Responsible sourcing Forging a sustainable supply chain
ABB works closely with its suppliers to ensure that its sustainability expectations, ambitions and targets are understood and met
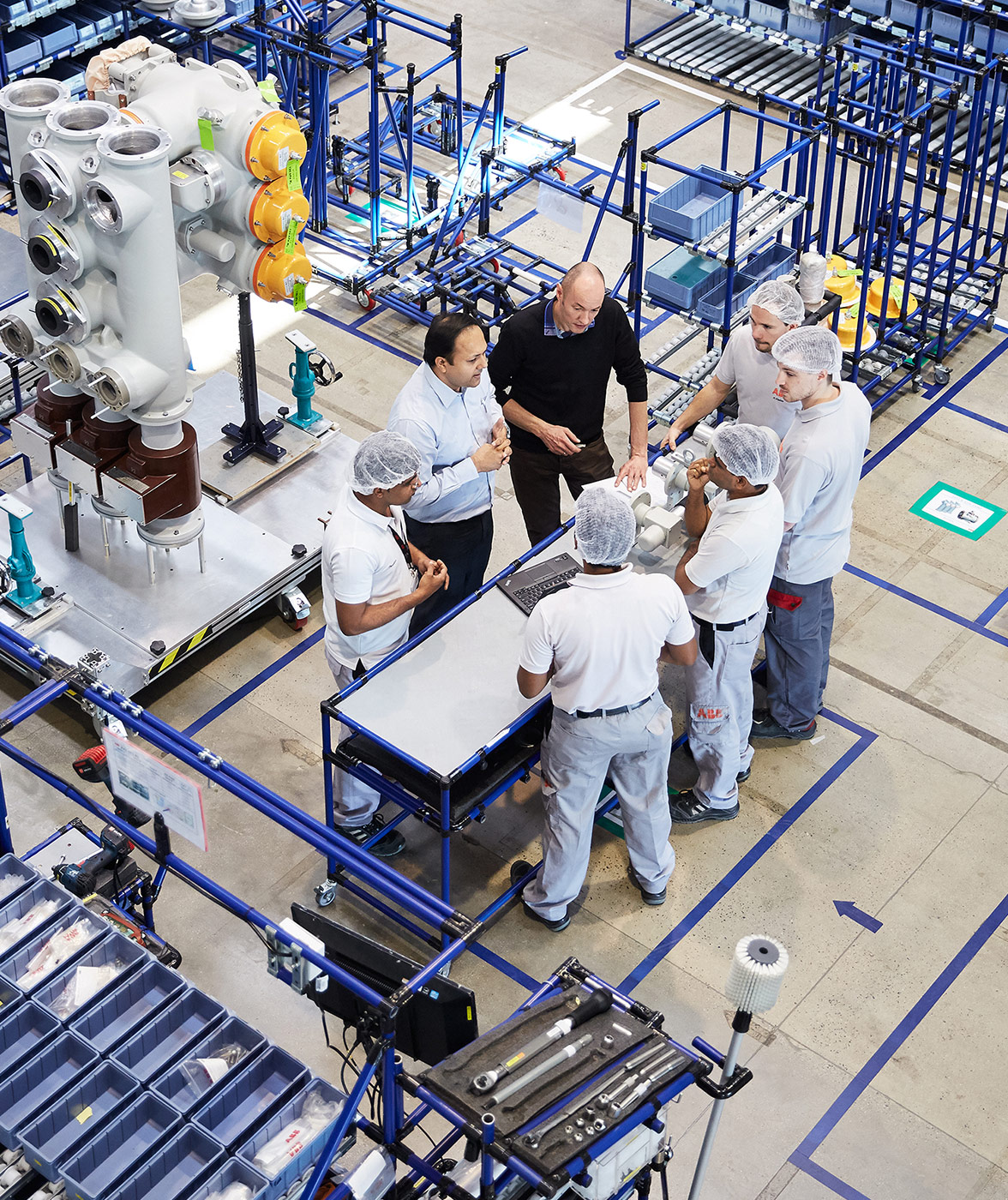
At ABB, we have ingrained our sustainability policies into all relevant procedures. As such, we pay close attention to the sustainability performance of our suppliers. ABB’s mandatory Supplier Code of Conduct (SCoC), which is published in 16 different languages, communicates our expectations, ambitions and performance targets to existing and potential business partners.
