Resource efficiency
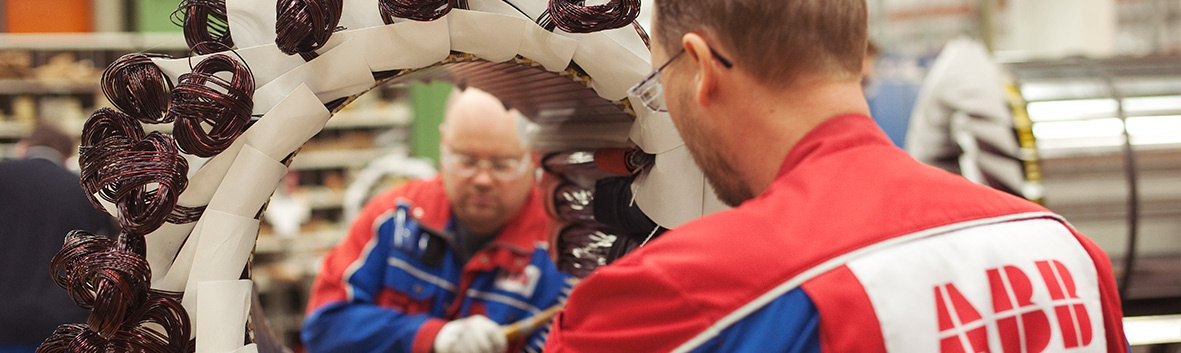
Our stakeholders are increasingly focusing their attention on ABB’s operational efficiency – how we optimize the use of resources and minimize waste. They have also confirmed their interest in how we reduce the use of natural resources during production and ensure our products are safe and compliant.
5,200 kilotons of water saved through reuse and recycling
Addressing these issues contributes to our business success by reducing costs and risks, improving the work environment for our employees and helping to maintain our license to operate.
Water reduction commitment
Although the majority of our manufacturing processes do not consume significant amounts of water, ABB is nonetheless committed to reducing our impact on local water resources.
In order to focus reductions where they are most needed, during 2012 and 2013 we targeted our manufacturing facilities in water-scarce and extremely water-scarce watersheds,1 rolling out an in-house tool for mapping and analysis of water flows. Facilities were required to review water flows systematically and develop water action plans to minimize risks and to leverage opportunities. The newly acquired businesses of Baldor and Thomas & Betts were not required to implement the ABB Water Tool during this phase due to their participation in specific integration programs.
Our Sustainability Objectives 2014-2020 expanded the scope and quantified this target. We are committed to reduce absolute water use by 25 percent by 2020 at facilities in water-stressed, water-scarce and extremely water-scarce watersheds, compared to a baseline of 2013. The initial focus will be on 30 selected facilities.
Following a range of business divestments in 2014, we will update our facility mapping during 2015 and define the 30 facilities included in the initial program.
1Food and Agriculture Organization of the United Nations (FAO) (2003). Review of world water resources by country. Water Reports 23. Rome. According to this methodology, a watershed is considered water-stressed if the total actual renewable water resources (TARWR) are below 1,700 m3 per person and year, water-scarce if below 1,000 and extremely water-scarce if below 500.
Water in our global operations
Looking at ABB’s global operations in 2014, there were no significant changes in our water withdrawal, use or discharge results compared to 2013, apart from a decrease of about 12 percent in the volume of reused and recycled water. Business divestments during 2014 did not have a material impact on our water profile.
Sources of water withdrawals in 2014 (2013)
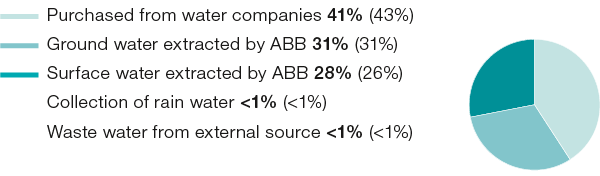
In 2014, more than 50 percent of ABB’s water withdrawals were used for cooling processes, almost 30 percent for domestic purposes such as sanitation, cooking or garden maintenance and the remainder for manufacturing processes.
