Learning from experience
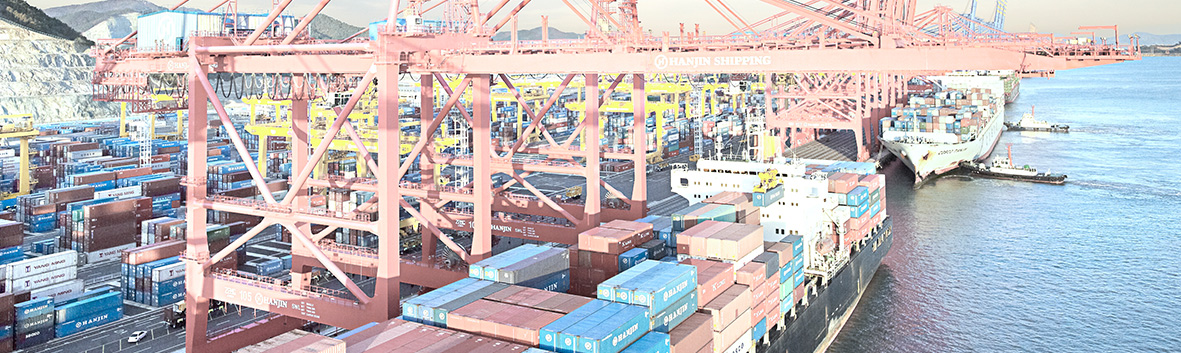
ABB is a large and complex organization, operating in approximately 100 countries, with manufacturing facilities located around the world. We manufacture products in over 300 product lines and have approximately 80,000 direct material suppliers.
ABB recognizes our suppliers as a valued and integral part of our company’s long-term success. We consider them to be part of our extended enterprise and, consequently, require our suppliers to honor the same sustainability and integrity standards as ABB. These standards are defined in the ABB Supplier Code of Conduct, which reflects the 10 principles of the UN Global Compact and the content of ABB’s Code of Conduct.
Building relationships with best-in-class suppliers is an essential aspect of ABB’s global supply chain management strategy, focusing not only on cost, quality and on-time delivery, but also on suppliers’ ethical, social and environmental performance. Our structured approach to supplier qualification, performance evaluation and development supports our suppliers to achieve sustainable improvement and, ultimately, provides our customers with a competitive and sustainable supply chain.
ABB’s process to register and prequalify suppliers is operated through our partner Achilles, which provides registration assistance and ongoing support to suppliers. The centralized, online supplier registration and prequalification system means up-to-date, accurate and validated information is available to all our purchasing specialists around the world.
Supplier performance evaluation is conducted in-house, according to a standard, global process, and covers quality, delivery, commercial, technical, and sustainability and risk management topics. The process covers external suppliers of direct material and project services, internal suppliers of direct material, and transport and logistics suppliers, and is required at least annually for suppliers accounting for the top 60 percent of spend in each local business unit. The results of evaluations drive supplier development processes, assuring poor suppliers get better and good suppliers become elite.
Focusing on sustainability improvement
ABB’s Supplier Sustainability Development Program (SSDP) focuses our efforts to ensure compliance with the ABB Supplier Code of Conduct and to support continual improvement in the sustainability performance of our suppliers. The program is structured around a combination of training for both suppliers and ABB employees, on-site assessments and monitoring of performance improvement plans.
598 in-depth supply chain sustainability assessments since 2010
We prioritize suppliers to participate in the program according to a risk matrix, which includes the criticality of the supplier, country risk, commodity risk based on operations characteristics, and spend volume. The selected suppliers receive training about ABB’s global requirements regarding sustainability standards and on practical ways to improve their performance. We then conduct sustainability assessments at the premises of selected suppliers to identify remaining gaps, and help them to develop improvement plans. After that we assess the timely implementation of these plans. Read more about the program on our website.
From strength to strength
The SSDP continues to expand, with the program newly established in Malaysia and South Africa during 2014 and supplier training extended to Indonesia, Thailand and Vietnam. Our internal assessor program, where ABB supply chain specialists achieve third-party certification as supplier sustainability assessors, was introduced to Brazil, India and South Africa, in addition to the existing programs in Mexico and China.
Support material was also enhanced, with the Supplier Code of Conduct now available in 15 languages and the Implementation Guide in four languages. Online learning programs about responsible sourcing and the SSDP were developed as part of the supplier management competency program. Online programs for suppliers are in development.
Since the program began in 2010, we have trained more than 2,500 suppliers (762 in 2014) and over 2,000 ABB supply chain and quality experts (264 in 2014). We have conducted sustainability assessments with 598 unique suppliers, with 175 of those during 2014 mainly in China, India, Brazil, Mexico and South Africa.
At the completion of on-site assessments, suppliers are assigned a risk rating based on the assessment findings. The risk rating determines the required pace of corrective action and whether an on-site re-assessment is required for the closure of corrective actions. Since the beginning of the program, we have assessed almost 1,100 risks (375 in 2014) and, through corrective action programs, have mitigated 675 of these (152 in 2014).
