Resource efficiency Steadily reducing our environmental footprint
ABB is making a concerted effort to use natural resources more efficiently
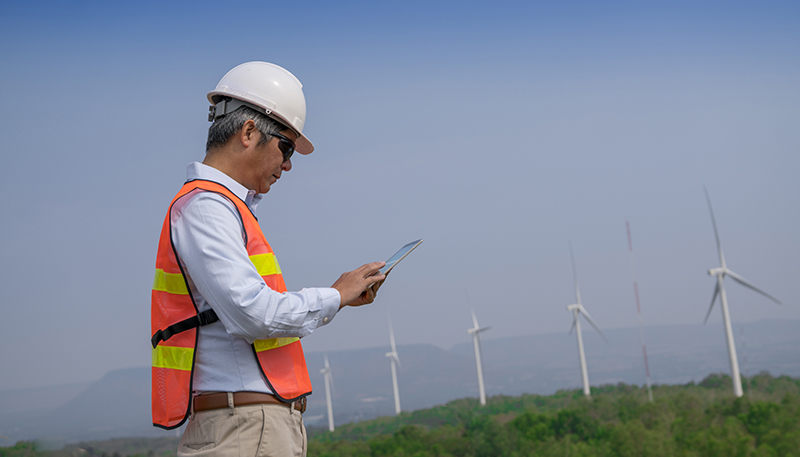
Since 2010, we have launched a large number of waste reduction and recycling programs at our sites around the world. These initiatives are steadily reducing ABB’s impact on the environment and, as an added benefit, are delivering cost savings to our Business Areas.
2020 targets
In the area of resource efficiency, we effectively met the two targets we established for 2020. The first target was to reduce absolute water withdrawals by 25 percent from 2013 to 2020 at facilities located in watersheds with medium to extremely high baseline water stress. While the majority of our manufacturing processes are not water-intensive, we know that clean water is an increasingly scarce resource. As such, we keep a close eye on how water is managed across ABB’s operations.
Water withdrawal in water-stressed areas
* PG not included for 2020
We use the World Resources Institute’s Aqueduct global water risk tool to assess our facilities according to the level of baseline water stress of the local watershed. Of the 446 ABB locations mapped in 2020, 59 face an extremely high level of water stress, 76 face a high level, and 61 face a medium-to-high level. The tool not only helps us assess water stress at our sites, but also the levels of groundwater depletion, flood risk and seasonal variability of water availability at our sites; this data is extremely useful for our work in managing water risk.
For all ABB sites in stressed watersheds, total water withdrawals in 2020 amounted to 1,178 kilotons, representing an 18 percent reduction from 2019 and a 39 percent reduction from 2013, in both cases excluding the impact of the Power Grids divestment and of new sites added in 2019, for which no 2013 baseline data exists.1Total water withdrawals in stressed watersheds, for all ABB sites, was 1,273 kilotons; total water withdrawals for all ABB sites except for the 39 new sites added in 2019, for which no 2013 baseline data exist, was 1,178 kilotons. The latter number is used to calculate our progress versus our target.
Distribution of water withdrawal 2020 (2019)
The divestment of Power Grids reduced ABB’s total water use in 2019 by 58 percent. In 2020, ABB’s water use went down by an additional 12 percent, to 3,224 kilotons. Closed-loop processes and other projects to recycle or reuse water comprise our primary water-saving practices; in 2020, such processes and projects saved 30 percent of all industrial water use and 53 percent of all cooling water use at ABB sites worldwide. There are 25 projects running to improve water management across ABB, with expected annual savings of 24 kilotons, or 0.75 percent of all the water we use. As an example of the type of projects we implement, consider the work we did over the past year at our site in Bad Berleberg, Germany. Because the site is located in an area of high water stress, we installed a closed loop system for its cooling water. This system, which is expected to reduce the site’s freshwater use by roughly 65 percent compared to a 2019 baseline, has already reduced the site’s water consumption by 20 percent since becoming operational.
Our second resource-efficiency target was to reduce the share of waste ABB sends to final disposal – both hazardous and non-hazardous – by 20 percent from 2013 to 2020.
Waste and recycling
* PG not included for 2020
In 2020, the divestment of Power Grids changed the waste generating and waste recycling structure of ABB. Back in 2013, the share of waste sent to final disposal by the Business Areas that presently remain in ABB was already lower than the 20 percent target we set for ourselves at that time. From that level, we have reduced the share of waste we send to final disposal by another 3 percent. The share is now down to 14 percent.
In 2020, ABB reduced the amount of total waste it generates by 25 percent and reduced its disposed waste by 27 percent compared to 2013.2We have re-baselined our waste data and removed the contributions of Power Grids to the 2013 baseline. This includes all ABB sites except for the 39 new sites we added in 2019, for which no 2013 baseline data exists. Over the past year, in-house recycling and reuse, mainly of packaging materials and thermoplastics, reduced the amount of waste ABB generates by 1,700 tons.