All new suppliers to ABB are required to complete our supplier qualification process, in which we assess the sustainability performance of potential business partners at the initial selection stage, along with other business parameters. To become qualified to do business with ABB, new suppliers must certify their compliance with our SCoC. This aspect of our routine supplier evaluation process reiterates our commitment to responsible sourcing.
We have also implemented a rigorous Supplier Sustainability Development Program (SSDP) to proactively identify and rectify sustainability risks with high-risk suppliers. This targeted intervention program features training and on-site assessments to identify areas for improvement and ensure continuous monitoring. The SSDP assesses the sustainability performance of high-risk suppliers on 42 parameters linked to our SCoC. These parameters cover general management, working conditions, health, safety and environment and associated key local regulatory requirements. In addition, we develop special training to strengthen our suppliers’ knowledge of local regulatory requirements and ABB’s parameters.
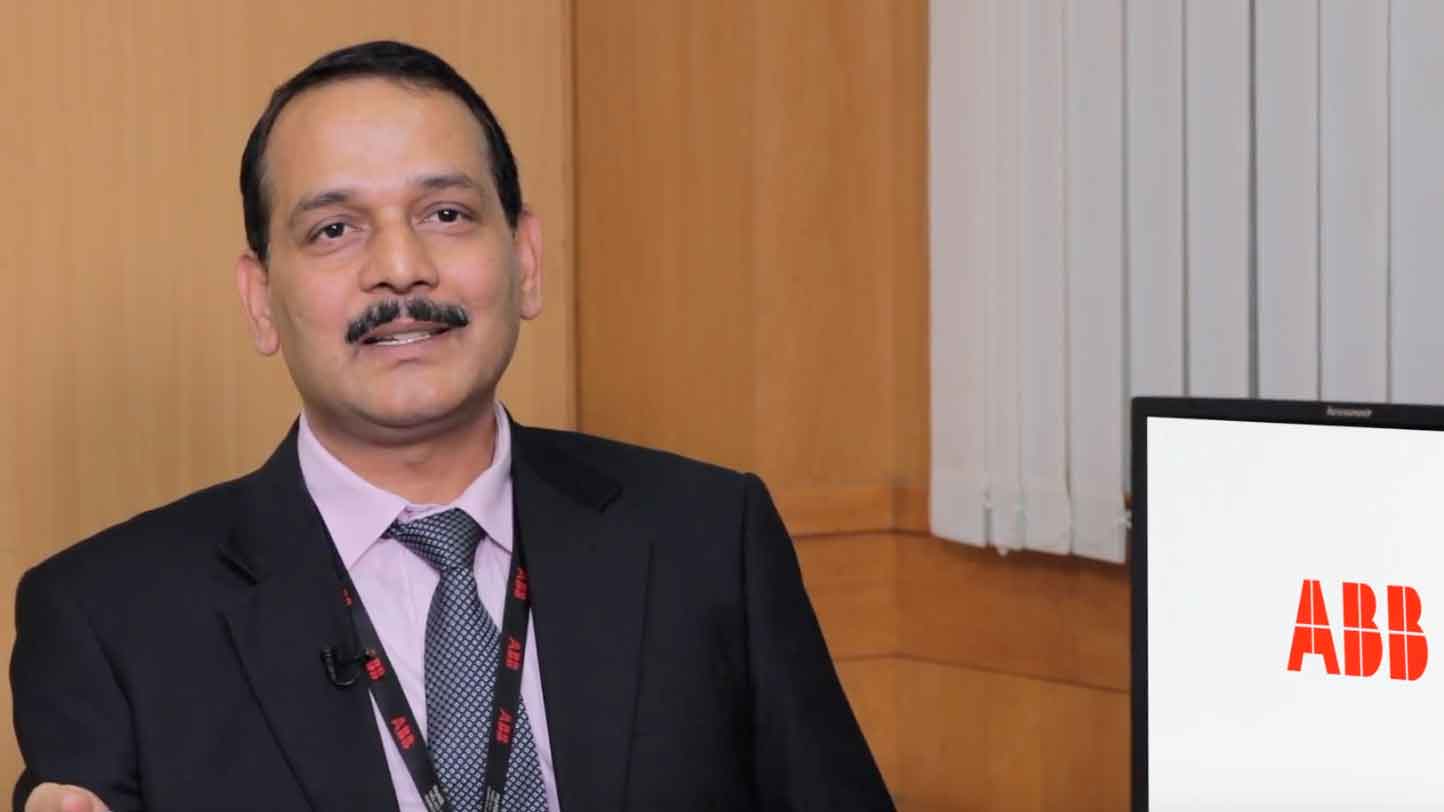
Case study Suyog Electrical
Reveal case studyFor many years, we have worked to source our materials responsibly, using a series of policies and programs that strengthen performance and partnerships in our supply chain. In this effort, we are committed to helping our suppliers improve their performance sustainability and find innovative solutions to chronic challenges.
