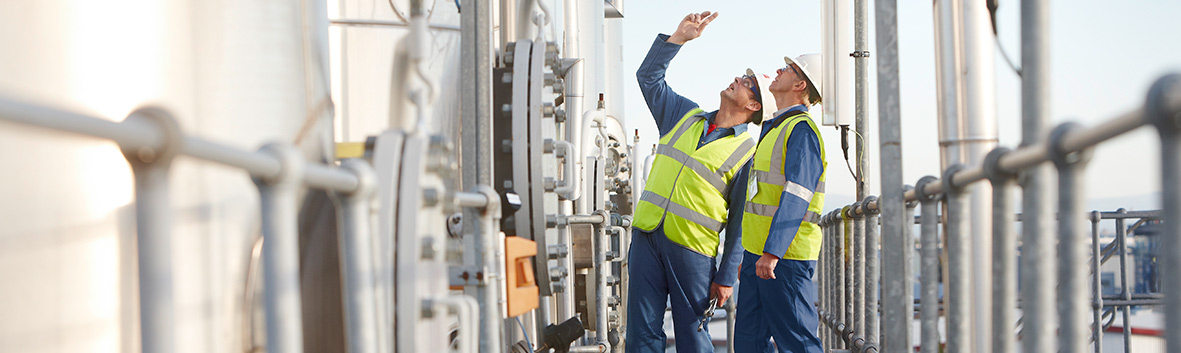
At ABB, performance is measured not only by the results achieved, but also how these results were achieved. A culture of integrity is a prerequisite for a world-class business and ABB’s strength and future success depend on our reputation as a trusted and reliable business partner.
ABB’s Next Level strategy reinforces the importance of integrity as a core value of our organization. We remain firmly committed to our integrity program and the activities to support global communication of the integrity message. Worldwide, ABB operates in over 100 countries, with around 140,000 employees. Managing the complexity of our risk profile requires a dedicated staff and a robust program. Our integrity program is fundamental within the company, and is based on three pillars: Prevention, Detection and Resolution.
Prevention
ABB’s integrity program is based on a clear set of values and unequivocal tone from the top. Commitment to these values is fostered by strong communication from top leadership throughout the organization – not only to our employees but also to our business partners. Our clear position on issues such as improper payments, gifts, entertainment, and expenses, and managing third parties is visible and clear to external parties and sets the right tone from the outset of any negotiation. Our values and expectations are expressed in a publicly available Code of Conduct and a Supplier Code of Conduct, as well as policies and standards.
Training and communications are key to ensuring ABB’s values are received and understood, and this requires constant innovation and follow up. Policies cannot be effective without a commitment from employees to embed rules and standards into every aspect of their work. This can only be achieved through strong messaging that is engaging and practical.
Upon joining the company, every ABB employee must complete two online eLearning programs and one face-to-face training on the ABB Code of Conduct including anti-bribery. In addition, employees in sensitive roles receive specialized online and face-to-face trainings for specific risk areas, for example antitrust. In 2014, over 94,000 employees (nearly 93 percent of all employees with an e-mail address) completed the Global Anti-bribery: Don’t Look the Other Way online training. These messages are then supplemented on at least a bi-annual basis through new e-learning modules, face-to-face training initiatives, and other integrity initiatives such as “Integrity on the LBU (Local Business Unit) Agenda,” and integrity modules in in-house learning and development programs.
Our training efforts are refined over time, according to feedback on risks identified globally and locally. In 2013, we conducted an in-depth Integrity Culture and Risk Survey to understand the success of the integrity program. With responses from over 24,000 participants globally, we have been able to adapt and target the training to specific risk areas identified for ABB employees. Throughout 2014, Country Integrity Officers provided local specialized training and communications on risk-based subjects identified in the survey, including but not limited to respect in the workplace, working with third parties, and self-enrichment/misuse of company resources.
During 2014 we also worked hard to deliver our integrity message in new, positive and collaborative ways. This updated communication and engagement strategy built upon our past successes using cases of consequence and blog posts, but also used new platforms and leveraged the changing IT landscape to attract more attention to our integrity message. Read more in our Case study
Detection
While prevention is important to minimize the incidents of misconduct, we nonetheless need a robust system in place to detect ongoing misconduct. ABB’s internal audit team carries out anti-bribery compliance reviews of business units and countries globally, and conducts an annual risk assessment as the basis for its audit planning for the following year. In these reviews, ABB’s internal auditors review business processes, accounts and balances, and test transactions to assess the robustness of controls and identify possible violations of ABB’s anti-bribery procedures.
