Personal commitments to improved performance
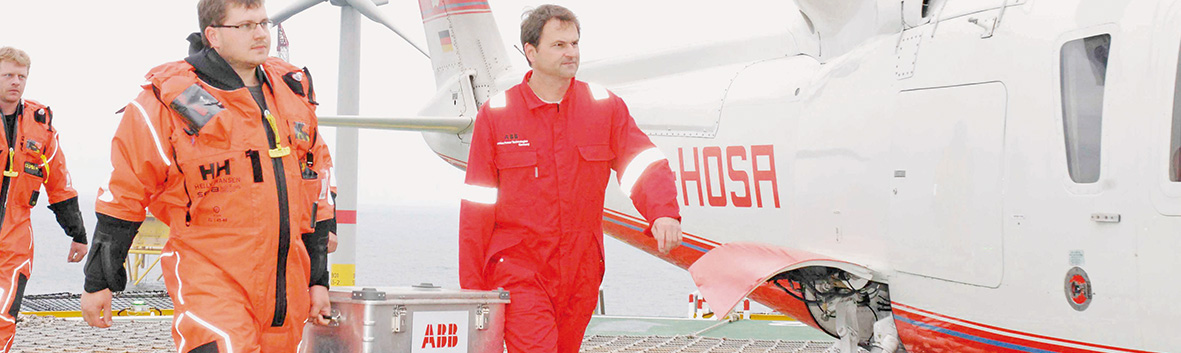
Safety is ABB’s first priority. Our objective is that by 2020 all ABB operations will have an excellent health, safety and security culture embedded in their day-to-day business, targeting zero incidents.
Even though ABB has long-standing programs in place across our businesses and our geographies to support this ambition, we faced a particularly challenging year in 2013, when we recorded a sharp increase in serious safety incidents. This prompted us to closely review how we promote and support safety throughout our global operations.
In response, in early 2014 our senior leadership launched a drive to truly embed safety as a core company value. “Don’t look the other way” defines the required behavior throughout the organization and activity under this banner is focused on positive behavioral change, emphasizing personal leadership and accountability as the basis for fundamentally improved safety performance.
Commitment to cultural change
The initiative started at the top, with ABB’s first-ever personal safety commitment signed by the Executive Committee and our top 200 leaders in March 2014. The commitment emphasizes personal responsibility, job-appropriate safety training for all, establishing a safe system of work for all tasks and the importance of reporting and learning from all incidents.
A dedicated web portal has been established to communicate the initiative throughout ABB, training materials have been developed and ABB country organizations and businesses have aligned their safety activities and programs. Regular Group-wide and local communication ensures that the initiative remains visible and relevant.
This commitment is further supported by the requirement for all ABB employees to include a health and safety behavioral goal in their annual objectives, starting 2014. The aim is to further embed positive safety behaviors at all levels and to ensure that formal discussions of these behaviors occur across the company.
First global Safety Week
ABB initiated a Group-wide Safety Week in November, aimed at further engendering a safety culture across the company. During the week, ABB employees were offered opportunities to learn about how they can make ABB a safer place to work, whether they are in a factory, an office, or on a project or customer site.
Events included global and local training sessions, meetings, and events in ABB facilities, and at project and customer sites. ABB contractors and customers were also invited to participate in some of the 2,500 training sessions held globally, which attracted around 142,000 attendees.
Safety Week also saw the launch of a new CEO Safety Award, designed to mark achievements and successes in improving health and safety, as well as reinforce the importance of safety throughout the organization. Awards will be presented at the annual Group Leadership Forum in March 2015.
Next Level strategy and targets for 2020
ABB’s commitment to safety as a corporate value was further underlined with the launch of our Next Level strategy during 2014. The strategy explicitly defines responsibilities at all levels of the organization, with accountability for safety assigned along business lines. These responsibilities and accountabilities clearly link business value with the ability to deliver safely and with integrity – pre-requisites to achieving our ambitious growth targets.