In a recent example of this commitment, we partnered with Suyog Electrical, a manufacturer of power and signal cables based in Gujarat, India, to reduce excessive working hours.
Our comprehensive approach led to an overall improvement in operational performance in several areas, including a 23 percent increase in on-time deliveries. As a result, the company’s late-delivery penalties fell by 72 percent in the same period and are expected to decrease further. Meanwhile, monthly average overtime hours were cut by more than half, and efficiency at Suyog Electrical’s factory rose by 5 percent, with machine breakdown hours reduced by 43 percent.
The facility has become more productive, is compliant with local labor regulations, and received favorable customer reviews due to its notable improvement in on-time delivery. We continue to engage in similar collaborations worldwide to create a sustainable supply chain and achieve the highest quality standards.
Close case studyEvery year ABB trains, coaches and assesses hundreds of suppliers on sustainability topics. As this is a continuous process, old risks are closed and new ones identified each year. The time required to close these risks ranges from eight months to over a year for chronic or complex issues, which may require a collaborative effort to resolve. Since 2015, we have identified an average of 788 new risks each year. Due to the ongoing identification of new risks and the time required to mitigate them, the closure rate of identified risks can never be 100 percent, despite our best efforts. Going forward, our measure and target for 2020 is to close 65 percent or more of identified risks from supplier assessments. This target is based on a review of our performance over the past few years.
We exceeded our measure and target for 2020, closing 72 percent of identified risks by the end of 2017. Thanks to our strong focus on supplier development, as opposed to simply conducting audits, we were able to engage our suppliers as partners. This approach allowed us to arrive at solutions that will deliver tangible sustainability improvements.
SSDP top 10 global non-compliance issues
Critical and serious issues
- Unsafe working practices
- No first aid or fire-fighting equipment
- Improper waste management
- Environmental non-compliance (statutory)
- Excessive working hours
- No OHS risk assessment
- No environmental risk assessment
- No equipment testing
- No monitoring of compliance
- No environmental licenses
In 2017, we expanded the SSDP’s footprint to three more countries: Bulgaria, Saudi Arabia and the United Arab Emirates. We assessed 243 suppliers, identifying 833 risks and mitigating 702 of them. In other activities to support responsible sourcing, we trained 533 ABB employees and 327 suppliers during the year.
After analyzing the data collected during our supplier assessments, the most frequent critical and serious issues observed were a lack of understanding of the environmental and occupational health and safety (OHS) risk assessments and a failure to comprehend statutory requirements and legal frameworks. To address this, we continued to raise awareness through initiatives such as our specially designed OHS workshops. We also designed and implemented a special workshop in India on statutory and legal frameworks. In 2018, we will conduct comparable workshops in other countries.
We also work with suppliers to seek solutions to chronic problems that are embedded in the local socioeconomic fabric. By supporting them with operational data analysis and visits to their factories to identify root causes and potential areas for intervention, we have been able to arrive at mutually satisfactory solutions.