Right materials Eliminating unsafe materials from our operations
ABB continues to remove hazardous substances from its products, processes and supply chain
We rely on the ABB List of Prohibited and Restricted Substances to guide the process of reducing and, where possible, eliminating hazardous materials. This list applies to all our operations, including procurement, product development, production processes, products, packaging materials, service activities and construction sites, and is updated twice per year in keeping with international regulations, in particular the EU REACH regulation.
ABB’s General Terms and Conditions for suppliers and our Supplier Code of Conduct cover prohibited and restricted substances in the context of regulatory compliance. To help suppliers meet their obligations – which include partnering with us to identify restricted substances and conflict minerals and prevent them from entering ABB’s supply chain – we have developed a companion guide to the above-mentioned list.
Our 2020 target for hazardous substances was to reduce ABB’s emissions of volatile organic compounds (VOCs) by 25 percent from 2013 levels. Since 2013, ABB has reduced its VOC emissions by 29 percent by using low-VOC paints and varnishes and installing active carbon filters and other equipment at our production sites We have re-baselined our VOC data and removed the contribution of Power Grids to our 2013 baseline. The baseline includes all ABB sites except for the 39 new sites we added in 2019; no 2013 baseline data exists for these new sites..
In 2020, 14 new projects got underway to reduce and phase out hazardous substances and VOC emissions. Due to the variety and specialized nature of our Group’s products and processes, the reduction of hazardous substance is typically handled on a site-by-site basis.
Projects underway to reduce and phase out hazardous substances and VOC emissions
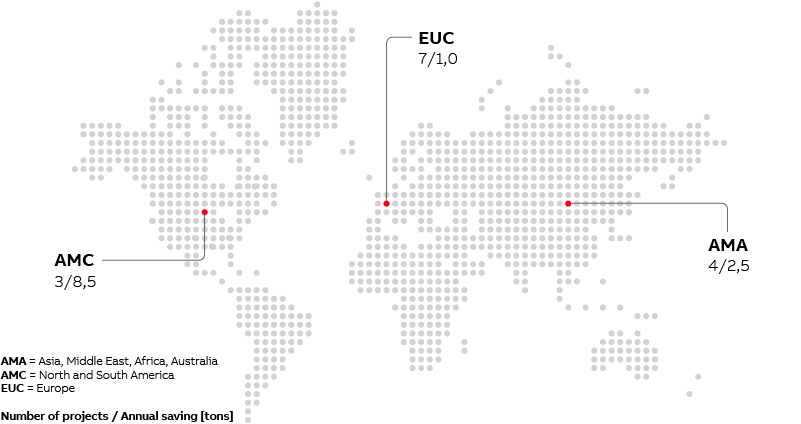
Among the major initiatives underlying these achievements was a screening program that our Electrification Business Area developed with its suppliers. The program monitors and eliminates hazardous substances from components supplied to ABB. In 2020, this program gathered data on more than 275,000 product components and worked with more than 8,500 active suppliers to satisfy our mutual obligations under the European Union’s REACH and RoHS regulations.
Emissions of volatile organic compounds (VOC)
* PG not included for 2020
The dedicated, corporate-led Product Stewardship & Material Compliance program we created in 2019 continued to deliver results in 2020. The program worked closely with our four Business Areas and 20 divisions to provide expert support on the increasingly challenging regulations and standards for chemical substances used in products and industrial operations. It also coordinated our cross-functional material compliance team and our material compliance network to help ABB comply with EU requirements regarding those chemicals and products listed in the Substances of Concern in Products (SCIP) database. This support included providing guidance to ABB’s Business Areas, sites and R&D to minimize the environmental impact of our products and our production facilities.
This support helped our Business Areas assume full ownership of their respective product material compliance duties while maintaining effective, cross-Business Area collaboration. In 2020, we assigned and transferred dedicated specialists to work directly within the structures of our four Business Areas and our 20 divisions. From this new vantage point, our specialists are at once closer both to ABB’s customers and to its suppliers.
Lessons learned
During the current sustainability reporting cycle, we learned that our work to use the “right materials” was becoming increasingly complex over time. In particular, the process of managing and/or eliminating hazardous substances from our processes has been so complex that only the most experienced and skilled of our people are qualified to oversee this task.
Furthermore, we learned that effective product stewardship demands systems, processes and standards. Again, the increasing complexity of this topic has meant a strong framework is essential to success. Another lesson we learned was that the expertise and knowledge gained at one of our sites through a piloted “trial-and-error” approach could readily be systematized and then transferred to other sites.