Resource efficiency Making our operations smart and sustainable
One of ABB’s top objectives is to reduce the environmental impact of its sites around the world
We work to optimize our use of resources, minimize waste from our operations, increase the share of waste that is reused or recycled, and ensure that the products we produce and the materials we use comply with our own and our stakeholders’ standards.
Distribution of water withdrawal in 2017 (2013)
Water withdrawal in water-stressed areas 2013–17
Case study Collaborating with local farmers in Mysore, India
Reveal case studyABB’s site in Mysore, India, produces prespane, a type of paper that is used as an electrical insulation material. To generate the high temperatures required during the prespane production process, our site’s furnaces burn sustainable biofuel made from agricultural waste, namely rice husks and briquettes of compressed coconut shells, coffee husks, sawdust and woodchip waste.
Given that agriculture is the predominant occupation of the people who live in the Mysore district of Karnataka, our supply of these sustainable fuels is assured. Moreover, these fuels are remarkably efficient, generating 57 GWh of carbon-neutral energy on-site in 2017, supplemented by 10 GWh of solar power from a local provider. Additionally, the ash from our furnace is delivered to local farmers at our own expense. In 2017, we delivered 3,815 tons of ash. An excellent organic soil conditioner and fertilizer, this ash reduces local farmers’ need for chemical fertilizers.
ABB is proud to participate in this sustainable, circular economy. We use the waste from local agricultural production to power our furnaces, and then the waste from our production processes is used by the farmers to grow their crops.
Close case study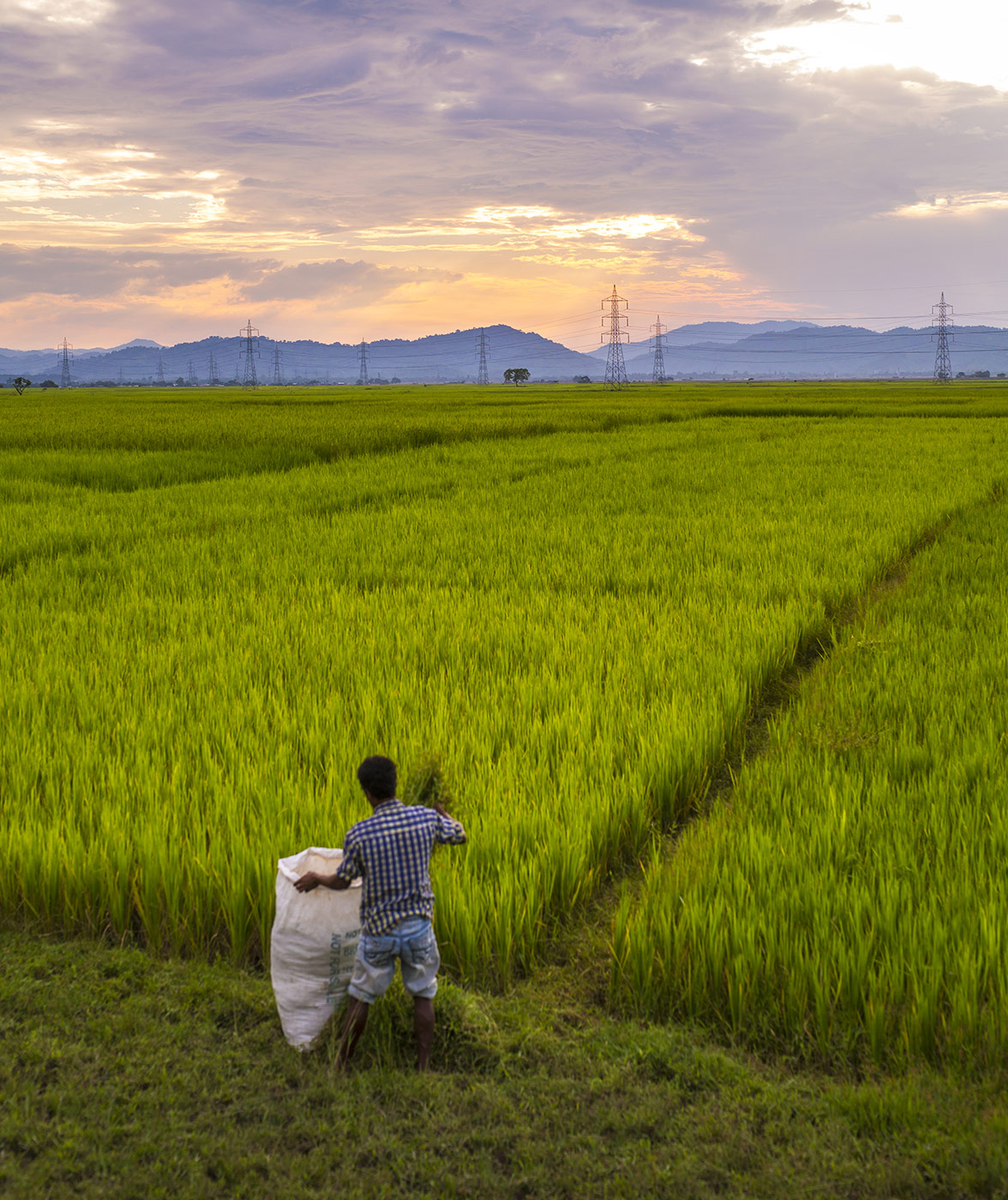
In 2017, no changes were made to our 2020 measures and targets for resource efficiency. Our first target is to reduce absolute water withdrawals by 25 percent between 2013 and 2020 at facilities in watersheds with medium to extremely high baseline water stress. While most of our manufacturing processes do not consume significant amounts of water, ABB is committed to reducing its water impact where it matters most. We map our facilities using the World Business Council for Sustainable Development’s Global Water Tool and classify them according to the level of “baseline water stress” of the watershed where they are located. Of the 561 ABB locations mapped in 2017, 81 face an extremely high level of water stress, 118 face a high level, and 89 face a medium to high level.