Our detection efforts are supported by the availability of multiple reporting channels, including line managers, Human Resources, representatives of the Legal and Integrity function, the Chief Integrity Officer, the Integrity Office at headquarters, the Business Ethics Hotline, or the local ombudsperson. ABB employees are encouraged to use one of the reporting channels whenever they suspect misconduct and whistleblowers are promised protection from any retaliation. The multiple reporting channels are advertised through a hotline poster campaign, this year created using integrity dilemma cartoons, and rolled out worldwide in multiple languages. A stakeholder hotline is available to our external business partners, with details of our reporting channels available on our website.
94,000+ employees trained on anti-bribery principles in 2014
Resolution
All allegations are investigated. The Office of Special Investigations (OSI), part of our Legal and Integrity team, is responsible for conducting internal investigations and consists of 18 professionals located in four different regions globally. Cases that are handled by OSI or by Country Integrity Officers are brought to closure through investigation and remediation, resulting in disciplinary action where appropriate. There is a strict zero tolerance policy for violations of the law or the ABB Code of Conduct.
Cases that are substantiated are often used in our integrity communications activities as a learning experience for the business and for employees, to illustrate our Code of Conduct in action and to demonstrate the consequences of violations.
Engagement and external recognition
ABB’s integrity program has been benchmarked and recognized externally. In 2013, we received the Ethisphere Compliance Leader Verification and Anti-Corruption Program Verification seals based on a review of our integrity program by NYSE Governance Services; we were also recognized as one of the World’s Most Ethical Companies. This was followed in 2014 with a second World’s Most Ethical Companies award.
ABB also supports international efforts at collective action and projects aimed at promoting integrity in the industries where we work and in the public sector. To that end, we are a founding member of the Partnering Against Corruption Initiative, with support from the World Economic Forum. We also became a founding member in 2014 of Ethics and Compliance Switzerland, a professional society whose goals are to promote ethics and integrity in both private and public organizations, as well as to promote sustainable best practices in compliance. This enables ABB to develop and contribute to the overall development of systematic values and integrity in various organizations throughout Switzerland and abroad.
Sustainability governance
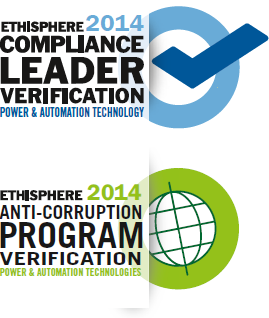
Sustainability principles and considerations are embedded in ABB’s business strategy and guide what we manufacture, how we operate the company and the way we behave towards stakeholders.
Our sustainability strategy is aligned with corporate strategy and is supported by objectives that address ABB’s activities and impacts along the value chain. Progress towards our objectives is driven through all levels of the business, from Executive Committee endorsement, through operational review and target setting in business units and countries to local training and execution at sites, supported by sustainability specialists at Group, country and local level. We rely on every employee to take responsibility to help us achieve our goal: A better world.
Our Sustainability Board, comprising the ABB Executive Committee, oversees sustainability policies and programs, reviews developments and monitors progress towards our targets on an annual basis.
The ABB Sustainability Affairs organization is responsible for the development and coordination of policies and programs covering health and safety, environment, corporate responsibility and security and crisis management. Sustainability Affairs reports directly to Executive Committee member Jean-Christophe Deslarzes.
A network of sustainability specialists worldwide reports to and supports the Sustainability Affairs management team. In countries where ABB entities have or could have significant sustainability impacts, we have appointed country sustainability controllers, country health and safety advisors and country security managers responsible for ABB’s sustainability management program and for gathering the data consolidated in this report. All regions where ABB operates have region health and safety advisors and corporate security managers.
The country and regional specialists are supported by local sustainability officers and health and safety advisors. Overall, the sustainability network is supported by a team of some 950 employees, full-time and part-time, at headquarters and around the world.
