Circularity
Target 2030: At least 80 percent of ABB products and solutions will be covered by our circularity approach
At ABB, we work with our value chain partners to drive sustainable development. To reduce the environmental impact of ABB’s operations, products and solutions, as well as to preserve the earth’s resources for future generations, we want to enable our customers and suppliers to become more circular and drive circularity across our value chain.
To develop and coordinate our circularity initiatives, ABB has established a cross-business area circularity working group. The goal of this working group is to develop a robust, objective, quantifiable and auditable framework that captures the circularity of our product portfolio. We recognize the need to incorporate external standards into this process and are therefore working to align our framework with existing external reporting standards and related regulations. These include the EU taxonomy for sustainable activities, the Corporate Sustainability Reporting Directive (CSRD) and GRI Standards, among others. By conducting a gap analysis and reinforcing governance, we aim to finalize our approach to regulatory alignment in 2023.
ABB’s circularity KPIs address all phases of the product life cycle. They were developed so we could set ambitious targets and move forward in a coordinated manner, while taking into account the wide range of solutions offered by our divisions and the diverse needs of the customers we serve.
All of ABB’s four business areas strengthened their circularity implementation plans over the past year. ABB Electrification introduced circularity KPIs into performance management processes and mandated all divisions to develop circularity plans and commit to quantitative targets through 2025. ABB Motion assigned circularity target leads for each division and launched seven cross-division circularity initiatives. ABB Process Automation designated circularity leads and teams for each division and formalized its top circularity priorities. These included sourcing alternatives to plastics, conducting further life cycle assessments (LCAs), and providing a broad range of services to extend the useful lives of systems and technologies already installed at our customers’ sites. ABB Robotics & Discrete Automation started to conduct LCAs for all of its top-selling robots, as well as for every new product it develops.
In 2022, we also created the ABB Circularity Approach Guidelines. These guidelines clarify the purpose of our circularity approach, define KPIs, and establish principles for the assessment of ABB products and solutions.
To support our customers’ circularity journeys and highlight the circularity performance of ABB products, in June 2022, we launched the EcoSolutions™ label. To be marketed under this product category label, products must provide transparency into their environmental impacts, both through a third-party verified environmental product declaration (EPD) and a circularity KPI assessment under the ABB framework.
Looking ahead, we are continuing to work with our customers and partners on the development of innovative business models that would enable our entire value chain to become increasingly circular. Such models are critical if society is to transition from a linear “take-make-waste” economy to a circular “borrow-use-return” economy.
Case study Upcycling recovered marine plastic while showcasing the future of retail
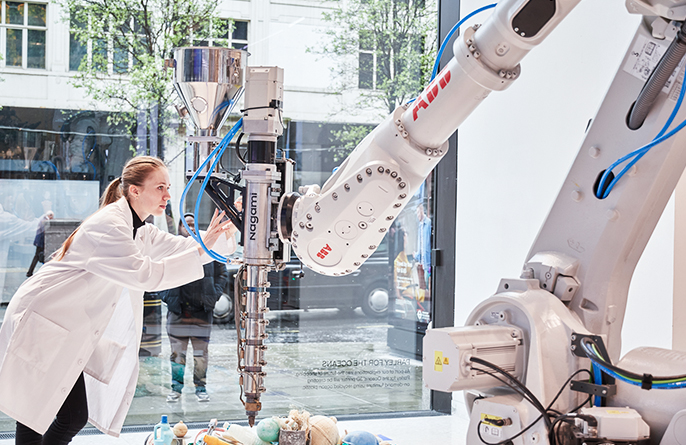
How ABB is going full circle
Product design and sourcing
In 2022, we began the process of reviewing and modifying product designs wherever practicable. For example, teams at ABB Motion are redesigning their motors so they can be more easily disassembled. The purpose of this is to reap the full benefits from the 98 percent recyclability rate of these products.
In terms of sourcing, we worked to identify fully renewable, recyclable or biodegradable resource inputs for our manufactured products. Our business areas are gradually raising the bar for supplier qualification and management processes by requiring suppliers to address the circularity of supplied materials and components. The teams also sought to identify viable alternatives to the conventional plastics and metals used in some products.
Production and packaging
In 2022, ABB continued to develop and implement circular solutions for its production processes and packaging materials. Many of the best ideas that were implemented over the course of the year were devised by local teams at our production facilities.
For example, the team at ABB’s Portland, Tennessee (USA), factory came up with a way to repurpose scrap plastic from its injection molding processes. By grinding the scrap into pellets and using it as part of a 25 percent recycled/75 percent virgin mixture in production, the facility was able to cut the amount of waste it sends to landfill each month by more than nine metric tons.