Water withdrawals and water reused / recycled (kilotons)
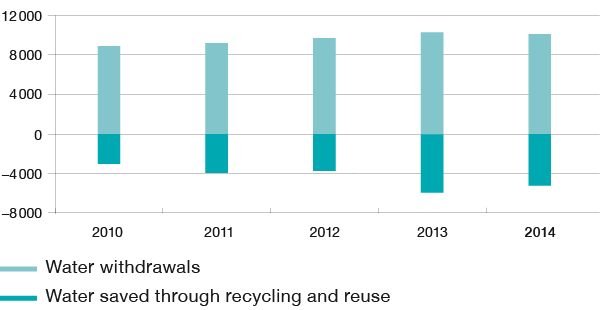
Of those sites that use water for process purposes, more than 30 percent use closed-loop systems. Excluding cooling water returned to the source of extraction, the use of closed-loop processes and the reuse of water in other ways saved approximately 5,200 kilotons of water in 2014. Without this recycling and reuse, ABB’s water withdrawals would have been more than 50 percent higher.
About half of our water discharge was to public sewers (48 percent), with approximately one-third of that volume first processed at our own treatment plants. Another 46 percent was discharged to surface or ground water, with almost 90 percent of that volume pre-treated. The remainder was handled by hazardous waste water treatment companies.
Our San Luis Potosí facility in Mexico reports that its water withdrawals are likely to have an impact on its water sources due to local water scarcity. Therefore, in 2014 the facility stopped withdrawing ground water – previously about 50 percent of total water withdrawal – and now treats and reuses all sanitary waste water from the campus. This saved over 11,000 m3 of water in 2014.
Many other site-level water efficiency projects were undertaken during 2014, with most creating significant benefits for the facility. Projects ranged from major repair and refurbishment of water systems at facilities in China, Canada and Germany, resulting in substantial water and cost savings, to collection of rain water for use in all process work at a facility in Australia, and the installation of waterless urinals at facilities in Finland and Spain. Many locations report the effectiveness of continued water conservation training and awareness-raising programs for employees.
A number of facilities examined their water flows and redesigned processes to enable increased recycling or reuse of waste water. Additionally, closed-loop systems were expanded in China, Italy, Saudi Arabia and the United States, or were newly installed at a large facility in the United States. In Peru, the entire sewer network at one plant was redesigned to enable separation of domestic and industrial waste water, with the potential for future treatment and reuse of domestic waste water flows.
Waste and recycling
ABB products contain mostly steel, copper, aluminum, oil and plastics, and the majority of this material is reclaimable at the end of the product’s life. We enhance the ability to recycle by designing products that can be dismantled more easily and by providing users with recycling instructions.
Consequently, the main waste streams at ABB facilities are metal, oil and plastic, as well as wood and cardboard from packaging materials and paper from office activities. We aim to optimize material use and increase the share of waste that is reused or recycled.
We are committed to reduce the amount of waste sent to final disposal – both hazardous and non-hazardous – by 20 percent by 2020. This will be measured as the proportion of total waste sent for final disposal and compared with a 2013 baseline.
There was a nine percent decrease in total waste generated in 2014 compared with 2013. The majority of this is due to business divestments during 2014. Due to the significant amounts of scrap metal and non-hazardous waste reported by those businesses in 2013, we consider that approximately 100 percent of the observed reduction in scrap metal, 70 percent of the reduction in recycled non-hazardous waste and over 35 percent of the reduction in non-hazardous waste sent for disposal in 2014 was due to the impact of the divestments. The divested businesses reported negligible hazardous waste and on-site recycling in 2013.
20% increase in materials recycled and reused in-house
In 2014, ABB sent 79 percent of total waste for recycling, compared with 81 percent in 2013. Again, this apparent reduction in the recycling rate is due to the impact of the high volumes of scrap metal reported by the divested businesses in 2013.
In-house recycling, mainly of packaging materials and thermoplastics, reduced the amount of waste by more than 4,980 tons, an increase of around 20 percent from 2013. In total, we generated almost 18,000 tons of hazardous waste in 2014, but sent about 25 percent of that amount for recycling rather than disposal.