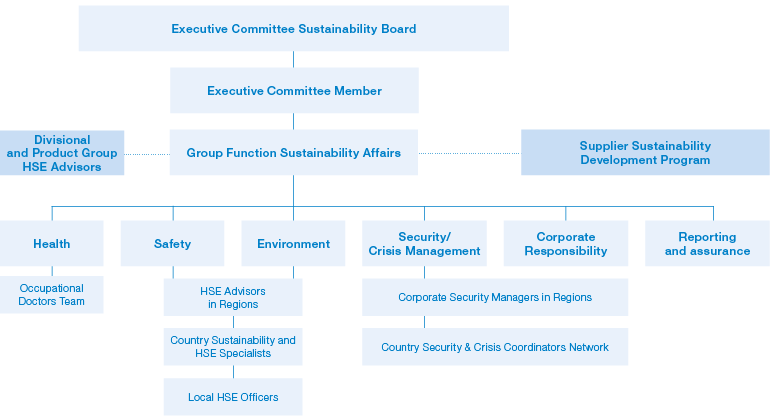
Sustainability policies, principles and external initiatives
We have implemented environmental, social, human rights, and health and safety policies and a Supplier Code of Conduct. These policies include references to the international standards to which they relate.
As a founder member of the United Nations Global Compact, ABB has been closely involved in its development. ABB’s understanding of human rights and day-to-day business benefits from involvement in such organizations. We have also taken note of the UN Guiding Principles on Business and Human Rights and use its recommendations to assess expectations of corporate behavior.
375+ locations certified to ISO 14001 and OHSAS 18001
ABB has adopted ISO 14001 for environmental management systems; ISO/TR 14025 for Environmental Product Declarations; ISO 14040–45 for Life Cycle Assessments; and ISO 19011 for environmental auditing of organizations. We have incorporated the principles of OHSAS 18001, the International Labour Organization (ILO) guidelines on occupational health and safety management systems, and the ILO Code of Practice on Recording and Notification of Occupational Accidents and Diseases into our health and safety program.
All ABB facilities are encouraged to implement management systems for environmental, health and safety and quality issues, while manufacturing and service locations are required to implement such systems. Globally, we have achieved external certification for environmental management systems at 390 sites and offices and for health and safety management systems at 378 locations.
Approach to sustainability reporting
We aim to cover all ABB Group companies in our formal sustainability reporting system, including wholly owned subsidiaries and majority-owned joint ventures worldwide that might have significant sustainability impacts. Power-One, and other entities acquired during 2013, are now integrated into this system. Integration of companies acquired during 2014 is continuing and data collection for environmental parameters, health and safety and corporate responsibility will be implemented during 2015.
We use three online data reporting questionnaires to measure and collect performance data throughout the Group via the ABB intranet – an annual social report from every country, an annual environment report from every site and a monthly health and safety report from every country which consolidates inputs from all entities in the respective country. Further details on scope and approach can be found in the Performance Summary section of this report.
Activities in 2014
During the year, the ABB Sustainability Board reviewed the Group sustainability strategy and objectives and confirmed the proposed 2015 focus activities and performance metrics. The Board agreed to include the safety metric ‘hazard reporting’ in the Group-wide ‘Relentless Execution’ dashboard – a panel of business-related metrics that will be reported regularly by all businesses in 2015. This is the first time a sustainability-related metric has been included in a set of Group metrics.
The Sustainability Affairs organization was strengthened in order to focus activity on the constituent areas of Health, Safety and Environment, and to reflect the importance attached by the CEO and Executive Committee to safety improvement. Leaders have been appointed to drive Group activities in these three areas, working with our businesses and with the respective sustainability networks on improvement projects and initiatives, and reporting to the head of Sustainability Affairs.
As part of our continuing work to strengthen the capability of our sustainability network, more than 80 of the top sustainability leaders in ABB undertook 360 degree assessments during 2014. Results were shared with each participant during a one hour session with a 360 degree feedback coach, who assisted with analysis of results and identification of suitable development activities. Consolidated results are also being reviewed at Group level to identify any common development requirements.
To ensure that we have the right sustainability resources and structures in place to support our businesses with implementation of the Next Level strategy, we have kicked off a comprehensive workforce mapping and skills inventory. The results, available in the first half of 2015, will guide development programs and allocation of resources at different levels in our businesses.
Material issues
We have undertaken considerable work in recent years to understand what internal and external stakeholders expect of ABB’s sustainability performance and where we should focus our strategy and improvement goals. We regularly review and evaluate these material issues to determine if they remain consistent and relevant, and if there are any new and emerging issues we need to address.
