Right materials Eliminating unsafe substances
ABB is phasing out hazardous substances from products and processes wherever feasible
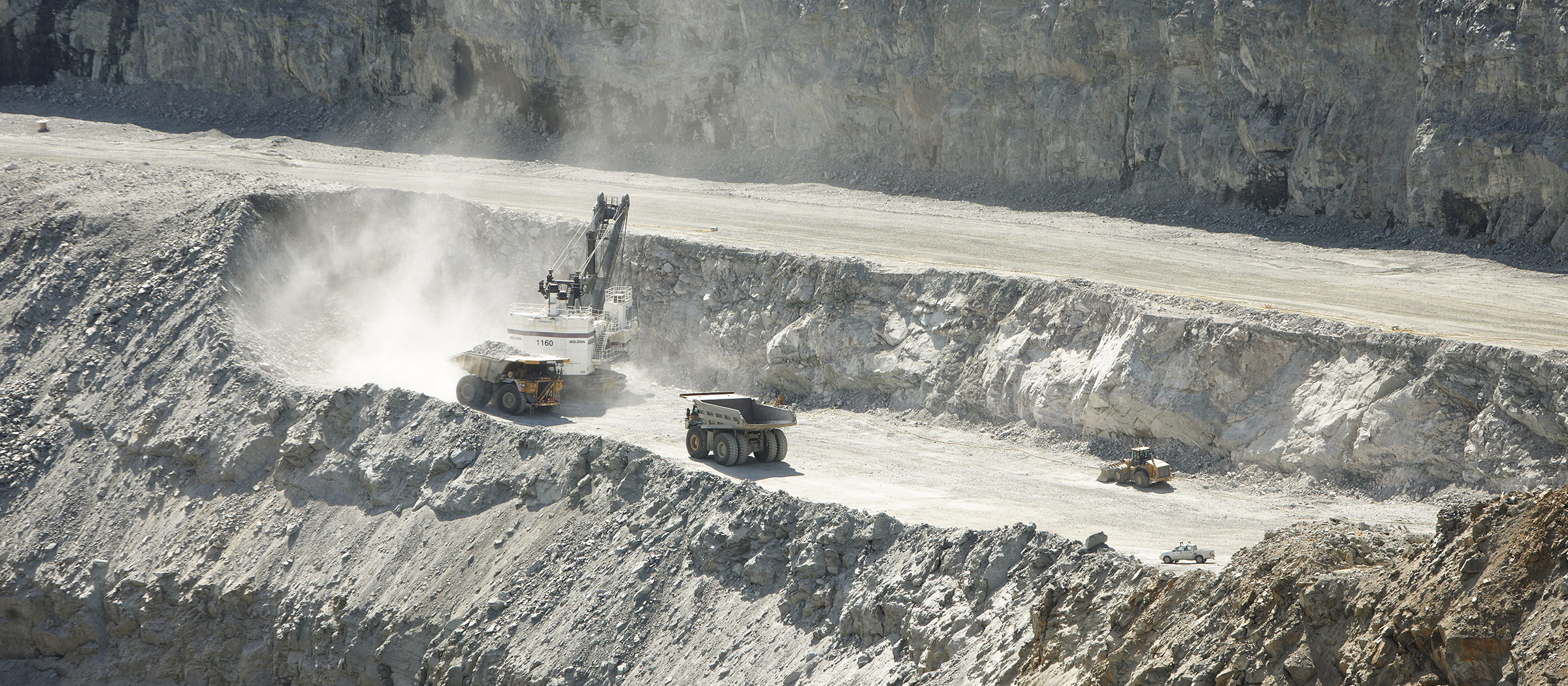
Emissions of volatile organic compounds
To help us phase out hazardous substances, we have compiled the ABB List of Prohibited and Restricted Substances. The list, which is updated regularly in line with international regulations, applies to all our operations, including goods supplied to ABB, product development, production processes, products, packaging materials, service activities and construction sites.
This list helps our facilities to comply with regulatory requirements and to ensure the protection of human health and the environment along the value chain. As regulatory compliance is also part of ABB’s Global Terms and Conditions for suppliers and our Supplier Code of Conduct, we have developed a companion guide to the list to support suppliers’ understanding of their obligations. These obligations include their ongoing partnership with us to identify and prevent “conflict minerals” and restricted substances from entering ABB’s supply chain.
