Safe operations Working to eliminate workplace incidents altogether
Safety and security are embedded in ABB’s values and explicit in its policies
We apply best practices in safeguarding our personnel, contractors and other third parties, while we do the utmost to protect our assets, the resilience of our business, and our reputation.
Safety at ABB is a line responsibility, and we do everything to ensure our managers and our people have the skills, knowledge and resources to fulfill this responsibility. Our annual plans, developed to reflect our business needs, always demonstrate our commitment to safety. Likewise, we have put in place extensive security programs to mitigate travel- and work-related risks and we continue to strengthen ABB’s resilience by providing training to crisis management task forces at site, country and regional levels.
0.73
TRIFR rate at the end of 2017
In 2017, we refined ABB’s 2020 targets for safety and security into a single metric – the employee total recordable injury frequency rate (TRIFR)*. Our immediate goal is to reduce TRIFR, the most comprehensive and reliable lagging measure of our safety performance, to less than 0.7 by 2020. While we continue to maintain many other safety and security indicators across our operations, we made this change in order to maintain our sharp focus on reducing injuries.
We have performed well in this regard; at the end of 2017 our TRIFR stood at 0.73. This equates to 91 fewer incidents than were recorded in 2016, an 8 percent improvement. Over the past five years, our program has delivered consistent reductions to ABB’s incident rate, and we have improved our TRIFR by 37 percent since 2013. Because no TRIFR rate above zero can be considered acceptable, we remain committed to eliminating incidents altogether and are well positioned to meet our 2020 target. To this end, we expanded our Safety Masterclass to ensure our leaders have the necessary information, skills and tools to prioritize safety on a daily basis. We also improved our investigation processes, focusing on high-potential incidents to determine how to take action before people are injured.
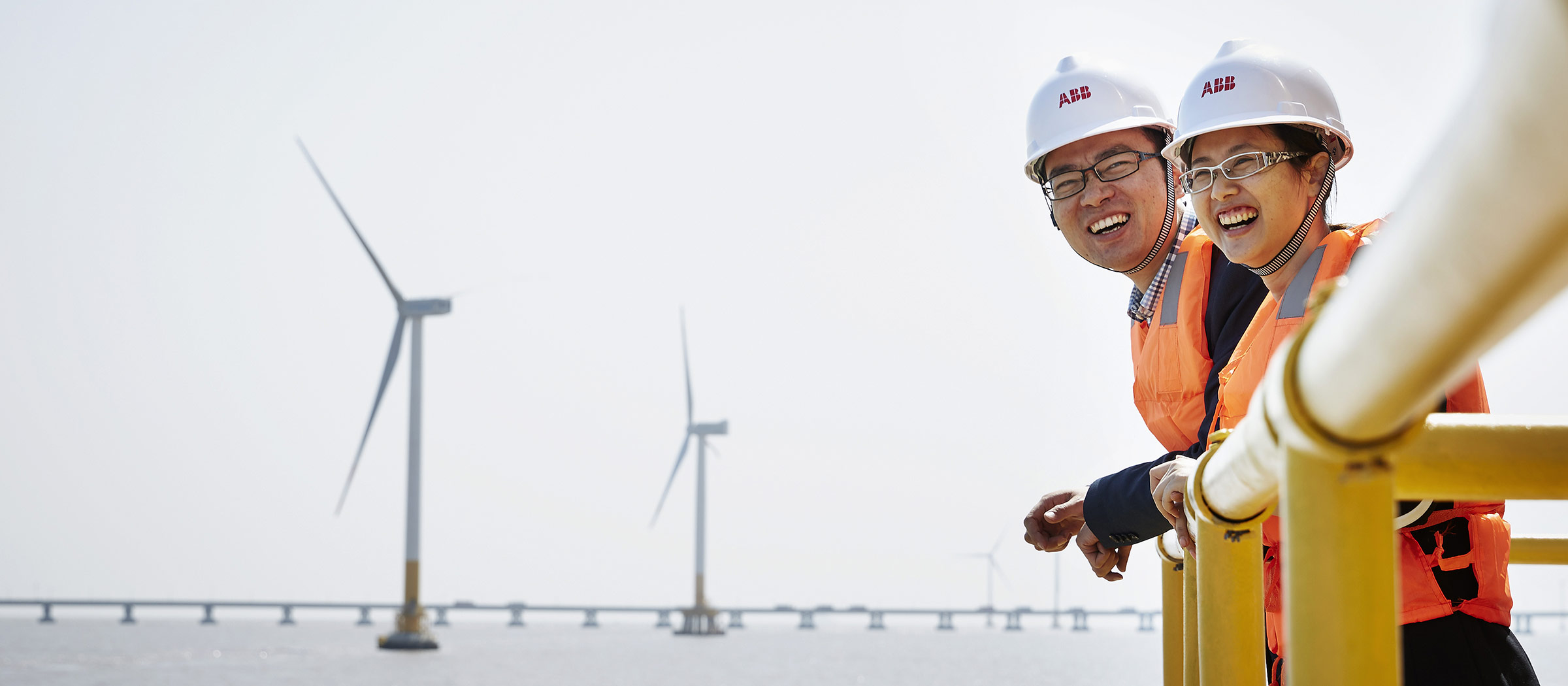