In 2011, we conducted a materiality assessment with input from nearly 600 people, including senior ABB executives and employees from all parts of the business, customers, and external stakeholders specialized in key sustainability areas. We also mapped regulatory risks and macro trends, and benchmarked against peer companies to help us establish a comprehensive sustainability issues landscape. The resulting materiality matrix then shaped the development of our sustainability strategy during 2011.
We undertook a further review with our stakeholders during 2013 to update our assessment of material aspects and to seek their views on how best to report on our sustainability strategy, performance and progress. The results from interviews with ABB employees, investors, customers and external sustainability experts, in the main, confirmed the conclusions from our 2011 consultation and helped us to shape our Sustainability Objectives 2014–2020.
In 2014, we consulted our stakeholders again: to gauge their views on the newly-released sustainability objectives and the 2013 matrix, and how we report on our sustainability performance. We also sought to assess any changes in their evaluation of ABB’s material issues following the release of ABB’s Next Level strategy.
This consultation focused solely on external stakeholders, as leaders from ABB’s business, countries and functions were extensively involved in the development of the Group Sustainability Objectives and the new business strategy.
A third party conducted 29 interviews with representatives across our key constituencies: Customers, suppliers, investors, civil society, including NGOs, international organizations, sustainability experts and young people. Around 40 percent of participants had been involved in previous consultations.
Overall, stakeholders found that the 2013 matrix provided a good snapshot of relevant issues for ABB, although a number of stakeholders requested better definition of the specifics considered within each issue.
Feedback from stakeholders
Eight of the material issues were considered by some stakeholders as more important – developing our people, waste and recycling, hazardous substances, innovation, human rights, working in the community, water, and health, safety and security – whereas only governance was considered slightly less important. Stakeholder views differed on the placement of three specific issues – stakeholder relations, energy efficiency and risk management.
Stakeholders expressed diverse views about new or missing issues, with some topics already encompassed in the existing material issue categories. However, there was insufficient support on any new single issue to justify its addition to the matrix.
We have updated our materiality matrix accordingly. Ratings of various issues have been adjusted in line with the feedback outlined above. We have also harmonized the terms used in the matrix with the language of our sustainability objectives to increase understanding and have developed definitions of the material issues. However, we have kept the internal and external constituencies of “People and society” separate to ensure a better focus on actions and outcomes. Other key changes are:
- “Water” and “Waste and recycling” now combined under “Resource efficiency”
- “Stakeholder relations” and “Working in the community” now combined under “Stakeholder engagement”
- “Risk management” removed from the matrix in response to commentary from stakeholders that the relevant risk – and opportunity – should be dealt with within each issue category
Regarding ABB’s Sustainability Objectives 2014–2020, stakeholders considered our 2020 ambitions highly relevant, reflecting the key issues on which the Group should focus. Products and services was clearly identified as the most important objective. However, stakeholders also told us that we have further work to do to ensure the KPIs and targets underpinning the objectives match our ambition levels. We acknowledge this point and, as noted throughout this report, we continue to develop the KPIs, targets and underlying programs to achieve our objectives.
Stakeholders also wanted to understand ABB’s contribution to broader societal goals and emphasized the importance of responsibility and collaboration along the value chain.
These stakeholder views are helping us to further shape the targets underpinning our Sustainability Objectives 2014–2020 and have helped to determine the structure and content of this report. We will continue to review these issues with our stakeholders at regular intervals and will use this input to inform our improvement goals and reporting activities.
Material issues defined
Products and services:
- Innovation and R&D
- Eco-efficiency and safety of products and services – reducing impacts of product’s use
- Innovative technology and services for renewable energy generation and grid integration
- Innovative technology and services to promote electrification, such as e-mobility, electrification of ships
Energy efficiency and climate change:
- Energy intensity of own operations, including direct fuel consumption and the use of electricity and district heating for manufacturing processes and to operate buildings
- Carbon intensity of energy use, including purchased ‘green’ energy, own generation of renewable energy, conversion to lower carbon forms of primary energy or electrification.