Similarly, the team at ABB’s St. Louis, Missouri (USA), plant identified a way to reuse scrap from the manufacture of motors, recovering 26,308 metric tons of electrical steel per year. When the plant’s primary electrical steel supplier purchased a local recycling company, ABB’s team realized they could sell the electrical steel scrap back to their supplier; in turn, the supplier pays ABB an above-standard price for the scrap because they can be certain that the material is of the highest quality.
ABB continued to replace conventional plastics in its packaging with either recycled or bio-based materials. ABB Electrification’s Smart Power division, for example, ran a pilot project in 2022 to improve the environmental performance of its packaging and reduce transport emissions. The project adopted an eco-design approach, based on LCAs. Packaging was analyzed based on its geographical origin, transportation distances and the overall environmental impact of its materials, among other factors. Focused on the packaging of Ekip Up digital units, the project yielded strong results. The new packaging is completely plastic-free, uses FSC-certified cardboard and has led to reductions in total cost, environmental impact and weight of the packaged unit, while providing the same level of protection.
Another sustainable packaging pilot project was undertaken by the team at ABB’s factory in Frosinone, Italy, in collaboration with ABB’s Research Center in Switzerland. Together they developed 100 percent recycled PET plastic blister packs. These will replace the virgin plastic blister packs used for the factory’s low-voltage breaker accessories in early 2023. And ABB Robotics & Discrete Automation developed new packaging for B&R’s ACOPOS servo drive; the new packaging is 50 percent smaller and 30 percent lighter. Another small adjustment that yielded big results was their decision to ship B&R X20 series I/O and controls in the customized configurations requested by their customers, rather than shipping each component separately.
Use phase
We offer our customers a number of ways to extend the life of their equipment. Retrofits, for example, extend the service life of existing drives and allow customers to replace only the necessary components. By retaining the equipment’s original cabinets, cabling, electrical components and automation systems, retrofits make it possible to modernize machinery with minimal expense, waste or interruption to normal operations. The life of the asset can be extended, while adding features and functionality that enhance safety, reliability and performance. As another example, we offer retrofit solutions that not only extend the service lives of marine vessels but also convert them to operate in hybrid and zero-emission modes.
ABB also has expertise in reconditioning aging assets to improve their reliability, performance and service life. In 2022, for example, ABB replaced the outdated ACS800 converters in 24 wind turbines operated by Enefit Green, the largest wind energy producer in the Baltics.
The decision to recondition old equipment is especially important in light of the quantity of GHG emissions involved and the materials required for the manufacture of new equipment. At the same time, reconditioning or rebuilding existing equipment is typically very cost-effective, for assets both large and small. In 2022, Sala Heby Energi Elnät AB, a Swedish electrical distribution company, had ABB refurbish 50 of its HPA circuit breakers, which had been manufactured in the 1980s. The customer was pleased to receive refurbished switches that will last another 20 to 25 years, for half the cost of replacement products.
ABB also offers digital solutions that enable our clients to extend the lives of their assets through optimization, remote operations and preventive maintenance. For example, Gallo NV, a leading Belgian recycling company, implemented ABB Ability Condition Monitoring for powertrains at its facility. By leveraging data insights and service expertise provided by ABB, Gallo has reported a significant increase in uptime and extended the service life of its machinery, with a payback period of just one year.
In addition, some of our divisions began to work with their customers to develop new business models that could drive circularity across the value chain. For example, in 2022, ABB Motion in Sweden piloted recycling incentives, which are now being rolled out to other countries in Europe.
End of life
In 2022, ABB continued to apply circularity principles to the end-of-life phase of our product portfolio. For example, to further improve the recyclability of ABB’s Azipod® electric propulsion systems, we made the materials used in their fabrication easier to reclaim and provided customers and recycling companies with clear end-of-life instructions. Up to 95 percent of the materials used in the production of the Azipod propulsion system is recyclable.
Additionally, ABB has entered partnerships with third-party companies to recycle batteries. One such partnership, between ABB Switzerland and Librec, a Swiss recycling company, assures that industrial batteries produced by ABB will be 90 percent recycled. As local legislation requires all battery manufacturers to either ensure end-of-life management or pay a disposal fee in advance, the partnership is good for the environment while reducing costs for ABB.
Over the last 25 years, ABB’s remanufacturing teams have given thousands of used robots a second life by refurbishing or upgrading them. Peripheral equipment, such as controllers and manipulators, is also refurbished to “like-new” condition at ABB’s Global Remanufacture & Workshop Repair Centers. Among these is the new robot refurbishment center that we opened in Mosnov (Czech Republic) in 2022. By offering this service, ABB makes it possible for existing customers to sell their redundant robots and equipment back to us rather than scrapping or mothballing them. A life cycle assessment carried out in 2021 revealed that robot refurbishment releases roughly 75 percent fewer GHG emissions than manufacturing a new robot. For robots and other equipment that can no longer be refurbished, ABB has a specialized team that disassembles and sorts the component materials for recycling.