Despite the sustained progress towards our key safety indicator, one employee and two contractors died during 2017 while working on our behalf. The incidents highlighted the importance of our arrangements for working with contractors and with electricity. Our recently introduced accountability framework increasingly ensures that all categories of contractors are incorporated within our control framework and, following on from our work on electrical safety training in 2017, we are reinforcing and adding specialist resources to our electrical safety network, building enhanced global support to our businesses in this critical area of safety.
Case study Person In Charge of Work
Reveal case studyAfter a number of serious electrical incidents and injuries, ABB’s Global Core Team of Electrical Safety Champions organized a workshop to help address our risk management challenges and fortify our electrical safety management system.
The workshop resolved that ABB must develop a Person In Charge of Work (PICW) system, which involves training selected employees and contractors to supervise work associated with electricity.
In response, we designed the 12-hour PICW training course to provide the necessary knowledge, tools and techniques to maintain a safe working environment for every person who works in proximity to electricity on behalf of ABB. At the conclusion of the training, participants had to pass a comprehensive examination to become a PICW. The program started in January 2016 and was completed at the end of 2017.
While the program is not a panacea that can prevent all future incidents, it ensures that all electrical work is carried out under the direction of a competent PICW who is fully equipped to create and maintain a safe working environment. Our 34 percent reduction in recordable electrical incidents in 2016–17 compared to 2014–15 indicates that this program is making a difference.
Close case studyIn 2017, we introduced the “ABB Way,” a single Group management system for health, safety and environment (HSE), security and corporate responsibility. This project, our most significant HSE initiative of the year, updated and extended all our control standards for safety. The ABB Way also incorporates, for the first time, a complete ISO-compliant HSE management system. The ABB Way will be implemented across our business over the next two years, simplifying our approach and improving our shared knowledge and understanding of safety requirements.