To increase transparency and drive improvement, in 2019 we started asking our sites to be more specific about how their general waste was disposed. This approach revealed that more than 40 percent of the general waste ABB sent for disposal that year was subject to incineration with energy recovery (i.e., the conversion of non-recyclable waste materials into usable heat, electricity or fuel through a variety of processes).3 In 2020, this share was 38 percent.The new definitions for reporting the disposal of non-hazardous waste, revealed a difference in how our sites around the world have reported ‘non-hazardous waste sent for incineration with energy recovery’ in the past. Our analysis shows that in 2018, roughly 75 percent was reported as disposed and roughly 25 percent as recycled.
Major initiatives in 2020
We implemented more than 60 recycling and waste reduction projects in 2020. These projects trimmed the amount of waste we generate each year by nearly 400 tons, while delivering annual savings of some $260,000. More than 80 percent of these projects have a payback period of less than two years.
To illustrate the type of projects we favor, consider our site in Westville, Oklahoma, USA, where ABB’s Motion Business Area manufactures AC and DC industrial electric motors. There, we adopted the practice of mixing paint directly at the paint booth, instead of pumping it across the factory from the storage facility. This adjustment, which reduced the site’s paint waste by more than 15 tons and delivered over $40,000 in annual savings, also reduced the amount of paint thinner used for viscosity adjustments and cleaning.
Another example of how we work to reduce waste comes from ABB Electrification’s Protection and Connection site in Vaasa, Finland. There, we have started to dismantle faulty or otherwise returned products and parts. We reuse the copper we recover, together with select parts, and send the remainder for recycling. This new process saves $55,000 per year. Also in Finland, our MOMG Espoo subsidiary purchased a second-hand cardboard shredder so it could reuse received packaging as padding for outgoing packages. The shredder, which cost $1,700, will pay for itself in less than one year.
In a particularly interesting example of how waste can be reduced even through the simplest of measures, one of ABB’s large office buildings in Baden, Switzerland, stopped using disposable cups. Previously, the 800 employees at the building used some 1 million disposable cups per year. By ending this wasteful practice, the building significantly reduced the amount of plastic garbage it generated, while saving $61,000 per year. With the help of strong change ambassadors, the building’s management team was able to effect a major change in the habits of the people working there.
Steel, copper, aluminum, oil and plastics make up the majority of the raw materials used in our products. Most of these materials are reclaimable at the end of a product’s life, and ABB deliberately designs its products to be recycled; almost all of our products come with recycling instructions and can be easily dismantled.
Across ABB, we have also taken steps to implement the principles of the circular economy to reduce waste. To drive this process further, in 2020, ABB joined the Ellen MacArthur Foundation, whose mission is to accelerate the transition to a circular economy.
A product sustainability competence team was formed in Dalmine, Italy, in 2020; the team will provide ABB’s Distribution Solutions business with assessments of the impact of its products’ lifecycles.
Case study ABB makes manufacturing more sustainable by recycling and remanufacturing thousands of old robots
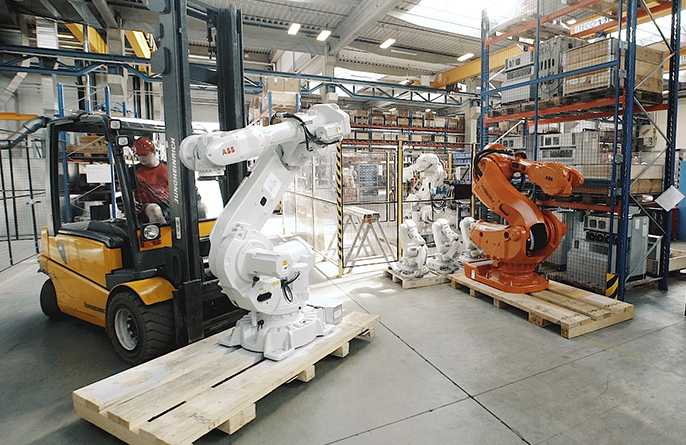
Lessons learned
During the sustainability cycle ending in 2020, we learned the value of setting targets that can be easily understood. Our targets, to take less water from stressed watersheds and to generate less waste, were concrete and measurable. It was not difficult to convince our people of the importance of these targets, and thus our water and waste recycling programs were readily accepted and implemented. As with our GHG emissions reduction target, our waste and water targets generated pride across ABB. They confirmed our people’s belief that the work they do is geared towards building a sustainable future for future generations. We realized that our environmental targets serve, in fact, to back up our company’s claims with hard numbers regarding our own performance improvements in key areas over time. In a sense, our environmental targets contributed to the formation of an implicit purpose for our company. We are thus pleased to see that ABB’s environmental contributions have been incorporated into our company’s new Purpose statement.
Finally, we learned that our work to use resources efficiently was not only a risk mitigation strategy, but also a significant business opportunity. This important lesson will translate well into our new sustainability strategy.