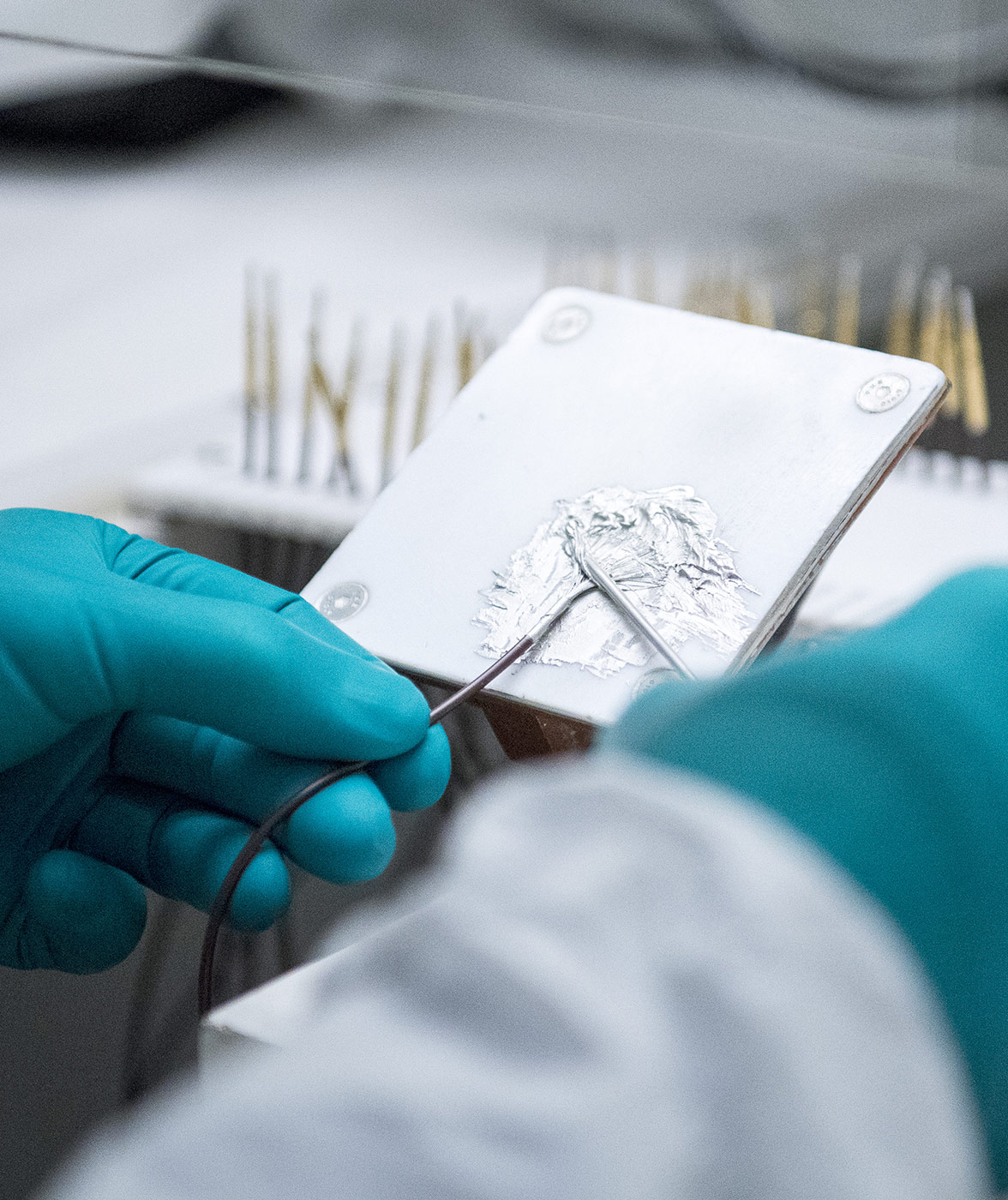
In 2017, we refined ABB’s 2020 measures and targets for the materials we use. Going forward, our objective is to reduce our emissions of volatile organic compounds (VOCs) by 25 percent by 2020. This target further strengthens our efforts to reduce the use of substances that are harmful to human health and the environment.
We performed well towards our 2020 target over the past year, as our VOC emissions decreased by 11 percent compared to the year before. We achieved this result through measures such as substituting less harmful products for solvents, recycling solvents in used paint, switching to low-VOC paints, and installing technical equipment to reduce emissions.
In 2017, our most significant initiative was the establishment of a cross-functional material compliance team. Its mission is to facilitate a standardized and systematic approach to the increasingly complex material compliance regulations we face in our global markets, based on best practices. The team assessed current efforts in the business units, communication with suppliers and customers, standards, guidelines, tools, trainings and internal expert support. The team also worked with ABB’s divisions to develop and release new global standards and guidelines, together with new, globally available webinar training packages on the REACH regulation and the RoHS directive.
19%
decrease in VOC emissions since 2013
In 2017, 48 projects were underway to reduce and phase out hazardous substances and VOC emissions. ABB’s network of environmental specialists collected and shared best practices from these projects to demonstrate how to phase out hazardous substances and the benefits of doing so. Due to the variety of products and manufacturing processes across our organization, hazardous substances are generally reduced on a site-by-site basis.
Case study Conflict minerals
Reveal case studyAt ABB, we are working to ensure our products do not contain minerals (including gold, tin, tungsten and tantalum, hereafter referred to as “3TG”) from mines that support or fund conflict within the Democratic Republic of Congo or adjoining countries. To help with this work, ABB has a Conflict Minerals Policy and a Conflict Minerals Compliance Program, which is supported and sponsored by ABB’s Executive Committee.
Under the Dodd-Frank Act, we annually report to the United States Securities and Exchange Commission on our use of conflict minerals. In May 2017, we provided our fourth report, which identifies products and components likely to contain 3TG minerals and links them to their relevant suppliers. Each year, ABB asks thousands of suppliers to provide information on their use of conflict minerals in the products supplied to ABB. To date, 396 smelters and refiners of 3TG used by our extended supply chain have been identified.
We participate in the Responsible Minerals Initiative (formerly the Conflict-Free Sourcing Initiative) and have, for the third year running, been recognized for our responsible sourcing of minerals in an independent benchmarking study conducted by the Responsible Sourcing Network. Out of 206 companies evaluated, ABB was ranked 13th.
Close case studyFor example, ABB Ltd. in Stonehouse, Great Britain, phased out hexavalent chromium for the etching of plastic cuvettes, replacing it with acidified potassium permanganate. This change maintained quality levels while reducing the risk to human health and the environment. Similarly, at our traction transformer factory in Geneva, Switzerland, we phased out the hazardous substance m-tolylidene di-isocyanate from the product lines because of the dangers it poses to human health in the supply chain and the risk of future restrictions on its use.