Safe operations Uncompromising in pursuit of zero harm
ABB’s four Business Areas are committed to reducing lost time injuries to employees and contractors alike
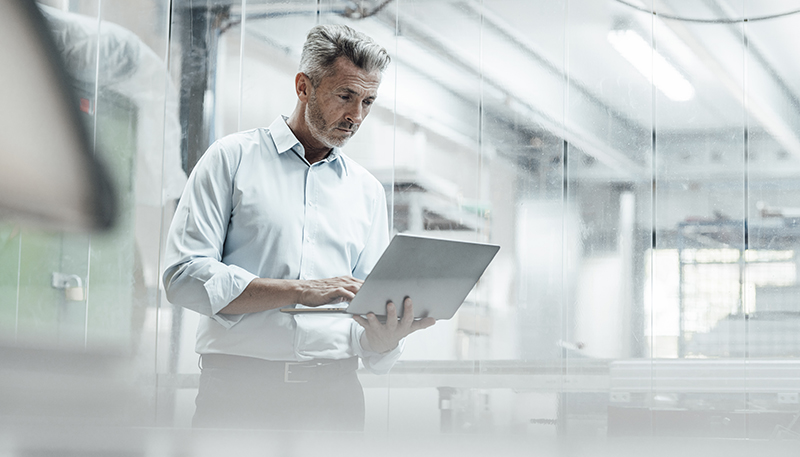
Making ABB a safer place to work is our highest priority. Our goal is that everyone who works at ABB returns home safely every day. Keeping our people safe is not only a moral obligation, it is vital to our long-term success; it underlies our reputation and standing as the right partner for our customers and other stakeholders.
2020 target
In 2020, we exceed our target of reducing ABB’s employee total recordable injury frequency rate (TRIFR) to less than 0.7. We ended the year with a TRIFR of 0.31, down from 0.47. I terms of actual injuries, we improved from 744 recordable incidents in 2019 to 410 in 2020.
ABB has built up an extremely robust safety program over the past decade, and our Business Areas have been implementing programs that have proven to be extremely effective in terms of significantly reducing or eliminating conditions that can lead to incidents. For these reasons, we not only achieved our 2020 safety target three years ahead of schedule, but also consistently reduced ABB’s incident rate over the past eight years. Given the strength of our safety program and the depth of our commitment, we believe that it will soon be possible for ABB to record zero incidents every calendar year. Everything we do is calibrated to achieve this uncompromising result.
Regrettably, ABB recorded one employee fatality and one contractor fatality in 2020. Both incidents were comprehensively investigated to understand their root causes, with action taken to mitigate the risk of similar incidents in the future.
It should be noted that the number of recorded incidents in 2020 was almost certainly impacted by the COVID-19 pandemic. Travel restrictions and social distancing requirements meant that far fewer people were on site, limiting the likelihood of injuries. Those who did work at ABB or customer sites had to comply with the more stringent measures and safety precautions that were put in place to prevent people from either contracting or transmitting COVID-19; these measures and precautions also served to limit the possibility of injury.
HSE/SA Management System
In 2020, we focused our efforts on reviewing and streamlining ABB’s Health, Safety and Environment (HSE) and Security policies, requirements and guidance. Over the year, we worked to simplify the standards within this set of documents – referred to internally as the The ABB Way for HSE and Security Management System – so that they could be quickly and easily consulted by our employees and contractors.
At the end of our revision process, we had produced a complete set of clear and simple one- and two-page documents detailing the mandatory HSE requirements for all of our Business Areas around the world, which came into force on January 1, 2021. These requirements will be distributed in 2021 together with a guide to their implementation.
Additionally, in 2020 the different standards of the HSE/SA Management System that comply with the requirements of the ISO 14001 and 45001 standards were translated into 17 languages; this will facilitate the interpretation and implementation of these standards by ABB staff around the world.
HSE/SA Management Information System
In 2020, we continued to introduce new mobile and desktop applications for our single Management Information System (MIS) for ABB’s health, safety, environment and security function and for its Sustainability function. Accessible around the globe, the MIS can be used by ABB employees and contractors to report information and assign actions related to these functions. This streamlines reporting and enables us to view data on the MIS in charts, graphs and other formats so that we can better analyze risks and trends before taking remedial actions.
We also launched a new app for incident reporting and management at the beginning of 2020. Available to all ABB employees around the globe, it enables our people to more comprehensively file reports on health and safety, environmental and security incidents. Reported incidents are then verified and classified by an ABB HSE/SA professional and, depending on their severity, investigated.
These apps significantly improve our incident reporting and management process by helping us to better identify underlying causes of incidents, learn from them, and take action to eliminate them. By investigating all errors that contribute to an incident, we can understand, support and educate persons involved in incidents where human error is identified as one of the contributing factors.