During the year we also developed detailed targets and supporting KPIs that will help us to achieve our ambition to be best-in-class in safety by 2020. The focus is on leading indicators, aimed at ensuring appropriate systems, competence and behaviors are in place to identify and eliminate hazards before they cause harm or injury.
- Safety Observation Tours (SOT): By 2020 we will be conducting 180,000 SOTs annually, achieving a rate of 1.2 SOT per employee. SOTs are a top-down approach that helps employees and managers to think about safety, allowing it to become fully integrated into our daily work. Managers and supervisors tour a work location, engage with people and talk about health and safety and everyday working behaviors, reinforcing safety as a priority and jointly seeking opportunities to improve performance. During 2014 we conducted SOT training throughout the Group and reporting the number of SOTs conducted is mandatory from 2015.
- Hazard reporting: By 2020 we are reporting 300,000 hazards; a rate of two per employee. Serious incidents are often preceded by minor incidents or unsafe behaviors or situations. Formally recording and remedying unsafe acts or conditions reduces the risk in our business, making ABB a safer place to work. Hazard and near miss reporting training was rolled out at the end of 2013 and reinforced during Safety Week. Hazard reporting became mandatory from 2014 and we will report publicly from 2015.
- Certified health and safety management systems: By 2020 more than 95 percent of ABB manufacturing, project and service organizations are covered by a certified management system.
Implementation of management systems in recently-acquired operations continued through 2014.
Tools and programs supporting our strategy
A Code of Practice for Safe Working was launched during 2014, providing detailed, Group-defined guidelines on 50 safety topics for manufacturing, projects and service operations. Topics covered include risk assessment, electrical safety, work at heights, chemical hazards, construction hazards, contractor safety and travel safety. The guide was developed by a committee of experts representing all divisions and our diverse geographies, and is supported by an extensive online learning package available to all employees.
Business-led programs supplement our Group activities, focusing on the particular needs of the different businesses. For example, our Discrete Automation and Motion division has initiated a division-wide health and safety audit process. Comprehensive site reviews complement the program of SOTs, hazard reporting and local management review, providing a vehicle to systematically share best practices across the division.
ABB’s global service organization continues to promote the importance of safety in its value proposition through the annual Global Service Safety Award. The 2014 award winner developed software that makes it easy to report unsafe working conditions – near misses and hazards – from wherever an employee is, using a mobile phone or tablet. It’s an effective mobile tool for a service engineer in the field and is now undergoing further development to test its suitability for rolling out across ABB.
Occupational hygiene
Launched in 2012, the Group occupational hygiene program continued to develop during 2014. The Occupational Doctors Team continued to support our network of health and safety advisors by identifying and communicating good practices through regular conference calls and provision of online resources. In conjunction with external advisors, extensive guidance material was developed regarding Ebola, to assist ABB crisis managers to provide factual updates for our operations. Guidance for dealing with MERS-Coronavirus was also developed during the year.
Our health and safety performance
Sadly, we recorded three fatal incidents during 2014, involving one ABB employee at a customer site in Kuwait and two contractors working at project sites in India.
In response, we have reinforced our global focus on contractor safety, building stronger relationships with respect to safety arrangements, which include contractor qualification, training and control. Specific programs have also been initiated in India to address the particular characteristics of the project work being undertaken there. These programs are progressing well and will be implemented in other regions of the world as appropriate. We also continue to focus on enhanced, transparent reporting of contractor incidents, to enable faster learning from incidents and consequent process improvement.
Lost time injury rates and total recordable incident rates for employees show a consistent downward trend, indicating that our long-standing safety programs and standards support a trend of incremental performance improvement.
With this underlying momentum, ambitious Next Level strategy and unequivocal senior leadership, we will continue to learn from our experiences, address our challenges and drive systematic and cultural improvement across our business.
Secure operations
In an increasingly volatile and insecure world, ABB has been placing greater emphasis in recent years on the security of our people and contractors, particularly in high-risk countries or during crises.
ABB has built up a security capability around the world designed to safeguard our people, protect our assets and meet our customers’ needs – even in some of the most hostile environments.