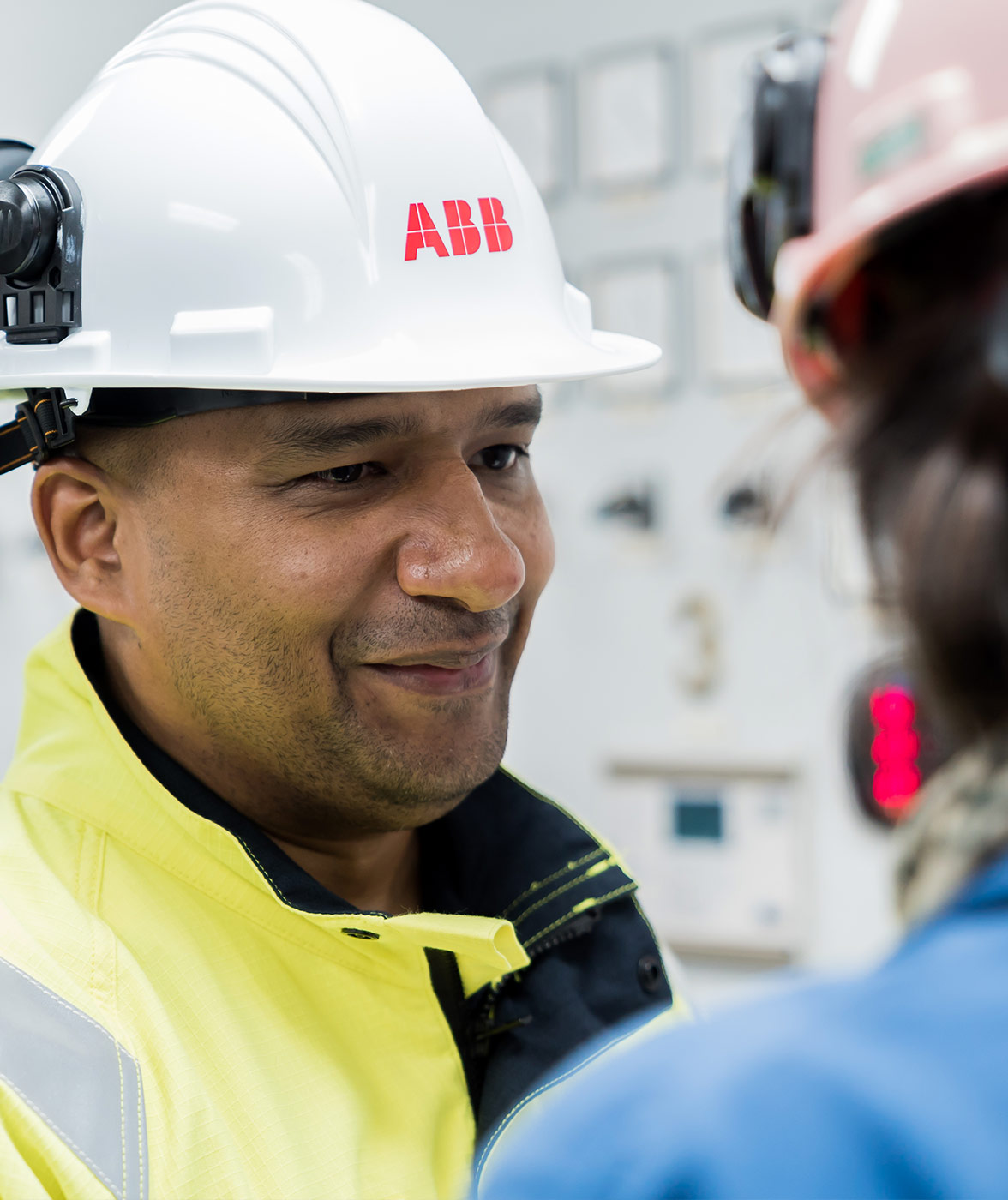
HSE lead managers have been assigned to every ABB facility to ensure that HSE responsibilities are delegated across all our sites. Over the past year, we have established more than 50 formal country HSE and sustainability boards to uphold good governance and assure compliance with local legislation, liability requirements, ABB’s standards and customer expectations.
In 2017 we worked with the business continuity teams of the newly established shared service centers to align their emergency and crisis response procedures with ABB’s overall crisis management processes. The four main hubs in Xiamen, Bangalore, Kraków/Tallinn and San Luis Potosi underwent crisis scenario training with representatives from their respective country crisis taskforces to test the plans.
* The number of recorded incidents multiplied by 200,000/total hours worked.