Creating a positive HSE & Security and Sustainability culture in ABB
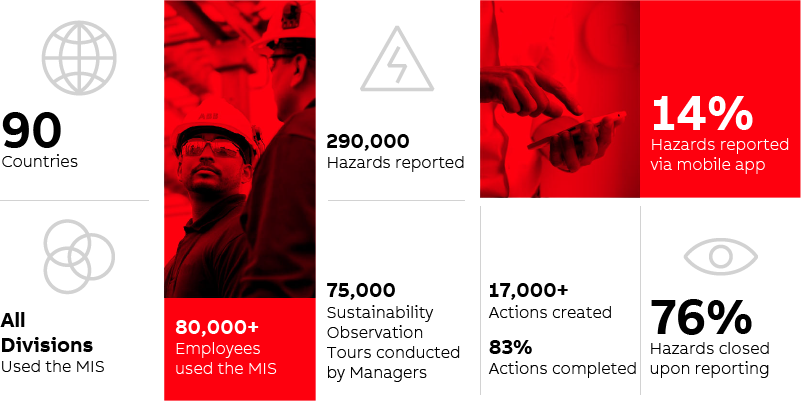
Overall, our single MIS system continues to be a huge success; in 2020, its apps were used by more than 80,000 people in all four Business Areas in every country where we operate.
Electrical safety
In 2020, our Global Electrical Safety Program (GESP) continued to deliver exceptional results. Since its inception in 2015, we have reduced the total recordable electrical injuries by 87 percent. Over the same five-year period, we have also reduced the number of serious electrical incidents by 85 percent.
Electrical safety incidents are in our top three of causes of serious incidents and a reminder of the high consequence danger our personnel face when working with electricity on a daily basis. In response to a rise in the total number of electrical incidents last year, we took action by implementing the final stage of a core part of our GESP, called the Electrical Competency Authorization Program (ECAP). This program includes a formal assessment of an employee’s technical competence, which considers their electrical education, training, experience and qualifications as set forth on their pre-assessment CV. When evaluating employees, our ECAP assessors conduct one-on-one interviews before making a recommendation to the respective local responsible manager. The manager then provides written authorization to certify that the employee can carry out work activities involving electrical risk at one of four defined levels of electrical competence (Level 1, Electrical Trainee; Level 2, Electrically Competent Person; Level 3, Electrically Authorized Person; and Level 4, Senior Authorized Person).
While ECAP serves to prevent personnel from being exposed to electrical risks beyond their capacity, it also permits ABB employees to advance from level to level based on subsequent experiences, courses, trainings, and qualifications. We firmly believe that the ECAP is an industry-best practice that will eventually enable us to eliminate electrical incidents at ABB.
Assurance & risk
Because the COVID-19 safety restrictions prevented most of our on-site visits in 2020, we were only able to conduct 41 confirmed audits – substantially fewer than the 180 audits we performed in the previous year. Nevertheless, we identified 169 incidences of non-conformance reporting (NCR), 205 opportunities for improvement and 69 good practices. In 2020, our on-time closure rate for NCRs was 97 percent. Since the training of our auditors is conducted in classrooms, not remotely, we were only able to train 33 persons in this discipline over the past year, down from 130 last year.
In 2020, our four Business Areas began the process of conducting detailed audits of their own operations. In all, they performed around 1,899 “self-assessments” over 383 separate programs.
Regarding risk, we have launched the Activity Based Risk Assessment (ABRA) course, process and module in MIS. This process unifies and improves the way in which we identify, classify and control operational risks from our activities. So far we have remotely trained 85 people, with 33 passing the course; 190 more colleagues are scheduled to take the course in the first few months of 2021.
Training and competence programs
Due to the COVID-19 pandemic and internal restructuring, it was not possible to run our corporate HSE/SA training and competence programs to the extent we had originally planned. To address this challenge, we began to adapt, pilot and deliver our existing programs virtually to priority target groups.
These actions brought us faster to our long-term goal to shift from face-to-face to more hybrid and virtual training and competence programs. In 2020, we mainly focused on virtually delivering our resilience and incident investigation programs, as well as the Actions-based Risk Assessment Training and Safety Master Class. For our new virtual resilience program, we trained nearly 50 trainers in 2020. In addition, more than 100 managers had joined a virtual Safety Master Class by the end of 2020, while the global community of Safety Master Class trainers successfully participated in virtual train-the-trainer sessions.
Lessons learned
During the 2020 sustainability reporting cycle, we learned the value of setting an extremely aggressive target for safety. Our aggressive target, in combination with our clearly stated goal for there to be zero incidents at ABB, raised the bar for all employees. This enabled us to achieve our target in advance and, ultimately, to exceed our target.
Another lesson we learned during the previous cycle was related to business continuity. During the process of managing ABB’s response to the COVID-19 pandemic, we realized that ABB’s decentralized divisions must collaborate at the country level to ensure a unified and consistent approach to the health and safety of all ABB employees. We are confident that the lessons we learned over the course of 2020 will serve us well in the years to come.
Finally, in 2020 we learned the true value of sharing best safety practices from one business to another. The ABB Business Areas that were first affected by COVID-19, such as our operations in China, were able to advise our operations in other countries on best practices for protecting our people and ensuring business continuity during lockdowns. This greatly reduced the time they needed to develop new health and safety measures in response to the pandemic.