We have ongoing training programs at Group, region and country levels to help our employees to understand how to act and react under exceptional circumstances.
Injuries, lost days, diseases and fatalities
Download XLS (26 kB) |
|
2014 |
2013 |
a |
2012 |
b |
2011 |
2010 |
||||||||||||||||
---|---|---|---|---|---|---|---|---|---|---|---|---|---|---|---|---|---|---|---|---|---|---|---|
|
|||||||||||||||||||||||
Employee work-related fatalitiesc |
1 |
0 |
|
1 |
|
0 |
1 |
||||||||||||||||
Incident rated |
0.01 |
0.00 |
|
0.01 |
|
0.00 |
0.01 |
||||||||||||||||
Employee business travel fatalitiesc,f |
0 |
0 |
|
1 |
|
0 |
2 |
||||||||||||||||
Incident rated |
0.00 |
0.00 |
|
0.01 |
|
0.00 |
0.02 |
||||||||||||||||
Contractor work-related fatalitiesc,e |
2 |
7 |
|
2 |
|
0 |
2 |
||||||||||||||||
Contractor business travel fatalitiesc,f |
0 |
0 |
|
0 |
|
0 |
0 |
||||||||||||||||
Members of the public fatalitiesc |
0 |
1 |
|
0 |
|
0 |
0 |
||||||||||||||||
Employee total recordable incident numbere,g |
1,500 |
1,664 |
|
1,750 |
|
1,505 |
1,426 |
||||||||||||||||
Incident rated |
9.95 |
10.94 |
|
13.04 |
|
13.17 |
13.48 |
||||||||||||||||
Contractor total recordable incident numbere,g |
333 |
310 |
|
348 |
|
307 |
258 |
||||||||||||||||
Incident rated |
7.76 |
7.52 |
|
8.21 |
|
7.47 |
7.00 |
||||||||||||||||
Employee lost time incident numbere |
652 |
686 |
|
683 |
|
722 |
761 |
||||||||||||||||
Incident rated |
4.34 |
4.70 |
|
4.80 |
|
5.70 |
6.80 |
||||||||||||||||
Contractor lost time incident numbere |
200 |
158 |
|
159 |
|
148 |
120 |
||||||||||||||||
Incident rated |
4.65 |
3.83 |
|
3.76 |
|
3.60 |
3.25 |
||||||||||||||||
Employee lost days due to industrial incidentsh |
8,415 |
10,591 |
|
10,345 |
|
9,478 |
8,362 |
||||||||||||||||
Lost day rated |
55.220 |
77.500 |
|
74.640 |
|
69.560 |
66.370 |
||||||||||||||||
Employee occupational health diseases |
17 |
10 |
|
10 |
|
7 |
13 |
||||||||||||||||
Employee occupational health disease rated |
0.11 |
0.14 |
|
0.07 |
|
0.06 |
0.05 |
In 2014, we carried out a series of mandatory training sessions in 25 countries. For example, nearly 250 members of country management teams received focused sessions on the do’s and don’ts, and processes to follow, in times of crisis. Management teams in countries where ABB has operations and major projects receive crisis training every three years.
There is also ongoing training on a wide range of other security tools and processes.
For example, further teams were trained in 2014 on the issues arising from kidnap and ransom incidents.
In the past, crisis situations for ABB have arisen in a number of areas, ranging from political upheaval in the Middle East and North Africa, to crime and violent incidents in different parts of the world, and natural disasters, particularly in Asia.
In 2014, the biggest concerted effort by Group and regional crisis managers focused on the Ebola disease outbreak, primarily in three West African countries. ABB has only very limited operations and a few people in those countries, but provided regular updates to our people on the development and initial spread of the disease. No ABB people or operations were affected. Read more in our Case study
The ability to analyze fast-moving scenarios and, where possible, predict likely events is part of the capability of our corporate security staff. In an increasingly dangerous world, such skills are essential to help protect our people and strengthen our business resilience.