Over the past year, we performed well towards our 2020 water target. For all ABB sites in stressed watersheds, total water withdrawals in 2017 were 19 percent lower than the 2013 baseline. We achieved a 1.1 percent reduction in our withdrawals in stressed watersheds compared to 2016, even as our total water use increased by 2.0 percent.
The 35 water reduction projects we implemented across ABB contributed to these savings. For example, a facility run by our Power Grids division in Beijing – an area facing an extremely high level of water stress – cut water consumption by nearly 50 percent after deploying an automated water control and optimization system at its 26,000-square-meter campus.
Our second target is to reduce the amount of waste sent to final disposal – both hazardous and non-hazardous – by 20 percent by 2020. This is measured as the proportion of total waste that is sent for final disposal and compared with a 2013 baseline.
In 2017, we reduced the proportion of waste sent to final disposal to 16.6 percent compared to 19.6 percent in 2013. In-house recycling and reuse, mainly of packaging materials and thermoplastics, reduced the amount of waste by 5,100 tons. Nearly 80 recycling or waste reduction projects were underway in ABB in 2017.
Waste and recycling
For example, this past year our composites factory in Piteå, Sweden, cut manufacturing scrap by 16 metric tons through process optimization, an action that will deliver $65,000 in savings per year. Our semiconductor factory in Prague, Czech Republic, also increased its income from the sale of scrap metal and other waste by $40,000 by using better sorting methods.
Our most significant new initiative in 2017 to support the achievement of our waste reduction target was the introduction of a quarterly KPI at 300 of our largest manufacturing sites to track progress on sorting and recycling of non-hazardous waste. These sites represent more than 95 percent of ABB’s generation of non-hazardous waste. This year we also launched a global control standard on waste management that explicitly states sending waste to landfill should be avoided.