The most frequently identified causes of these risks include lack of knowledge of applicable labor, health, safety and environmental regulations, which can then result in unsafe working conditions, poor environmental practices and excessive overtime. The 10 most frequently identified non-compliance issues are shown below:
The ten most frequent sustainability non-compliance issues found in supplier assessments |
||
General Management |
|
|
Labor and human rights |
|
|
Health and safety |
|
|
|
|
|
|
|
|
|
|
|
|
|
|
Environment |
|
|
|
|
|
|
|
|
To assess how suppliers are maintaining the improvements from their corrective action plans, in 2014 we revisited seven suppliers who had previously undergone sustainability assessment and had successfully closed all corrective actions. We discovered some repeat findings and, after discussion with the suppliers, concluded that we needed to expand the focus of the assessment process to include root cause analysis as well as preventive actions.
We acknowledge that some of the issues identified during supplier assessments cannot be solved simply through training or improving management processes; they require partnership to understand root causes and develop lasting solutions. The assessment protocol has now been adapted accordingly and, from 2015, our assessors will be helping our suppliers not only to reduce their immediate sustainability risks, but also to understand why they arose and to put in place appropriate processes to prevent recurrence.
Many suppliers are now starting to realize real business benefits from the program, while improving their sustainability performance. Read more about some of these suppliers here.
While the SSDP focuses on working with suppliers to improve performance, there are consequences for suppliers unwilling to bring their performance standards in line with ABB requirements. During 2014, 10 suppliers were blocked due to unsatisfactory progress with their corrective action plans. Four of 17 previously blocked suppliers closed their action plans and were allowed to return as active suppliers, bringing the total number of blocked suppliers to 23.
Expanding the focus
During 2014 we put a special focus on contractor safety development through an enhanced subcontractor qualification program. A cross-functional, expert team including representatives from supply chain, quality, health and safety, site management and project management jointly elaborated a specific qualification questionnaire and pre-qualification process for subcontractors for contracted services.
The process focused on health and safety performance, clear roles and responsibilities for contractors and specific exclusion criteria. An extensive pilot program in South America involved almost 90 site assessments and resulted in simplification and enhancement to ensure business relevance and ease of use. An improved contractor qualification process with increased focus on health and safety was also introduced in the Power Systems division, and piloted in a range of countries, including Saudi Arabia, India and South Africa. This pilot proved the practical usefulness of the new protocol, which was released for global use in the Power Systems division by year end.
During the year, we also undertook an analysis of ABB’s risk exposure to water scarcity in the supply chain. We are currently validating that analysis to assess appropriate next steps.
Moving forward in 2015
We will continue our efforts to scale up and replicate the SSDP in 2015. We will roll out supplier assessments in Indonesia, Thailand and Vietnam following the introduction of supplier training in 2014. Poland will also be added as a new focus country to the program. We will also continue re-assessments of suppliers with closed corrective action plans.
Training for suppliers will be further enhanced, reflecting ABB’s own heightened focus on safety, with the roll out of supplier safety reviews, where local managers regularly walk around their facilities, observing practices and engaging employees in discussions on the safety aspects of their jobs. Issue-specific capacity building workshops will also be developed, such as around root cause analysis of excessive working hours.
Number of ABB employees trained
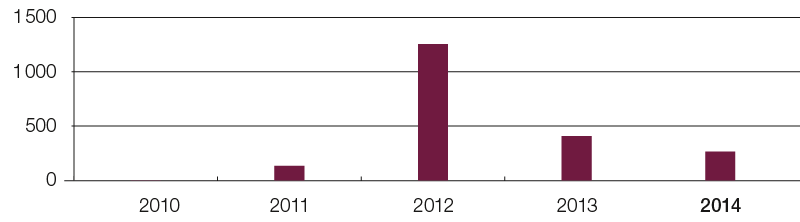
Number of suppliers trained
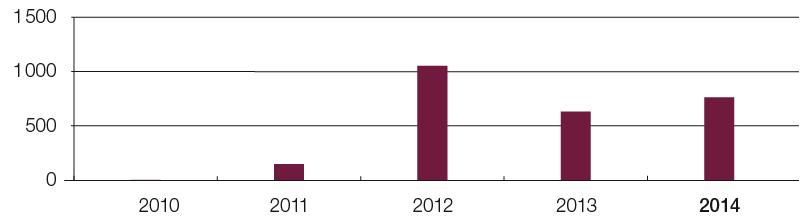
Number of suppliers assessed
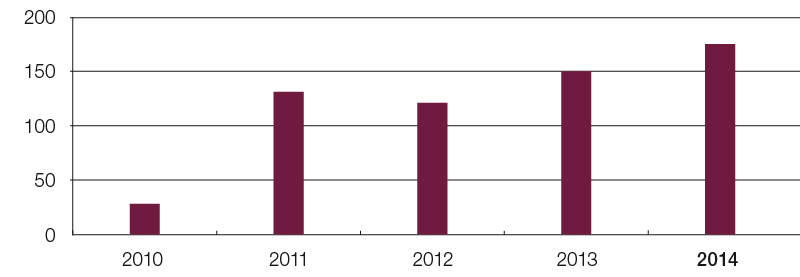