Waste and recycling
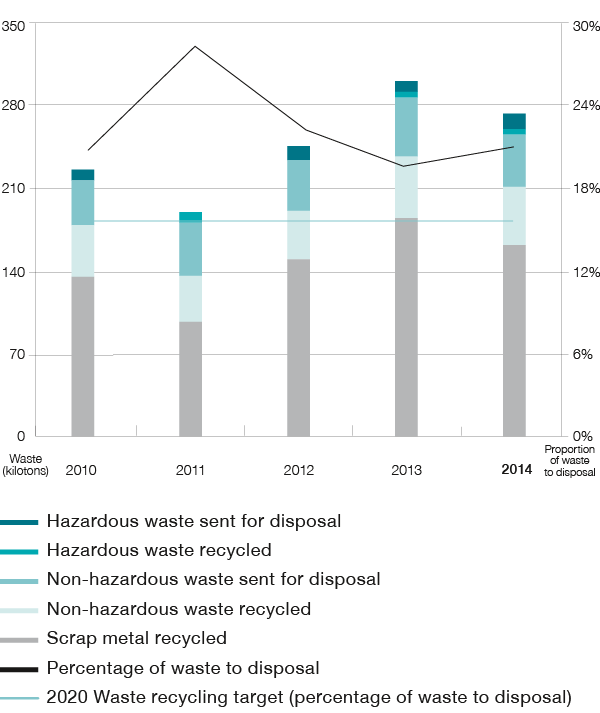
ABB operations undertake a wide range of waste reduction and recycling initiatives, bringing both environmental and cost benefits for the business. The nature of the improvement activities generally depends on the characteristics of the production processes and the local waste infrastructure, but there were common themes.
Many locations have conducted detailed on-site analyses and are working with their waste management vendors, or have selected new vendors, to optimize recycling options. Revenues realized from a range of waste streams along with the reduced costs of waste disposal reinforce these efforts within our businesses. Read more in our Case study
During 2014, many facilities pursued operational excellence projects to optimize material use and reduce waste, but a number of our operations also invested in novel processes aimed at reducing and reusing waste. For example, a plant in China upgraded its filtration process to enable reuse of a specialized oil, not only reducing oil waste by 20 tons, but reducing costs by more than $100,000. At an insulation and components manufacturing facility in India, an in-house lamination process was developed to reuse offcuts from other processes. In Sweden, installation of a special room for chemical waste allowed for better sorting and labeling options, thus improving recycling and cutting disposal costs.
Reduction and reuse of packaging, such as repurposing wood from transport crates and encouraging the use of reusable, bulk containers by suppliers, are also helping to reduce waste volumes on sites. A number of locations adapted administrative procedures to avoid or minimize the use of paper, and many sites are focusing on improved recycling of beverage containers or have ceased using disposable water bottles and cups altogether.
Reduction of hazardous substances
ABB is committed to minimizing our environmental impacts and to ensuring the health, safety and protection of people who come into contact with our products and business. We continue to phase out hazardous substances in products and processes, where technically and economically feasible, with the ambition to use these substances in closed loops or not at all.
This requires attention to product design and manufacturing processes, as well as to our supply chain, to ensure that the materials and components we use and the products we produce comply with our own and our stakeholders’ standards.
To guide this process, we have compiled lists of prohibited and restricted substances, which reference international regulations. These lists are updated regularly and help both our engineers and suppliers to comply with regulatory requirements and to manage potential risks caused by the presence of chemicals in various products.
Use of hazardous substances (tons)
Download XLS (23 kB) |
|
2014 |
2013 |
2012 |
2011 |
2010 |
---|---|---|---|---|---|
Phthalates – softener for PVC |
258 |
21 |
28 |
47 |
31 |
PBB and PBDE – flame retardants |
1.9 |
2.9 |
~0 |
~0 |
~0 |
Lead in submarine cables |
7,842 |
7,236 |
5,633 |
5,725 |
3,632 |
Organic lead in polymers |
0.1 |
0.6 |
0.9 |
1.3 |
52 |
Lead in other products, e.g. backup batteries and counterweights in robots |
1,884 |
2,601 |
363 |
227 |
265 |
Cadmium in industrial batteries delivered to customers |
4.4 |
4.4 |
5.6 |
1.6 |
1.7 |
Cadmium in rechargeable batteries |
75.1 |
67.6 |
6.3 |
10 |
5.9 |
Cadmium in lead alloy and other uses |
6.0 |
5.7 |
4.5 |
4.3 |
2.9 |
Mercury in products delivered to customers |
0.071 |
0.012 |
0.011 |
0.030 |
0.038 |
SF6 insulation gas (inflow to ABB) |
1,483 |
1,438 |
1,139 |
1,052 |
968 |
SF6 insulation gas (outflow from ABB) |
1,466 |
1,425 |
1,118 |
1,040 |
959 |
Our suppliers are requested to comply with these regulations, which are also part of ABB’s Global Terms and Conditions and Supplier Code of Conduct. We have developed a Guide for Suppliers to the ABB List of Prohibited and Restricted Substances to help our suppliers understand and implement the ABB List and to provide guidance on suppliers’ obligations.