- Direct emission of greenhouse gases (GHG) from SF6 handling on-site, production processes involving SF6
Safe and secure operations:
- Safety of ABB employees, contractors under our control and members of the public affected by our activities, at our own sites and those of our customers
- Occupational health of employees and contractors
- Physical security of our people and assets, including manufacturing operations, service activities and project sites
- Crisis management and business resilience
- Security of ABB employees while on business travel
- Cyber security
Integrity:
- Behavior of employees and business partners along the value chain, defined by ABB Code of Conduct and Supplier Code of Conduct, policies and standards, and applicable laws
- Includes anti-corruption, anti-bribery, anti-trust, appointment of representatives, gifts and entertainment, legal compliance
- Detection and resolution of non-compliance
Responsible sourcing:
- Sourcing of materials, products and services
- Social and environmental risks and impacts of sourcing practices, including social and environmental performance of suppliers, material compliance, conflict minerals
- Detection and resolution of non-compliance
- Support for supplier development and performance improvement
Human rights:
- Social and environmental impacts of business activities at customer and own sites, in supply chain and communities, and through other business partnerships
- Community relations and engagement
- Compliance with national and international laws and standards on labor and human rights
- Identification and mitigation of potential risks
- Activities in sensitive countries and regions
- Access to remedy, detection and resolution of grievances
Developing our people:
- Attraction and retention of talent
- Learning and development
- Diversity and inclusion
- Employee engagement
- Employment conditions, labor rights
Right materials:
- Sourcing, design and manufacture of our products
- Use of hazardous substances (chemicals and toxic natural resources, e.g. cadmium) and scarce materials
- Compliance with legislation, e.g. EU REACH and EU RoHS, Dodd-Frank Act
- Customer requirements
Resource efficiency:
- Impacts of our own operations
- Water use, material use/waste generation and recycling
Stakeholder engagement:
- Interaction with customers, suppliers, investors and civil society
- Incorporating stakeholder feedback into our business
- Partnerships for improved performance
- Projects and philanthropy
2013 materiality matrix
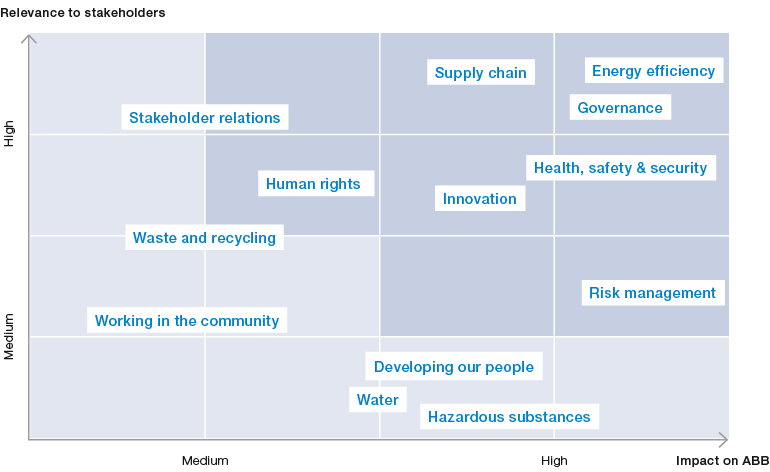
2014 materiality matrix
Mouse over the image to see the definitions of each material issue.
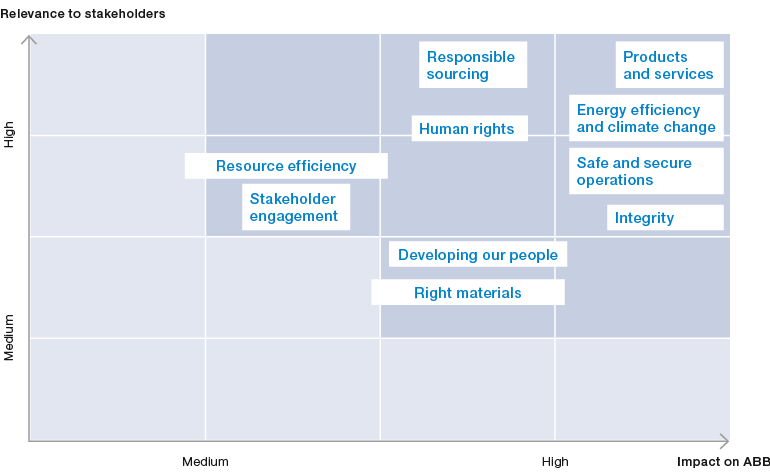