ABB facilities are required to ensure compliance with the ABB List and to work to phase out hazardous substances in their processes and products.
As we integrate our recent, large acquisitions, Baldor and Thomas & Betts, we are seeing changes in our Group profile of hazardous substances due to the different product portfolios and manufacturing processes undertaken by these businesses. In particular, in 2013, the first year both companies reported on their environmental performance, we saw an increase in lead and cadmium in batteries delivered to customers and in polybrominated flame retardants used in polymers. A substitution program resulted in reductions in the use of these polybrominated flame retardants in 2014.
During 2014 we worked to improve the quality of hazardous substances reporting through further investigation of complex mixtures and polymers. As a consequence, we report a significant increase in phthalates, used as plasticizers in polymers, mainly due to raw material used at one plant in the United States. Use of lead in rubber compounds in two plants in the United States also impacted the category lead in other products.
Emissions of volatile organic compounds (tons)

Ongoing activities at other plants are beginning to show results. We are making progress in the elimination of lead in solder, with a reduction of 24 percent in 2014, and with the substitution of various chemicals used in metal cleaning processes. For example, the construction of a new interrupter facility at one of our plants in India provided the opportunity to install an ultrasonic alkaline degreasing facility – an investment of over $100,000 – resulting in the phase-out of chlorinated solvents from January 2015. Also in India, extensive testing led to the replacement of solvent-based degreaser with a neutral soap solution.
Promoting material compliance
ABB’s network of environmental specialists works alongside our product development and supply chain functions to promote material compliance. During 2014, we reinforced our continuing work around REACH compliance through the delivery of eight training sessions on different aspects of the regulation to our cross-functional REACH network.
As well as targeting the phase-out of hazardous substances in our products and processes, ABB has also initiated programs to monitor the source of certain minerals more closely.
ABB is aware of and concerned by the conflicts occurring in the Democratic Republic of the Congo. We are actively working to identify which products and material from suppliers may contain conflict minerals and are engaging with our customers regarding their disclosure obligations.
In 2014, we provided our first report regarding conflict minerals to the United States Securities and Exchange Commission according to the requirements of section 1502 of the Dodd-Frank Wall Street Reform and Consumer Protection Act.
Improvement by design
ABB’s Research and Development (R&D) engineers and scientists are key to ensuring that our environmental, and health and safety ambitions are designed into ABB’s products and solutions.
The ABB Gate Model process defines our Group-wide approach to product and technology development and is designed to ensure appropriate consideration of all aspects needed to satisfy a project’s defined objectives. These include consideration of legal, technical, strategic, manufacturing, customer and other requirements.
Sustainability aspects are built into the Gate Model and include a standardized Life Cycle Assessment (LCA) procedure and a handbook to guide consideration of environmental, and health and safety aspects during design. We have developed support materials such as a Health, Safety and Environment (HSE) checklist and training packages for our research technologists to improve understanding and ensure these aspects are incorporated into design.
During 2014, we updated the HSE checklist to reflect ABB’s 2014–2020 Sustainability Objectives and strengthened the sections related to hazardous materials and other potentially controversial materials, such as conflict minerals, rare earth elements and palm oil. Rolling out these changes, we trained 132 R&D engineers on the updated checklist, with over 80 percent of the project leaders at our largest R&D center trained.
To further increase awareness of how technologists can influence environmental performance through product and process design, ABB’s Corporate Research Center (CRC) in Sweden established a “Green Project of the Year” award in 2013. With the second round of entries submitted during 2014, the awards program is now providing feedback to improve the sustainability support materials for R&D engineers. For example, one of the projects evaluated for the award prompted questions around rare earth elements. These questions were investigated through a small research project, with the results now incorporated in the updated HSE checklist.
The Swedish CRC also undertook a first-time “materiality” survey in 2014 to better understand the sustainability topics prioritized by R&D technologists and their various customers. The results of the survey were still being analyzed in early 2015, but will be used in part to improve communication of sustainability within ABB.
LCA is not only required as part of a product’s research and development phase, it is also used in the concept development phase for next generation products. ABB develops Environmental Product Declarations to communicate the environmental performance of our core products over their life cycle. Declarations are based on LCA studies, created according to the international standard ISO/TR 14025. Approximately 80 declarations for major product lines are published on our website.